Manual surface finish for rapid prototyping has a rich history rooted in the meticulous craftsmanship and attention to detail that characterize the manufacturing industry. As technology has advanced, the demand for high-quality prototypes with superior surface finishes has only increased. In modern CNC factories equipped with state-of-the-art 3-axis and 5-axis CNC machines, the need for manual surface finish persists, especially among high-end clients who prioritize precision and aesthetics.
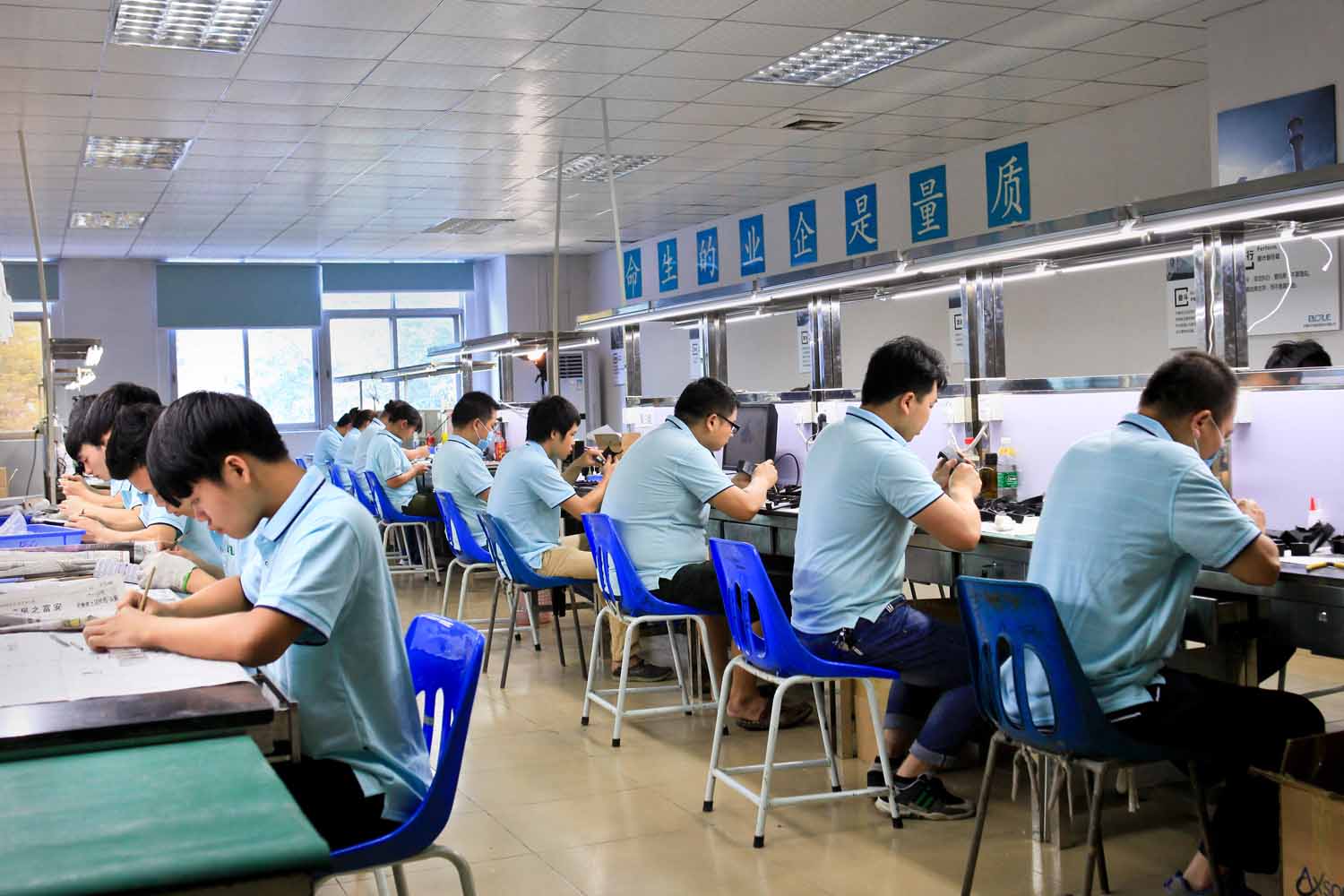
To produce a top-quality prototype, we need to use both CNC machines and manual surface finish for rapid prototyping
Let’s focus on WHAT AND HOW about this type of manual surface finish in this article.
The Importance of Manual Surface Finish in Modern CNC Factories
Despite the capabilities of advanced CNC machines, manual surface finish remains essential for several reasons:
Precision: Manual surface finish allows for fine-tuning and customization that automated processes may not achieve, ensuring the highest level of precision in prototypes.
Aesthetics: High-end clients often require prototypes with impeccable surface finishes to showcase the quality and attention to detail of their products.
Customization: Manual surface finish offers flexibility in tailoring the final appearance of prototypes to meet specific design requirements and aesthetic preferences.
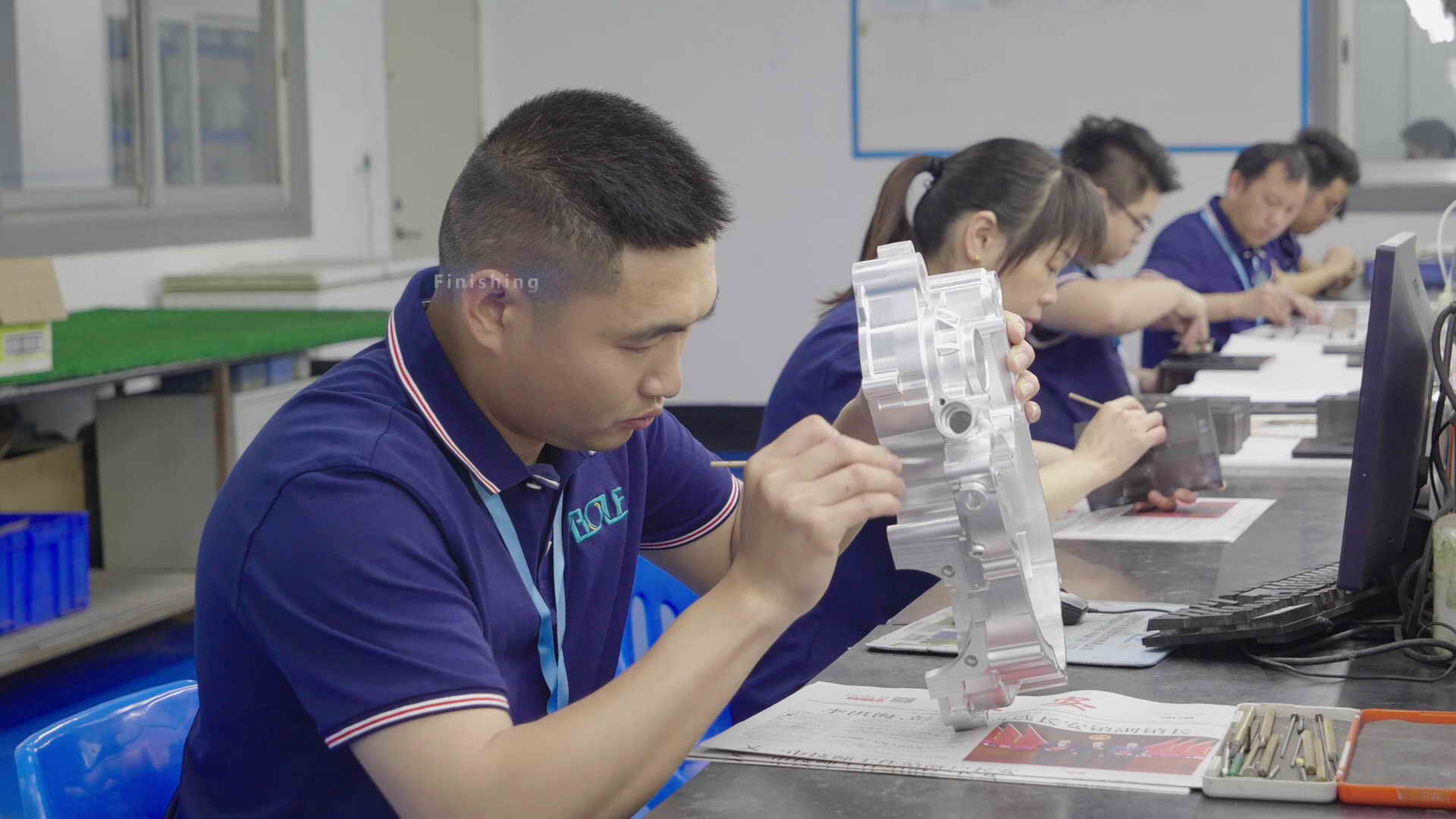
Regular Manual Surface Finish Treatments for Different Materials and Applications
Polishing: Polishing is a common surface finish treatment that enhances the smoothness and luster of prototypes, making them visually appealing. It is suitable for materials like plastic, metal, and resin.
Sanding: Sanding is used to remove imperfections, rough edges, and surface irregularities from prototypes. It is particularly effective for achieving a uniform surface texture.
Painting: Painting is a versatile surface finish treatment that allows for customization in color, texture, and finish. It is ideal for prototypes that require a specific aesthetic or branding.
Anodizing: Anodizing is a process that creates a protective oxide layer on metal prototypes, improving their corrosion resistance and adding color options.
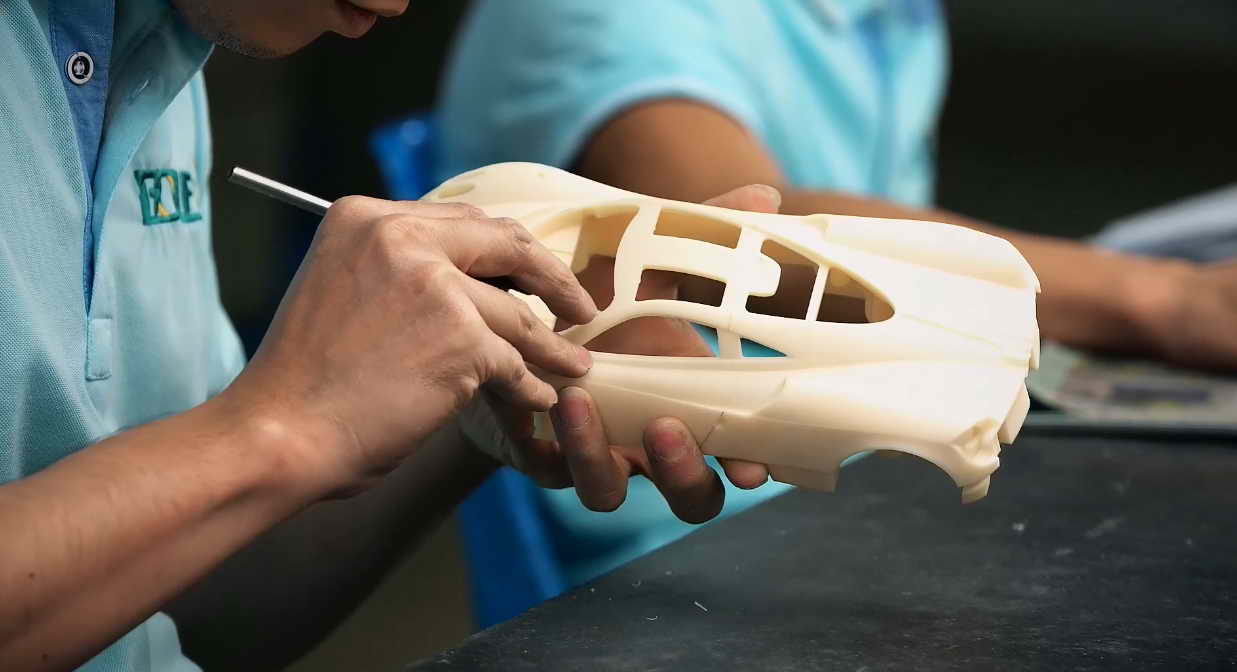
Tools for Manual Surface Finish
Sandpaper: Various grits of sandpaper are used for sanding and smoothing surfaces.
Polishing Compound: Polishing compounds help achieve a high-gloss finish on metal and plastic prototypes.
Paint and Brushes: High-quality paint and brushes are essential for painting prototypes with precision and uniformity.
Anodizing Kit: An anodizing kit includes chemicals and equipment needed to perform the anodizing process on metal prototypes.
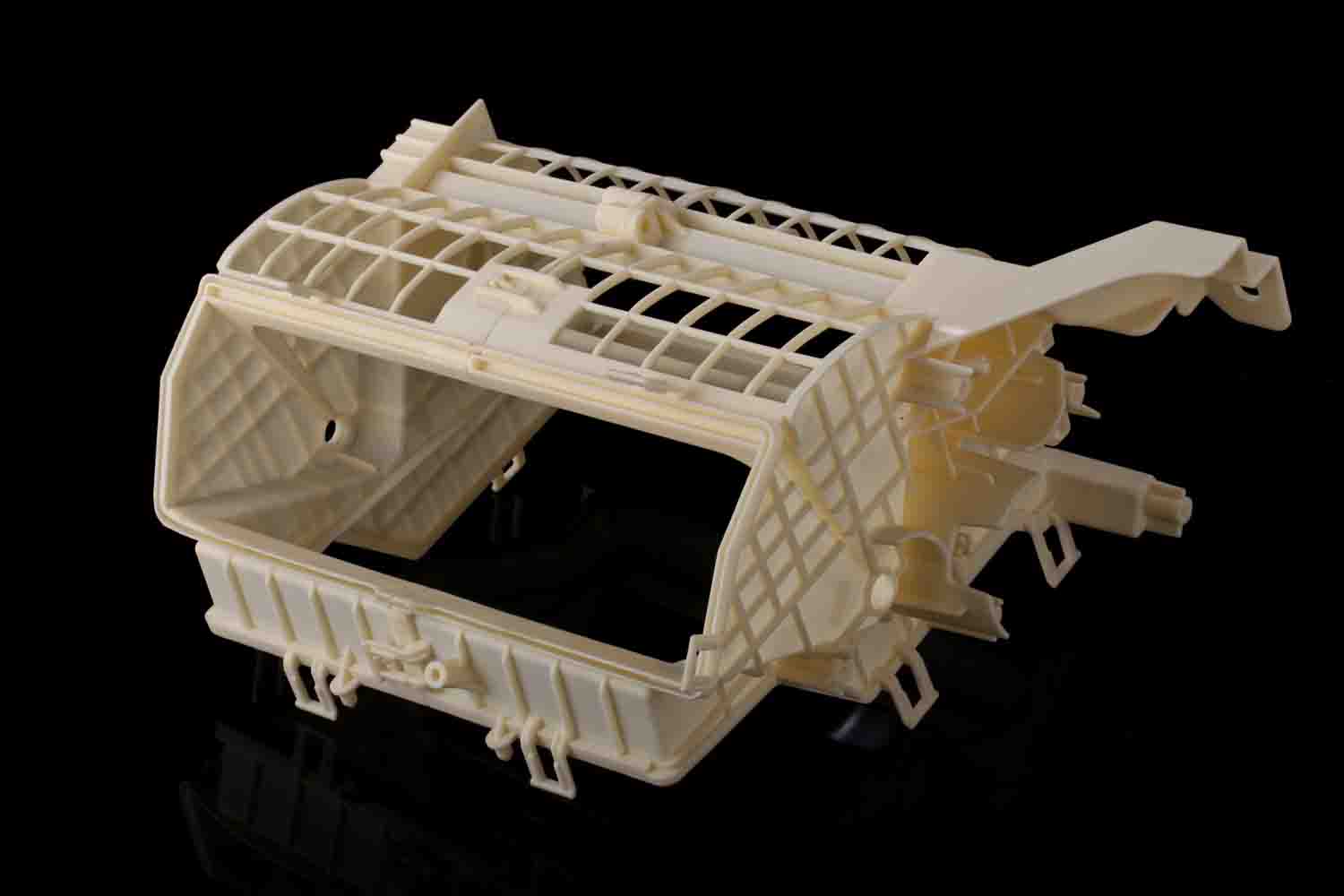
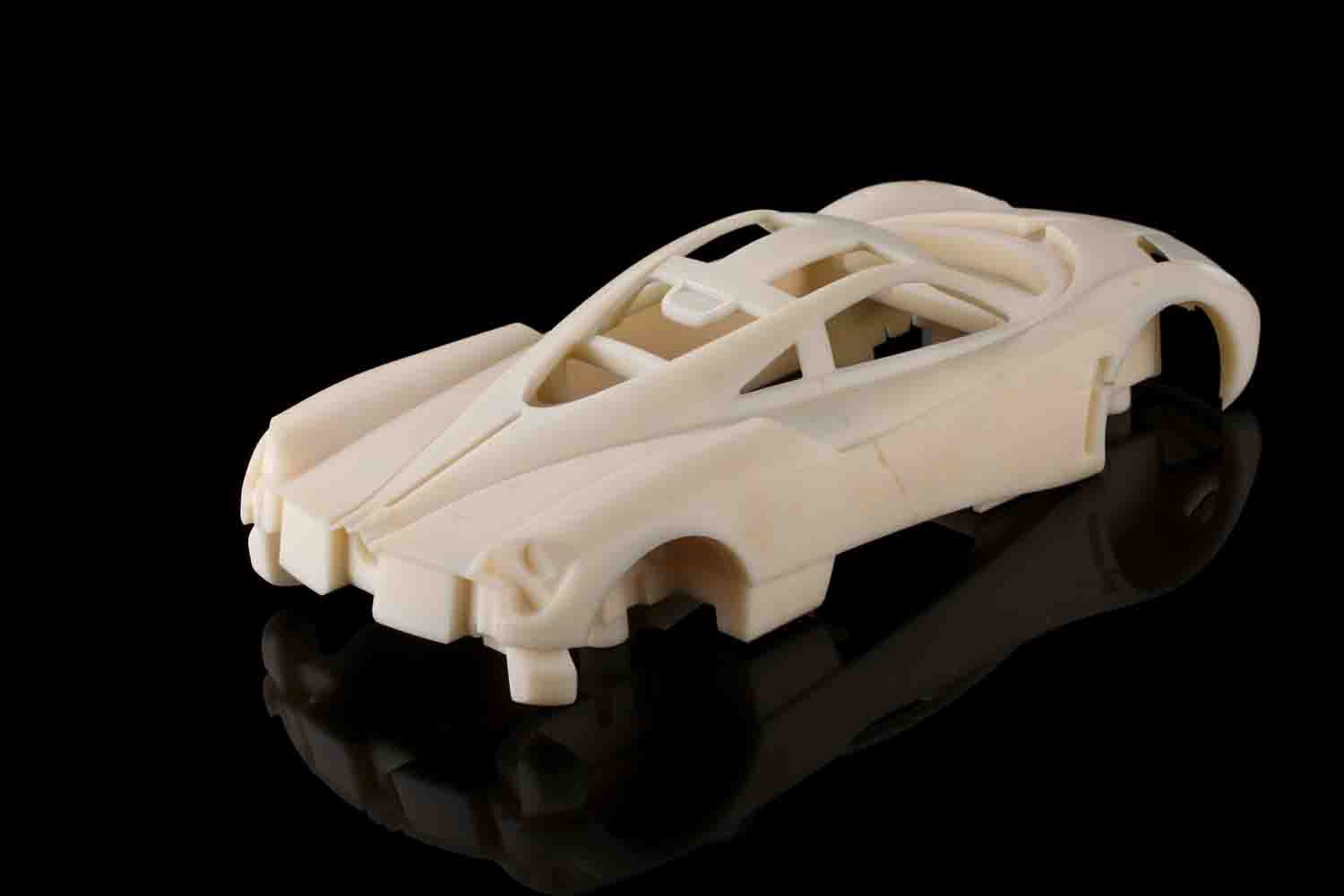
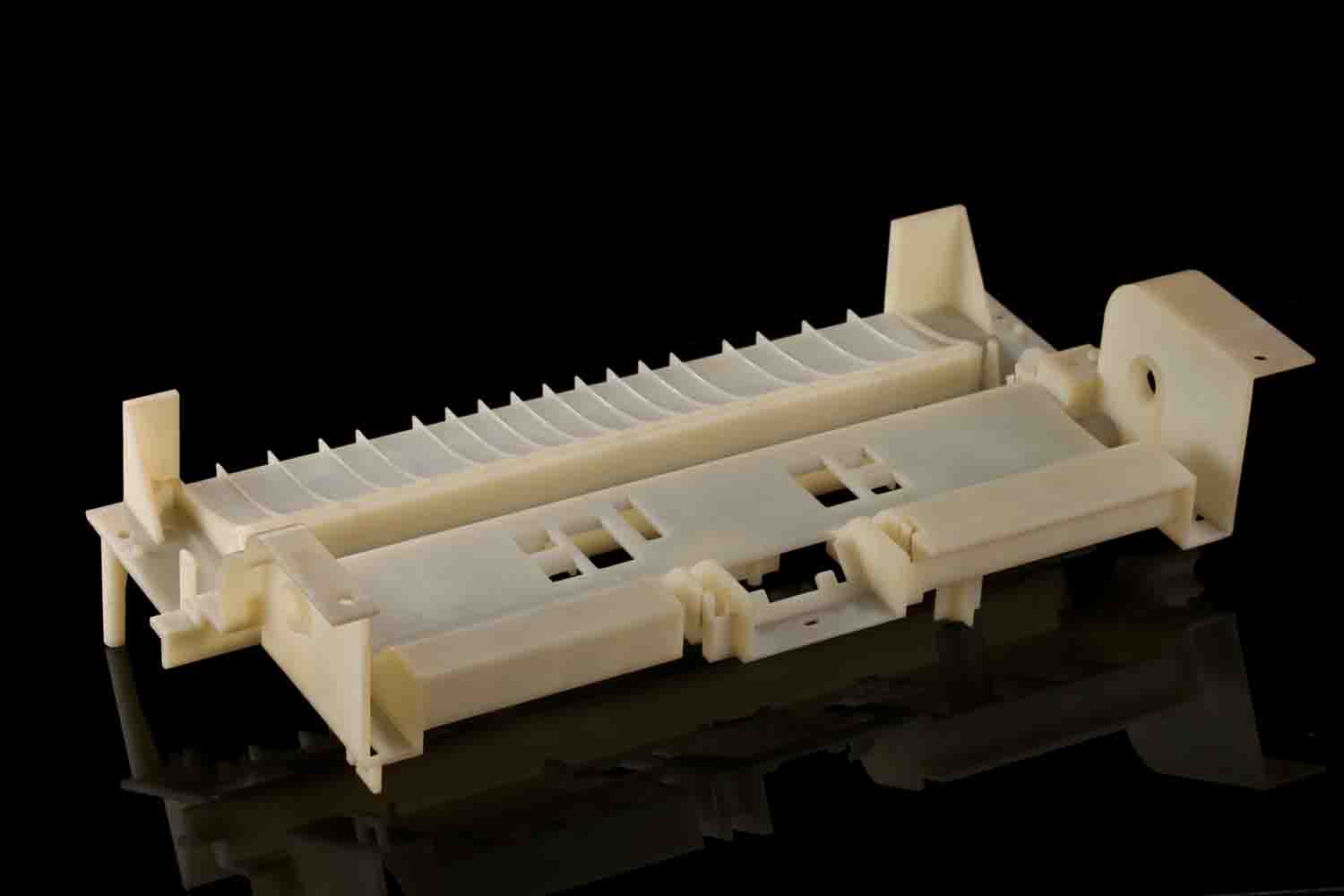
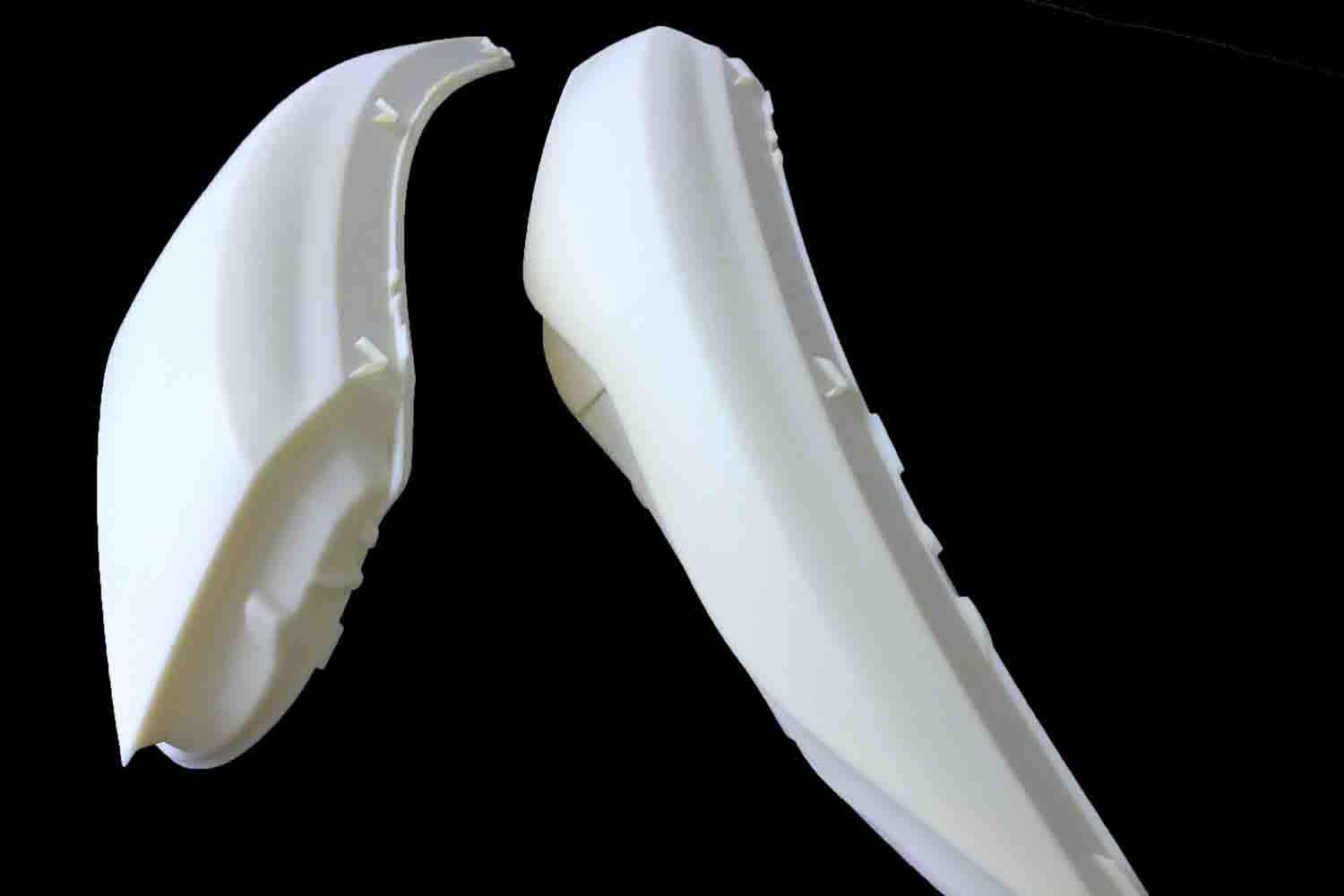
Special Tips for Manual Surface Finish
Preparation: Properly clean and prepare the surface of the prototype before applying any surface finish treatment.
Consistency: Maintain consistency in the application of surface finish treatments to ensure uniform results.
Testing: Conduct test runs on sample pieces to determine the best surface finish treatment for the desired outcome.
Safety: Wear appropriate protective gear, such as gloves and goggles, when working with chemicals or abrasive materials.
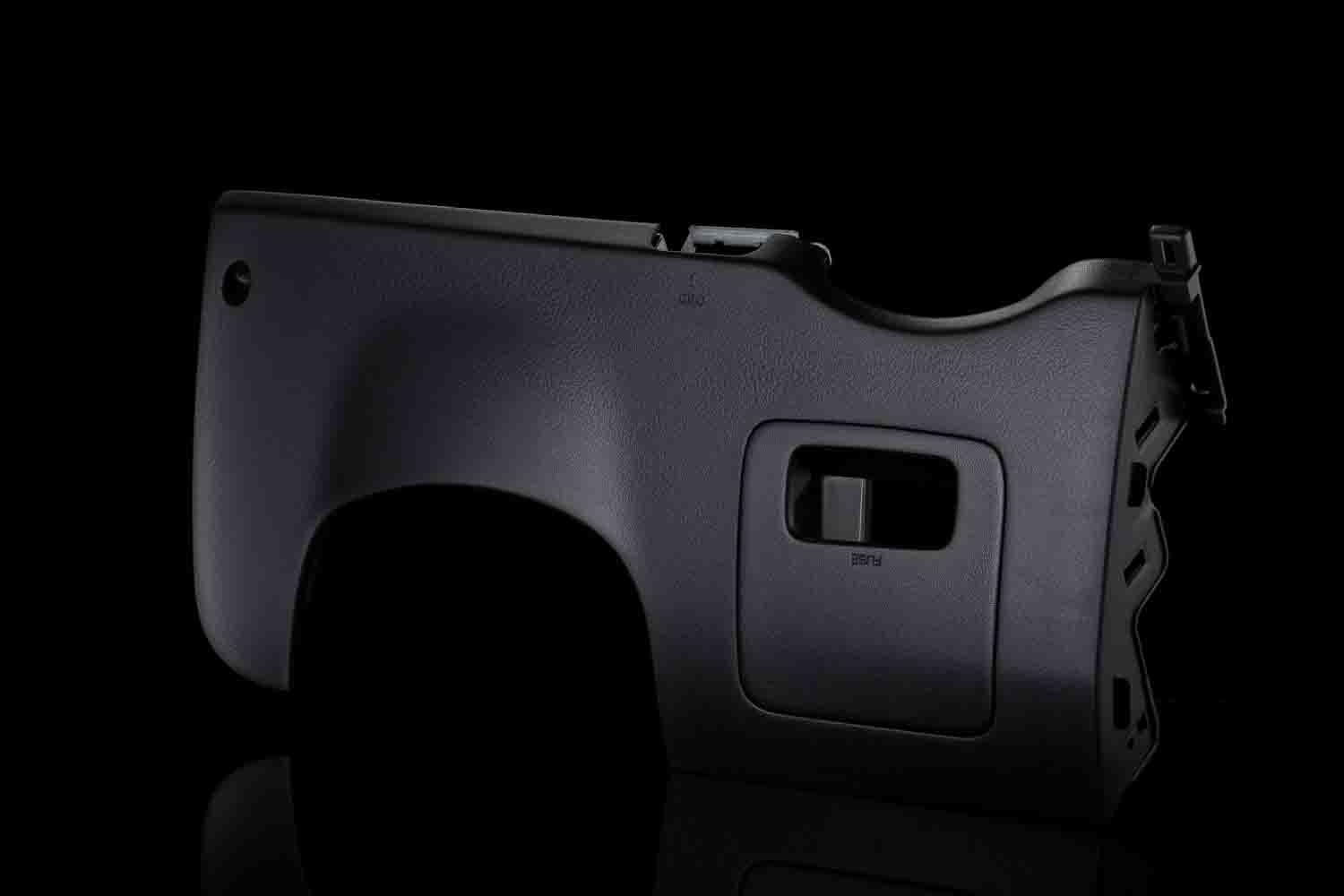
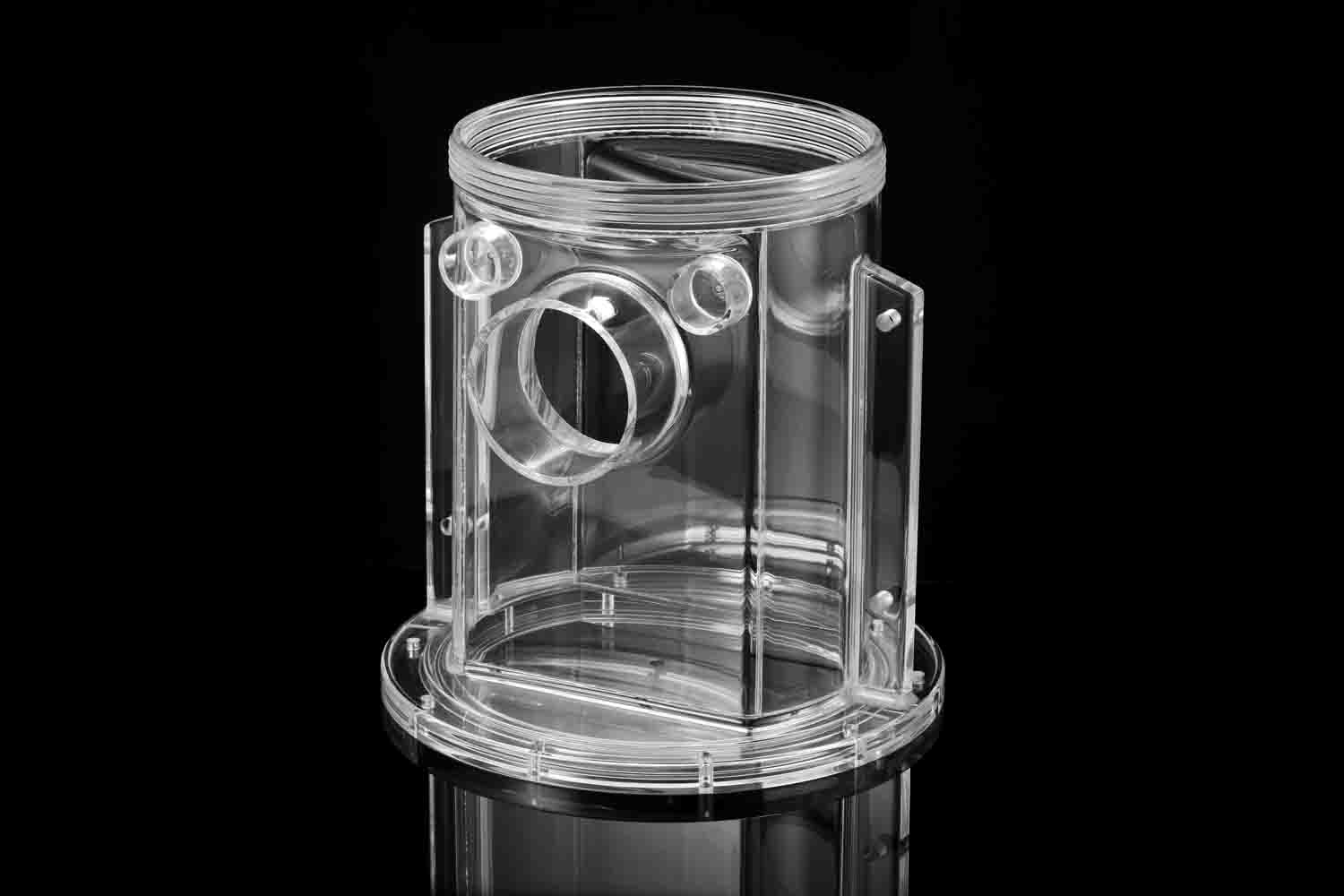
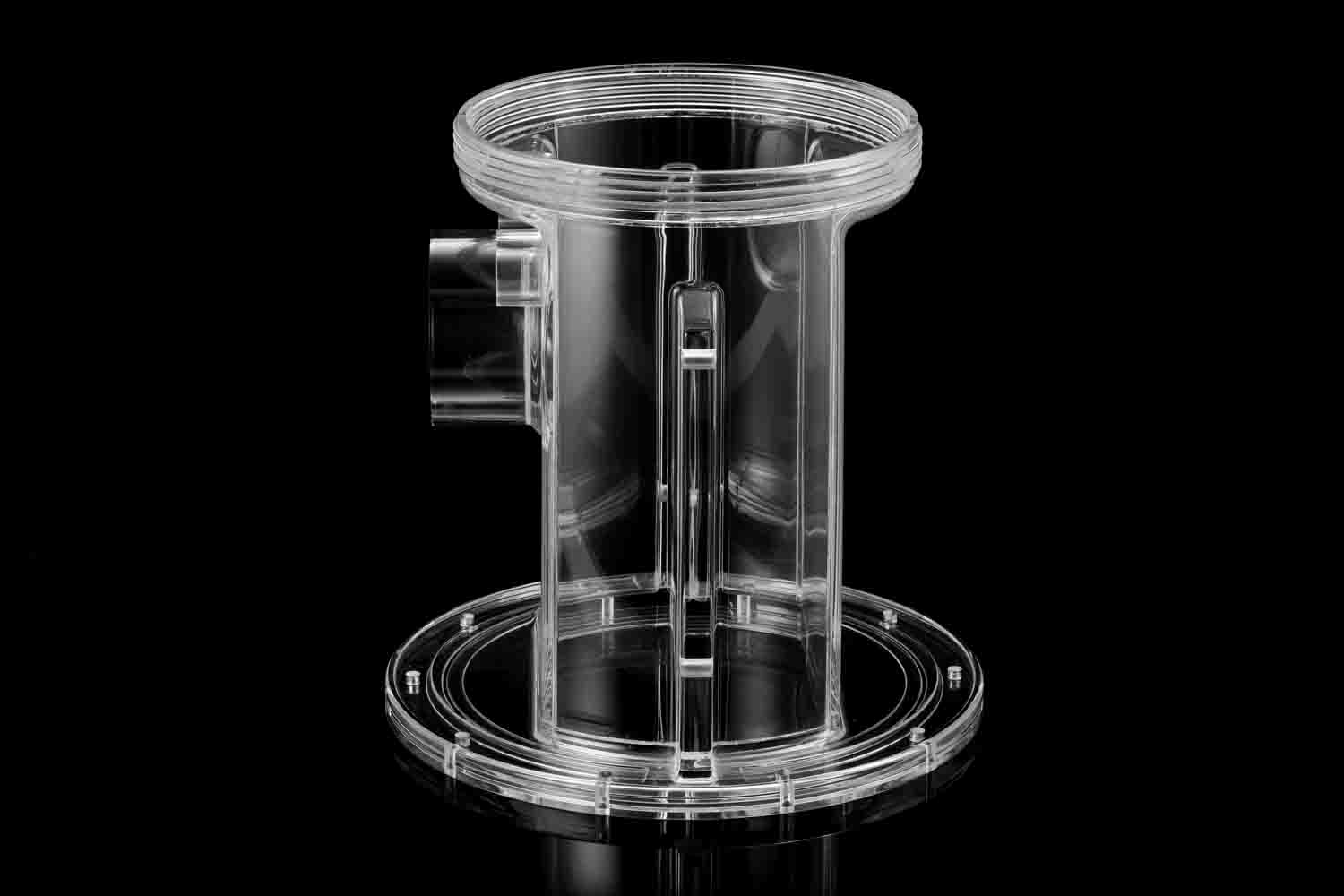
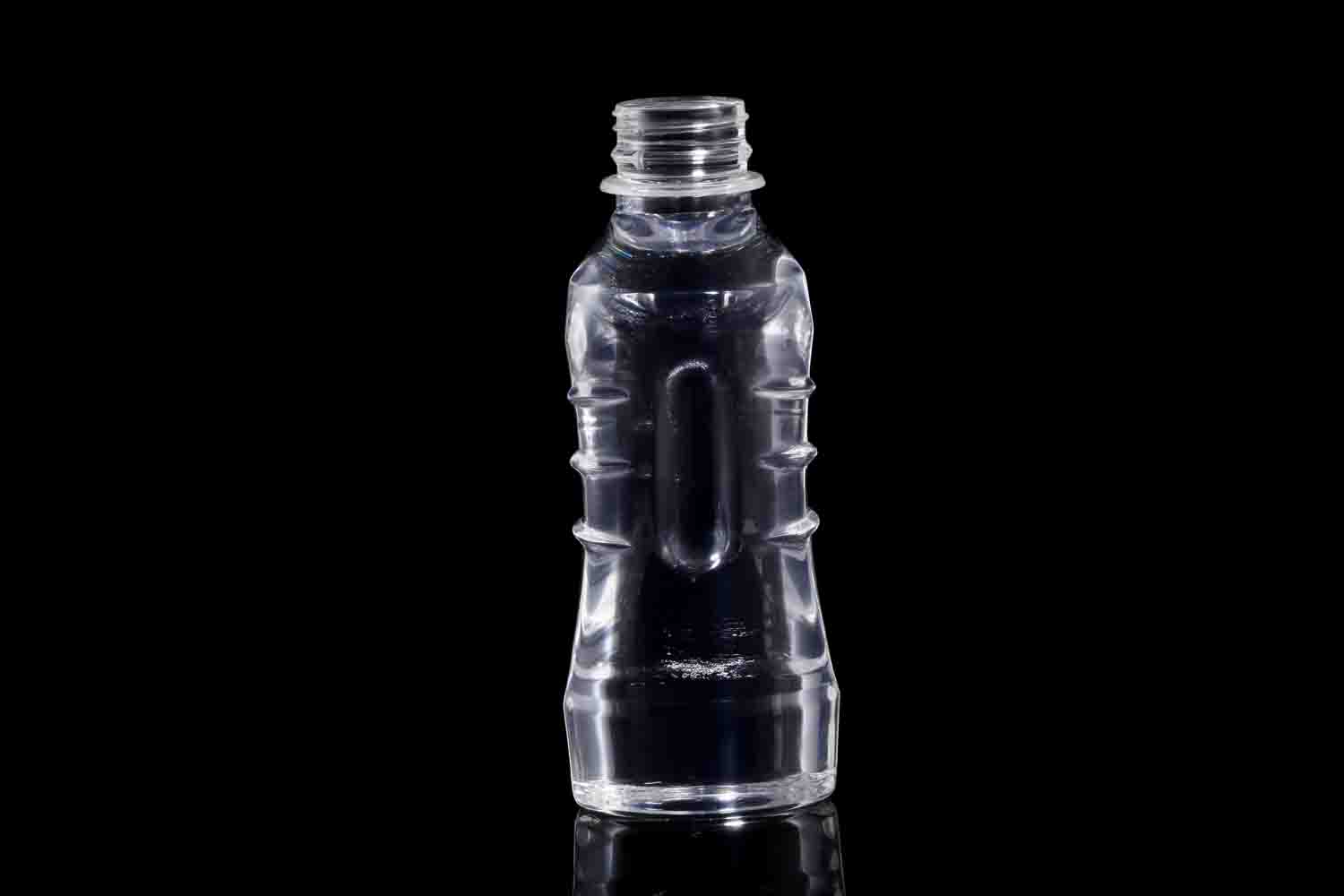
Advanced Techniques in Rapid Prototyping
As rapid prototyping continues to evolve, several advanced techniques have emerged to enhance the speed, precision, and quality of prototyping processes. Some of these techniques include:
Additive Manufacturing: Additive manufacturing, also known as 3D printing, allows for the creation of complex geometries and intricate designs with high accuracy and efficiency.
Multi-Material Printing: Multi-material printing enables the fabrication of prototypes with varying material properties in a single print, expanding the possibilities for functional prototypes.
Surface Texture Mapping: Surface texture mapping techniques enhance the visual appeal of prototypes by replicating textures and finishes found in real-world objects.
Generative Design: Generative design software utilizes algorithms to optimize designs based on specified parameters, leading to innovative and efficient prototypes.
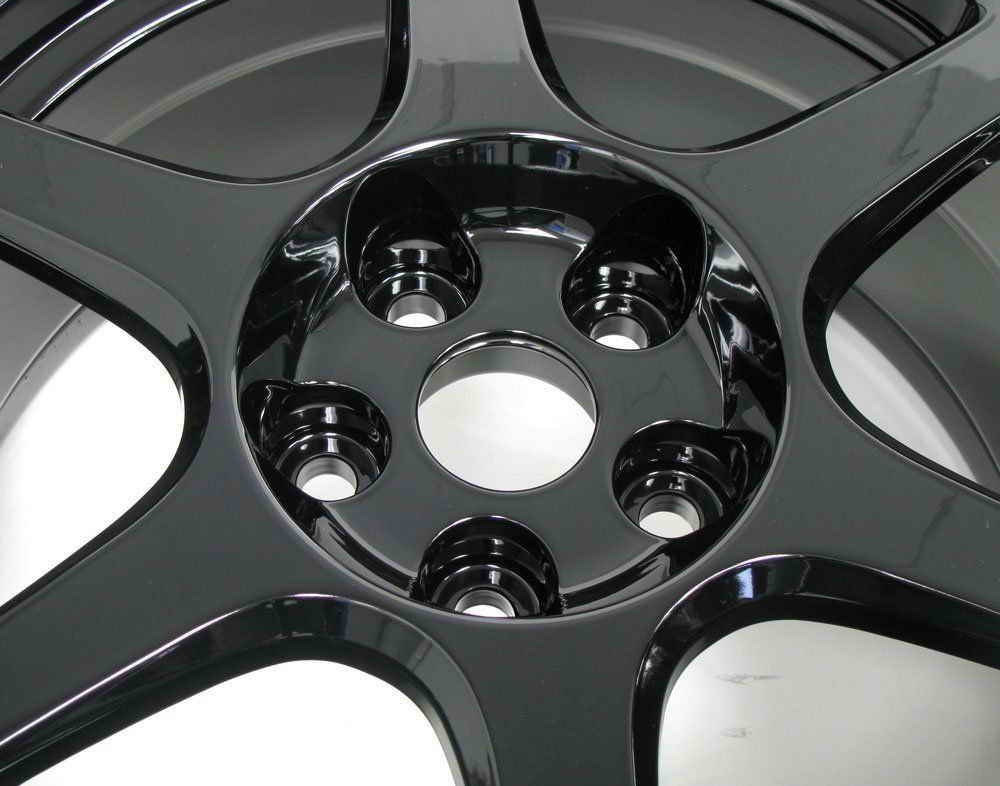
Leveraging Digital Technologies for Surface Finish
Digital technologies such as computer-aided design (CAD) software and simulation tools play a crucial role in achieving precise surface finishes in rapid prototyping. These tools enable designers and engineers to visualize, simulate, and refine surface finish treatments before implementation, reducing errors and enhancing efficiency.
Conclusion:
In conclusion, manual surface finish for rapid prototyping plays a crucial role in enhancing the quality, aesthetics, and precision of prototypes.
By understanding the various surface finish treatments, using the right tools, following special tips, and leveraging the expertise of skilled individuals, manufacturers can create prototypes that meet the highest standards of excellence and pave the way for successful bulk manufacturing endeavors.
Advanced techniques in rapid prototyping, coupled with digital technologies, continue to push the boundaries of innovation and efficiency in the manufacturing industry, ensuring that prototypes are not just functional but also visually appealing and market-ready.