5-axis milling car parts is very important for auto manufacturing. The automotive industry constantly seeks ways to enhance efficiency and precision in manufacturing processes. One technology that has significantly transformed the production of auto parts is 5-axis milling. This advanced machining technique allows for the creation of complex and high-precision components, essential for modern vehicles. In this article, we will delve into how 5-axis milling machines process auto parts and why they are pivotal in increasing manufacturing efficiency.
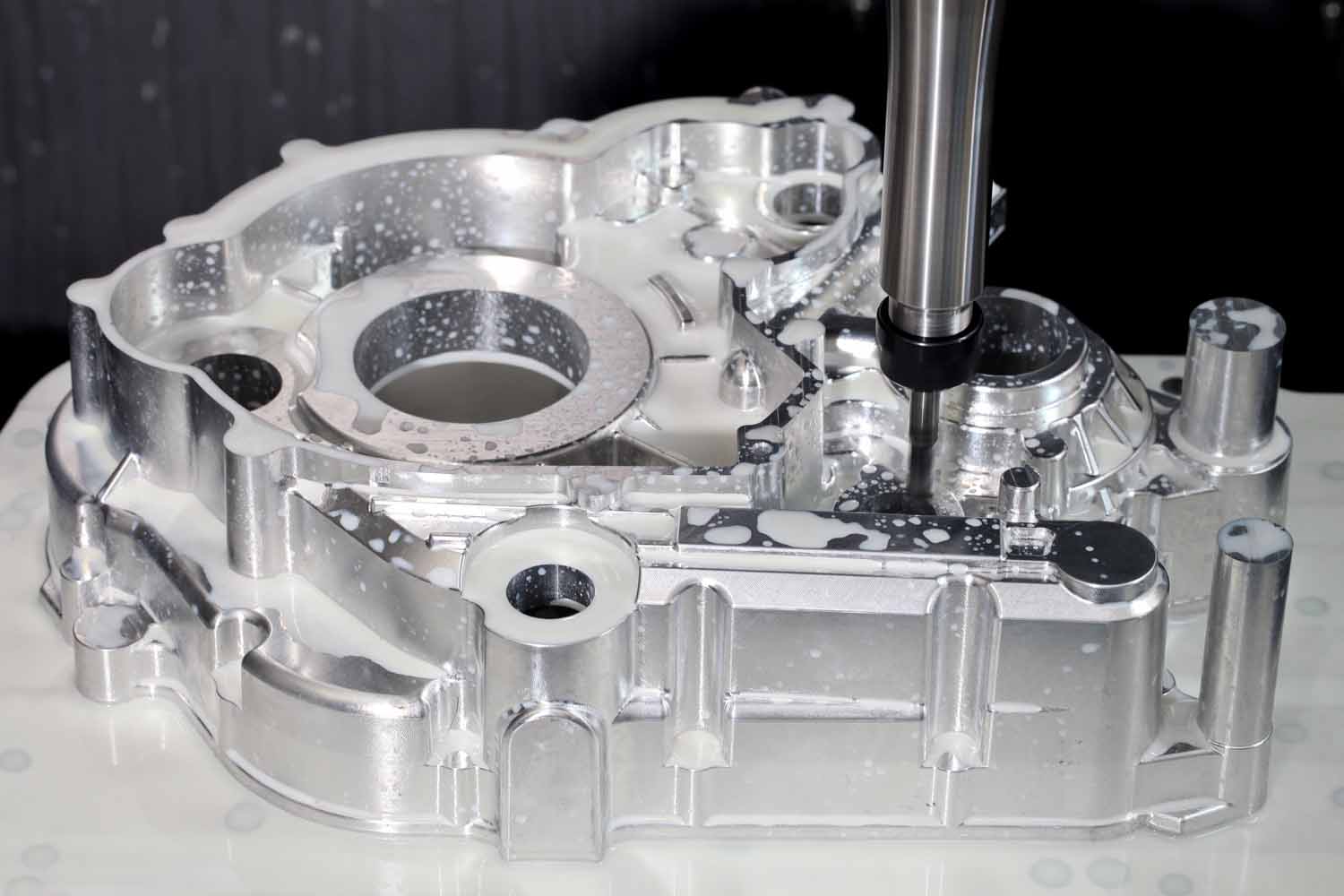
Understanding 5-Axis Milling Machines
5-axis milling machines are advanced CNC (Computer Numerical Control) machines that operate along five different axes simultaneously. Unlike traditional 3-axis milling machines, which move the cutting tool along the X, Y, and Z axes, 5-axis milling machines add two additional rotational axes (A and B). This capability allows for the machining of intricate and complex geometries that are often required in the automotive industry.
How 5-Axis Milling Machines Process Car Parts
1. Complex Geometries and Precision
5-axis milling machines are designed to handle the most complex geometries found in car parts. Components such as engine blocks, transmission cases, and suspension parts often require intricate shapes and tight tolerances. The additional rotational axes of 5-axis machines enable the cutting tool to approach the workpiece from virtually any direction, ensuring precise and accurate machining.
2. Reduced Setups and Increased Efficiency
Traditional 3-axis milling often requires multiple setups and manual repositioning of the workpiece to achieve the desired shape. This process is time-consuming and can lead to errors. In contrast, 5-axis milling machines can machine multiple sides of a car part in a single setup. This reduces the need for manual intervention, minimizes setup times, and significantly increases overall efficiency.
3. Enhanced Surface Finish
The ability to maintain a constant angle relative to the workpiece during machining results in a superior surface finish. This is particularly important for car parts that require smooth surfaces for optimal performance and aesthetics. 5-axis milling ensures that the final product meets the highest quality standards, reducing the need for additional finishing operations.
4. Versatility in Material Handling
Car parts are made from a variety of materials, including aluminum, steel, titanium, and composites. 5-axis milling machines are versatile and capable of handling a wide range of materials with ease. This versatility allows manufacturers to produce diverse components, from lightweight aluminum engine parts to durable steel suspension components, all with the same level of precision.
5. Increased Tool Life
The advanced capabilities of 5-axis milling machines allow for better tool orientation and engagement with the workpiece. This results in reduced tool wear and longer tool life. For manufacturers, this translates to lower tool replacement costs and less downtime, further enhancing production efficiency.
Why 5-Axis Milling Increases Manufacturing Efficiency for Car Parts
1. Time Savings
One of the most significant advantages of 5-axis milling car parts is the substantial time savings it offers. The ability to machine complex parts in a single setup reduces production time and accelerates the manufacturing process. This is crucial in the automotive industry, where time-to-market is a critical factor.
2. Cost-Effectiveness
While 5-axis milling machines represent a higher initial investment compared to traditional 3-axis machines, the long-term cost savings are substantial. The reduction in setup times, increased tool life, and minimized material waste contribute to lower overall production costs. This cost-effectiveness makes 5-axis milling an attractive option for automotive manufacturers.
3. Improved Quality and Consistency
The precision and accuracy of 5-axis milling ensure that car parts are manufactured to exact specifications. This consistency in quality is essential for automotive components that must meet stringent safety and performance standards. By maintaining high-quality standards, manufacturers can reduce the risk of defects and recalls, further enhancing efficiency.
4. Flexibility in Design
The automotive industry is constantly evolving, with new designs and innovations emerging regularly. 5-axis milling machines offer the flexibility to adapt to these changes quickly. Manufacturers can produce prototypes and custom components with ease, allowing for rapid iteration and innovation. This flexibility is a key driver of efficiency in the fast-paced automotive sector.
5. Integration with Advanced Technologies
5-axis milling machines can be seamlessly integrated with other advanced technologies, such as CAD/CAM software and automation systems. This integration streamlines the entire manufacturing process, from design to production, and enables real-time monitoring and optimization. The result is a highly efficient and responsive manufacturing environment.
Conclusion
5-axis milling car parts have revolutionized the automotive manufacturing process, offering unparalleled precision, efficiency, and versatility. By enabling the production of complex geometries, reducing setup times, and enhancing surface finishes, 5-axis milling machines have become indispensable in the automotive industry. The time and cost savings, improved quality, and flexibility in design make 5-axis milling an essential technology for modern car part manufacturing. As the automotive industry continues to evolve, the adoption of 5-axis milling will play a crucial role in driving innovation and maintaining competitive advantage.