To better serve our clients, Bole put heavy investment to purchase plentiful Vertical Machining Center(VMC) and Horizontal Machining Center(HMC) and train our engineers. Both of them are important CNC processing machines. In this article, we will make a comparison and technical illustration. We hope more and more news clients know our capability and our sincerity for potential cooperation.
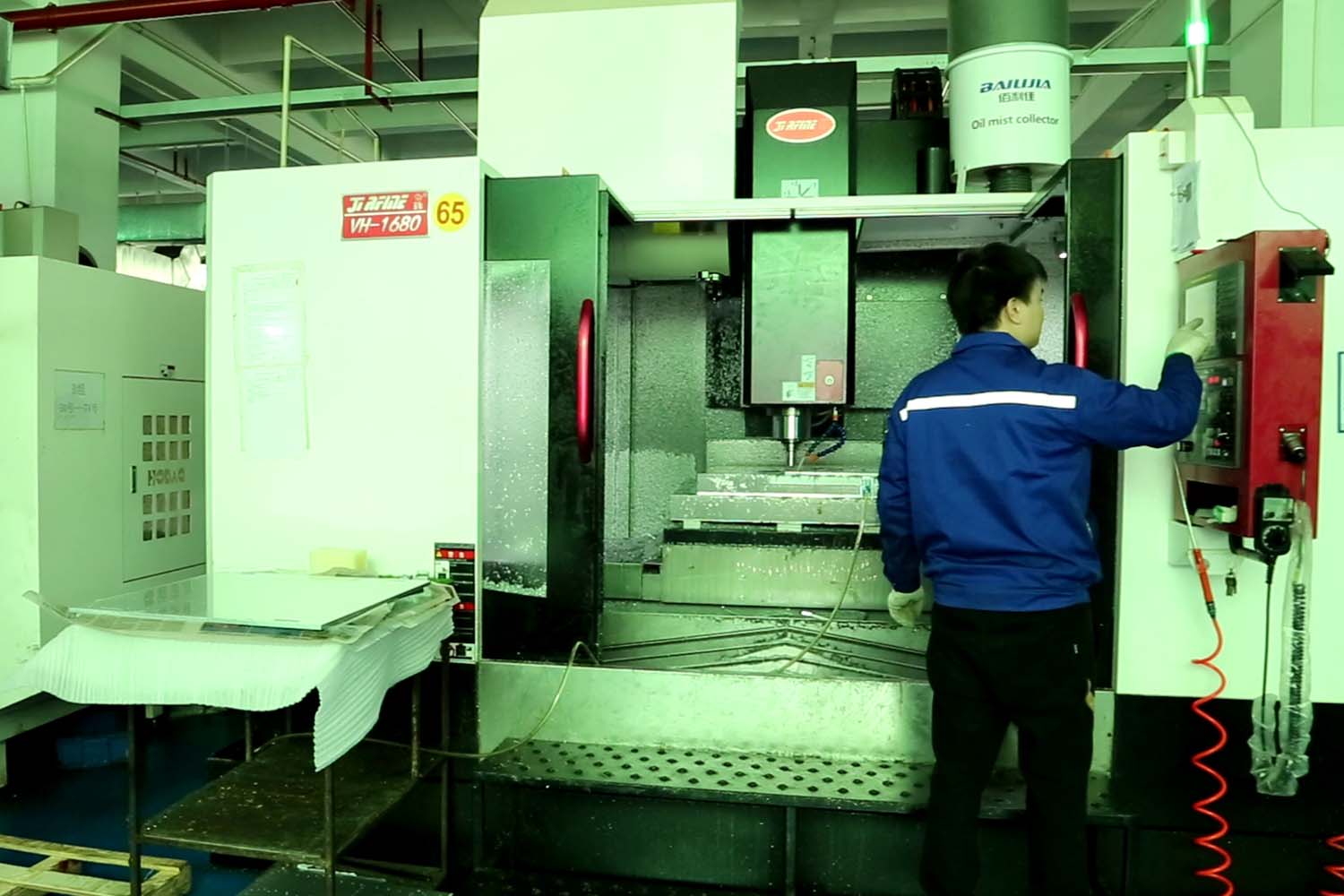
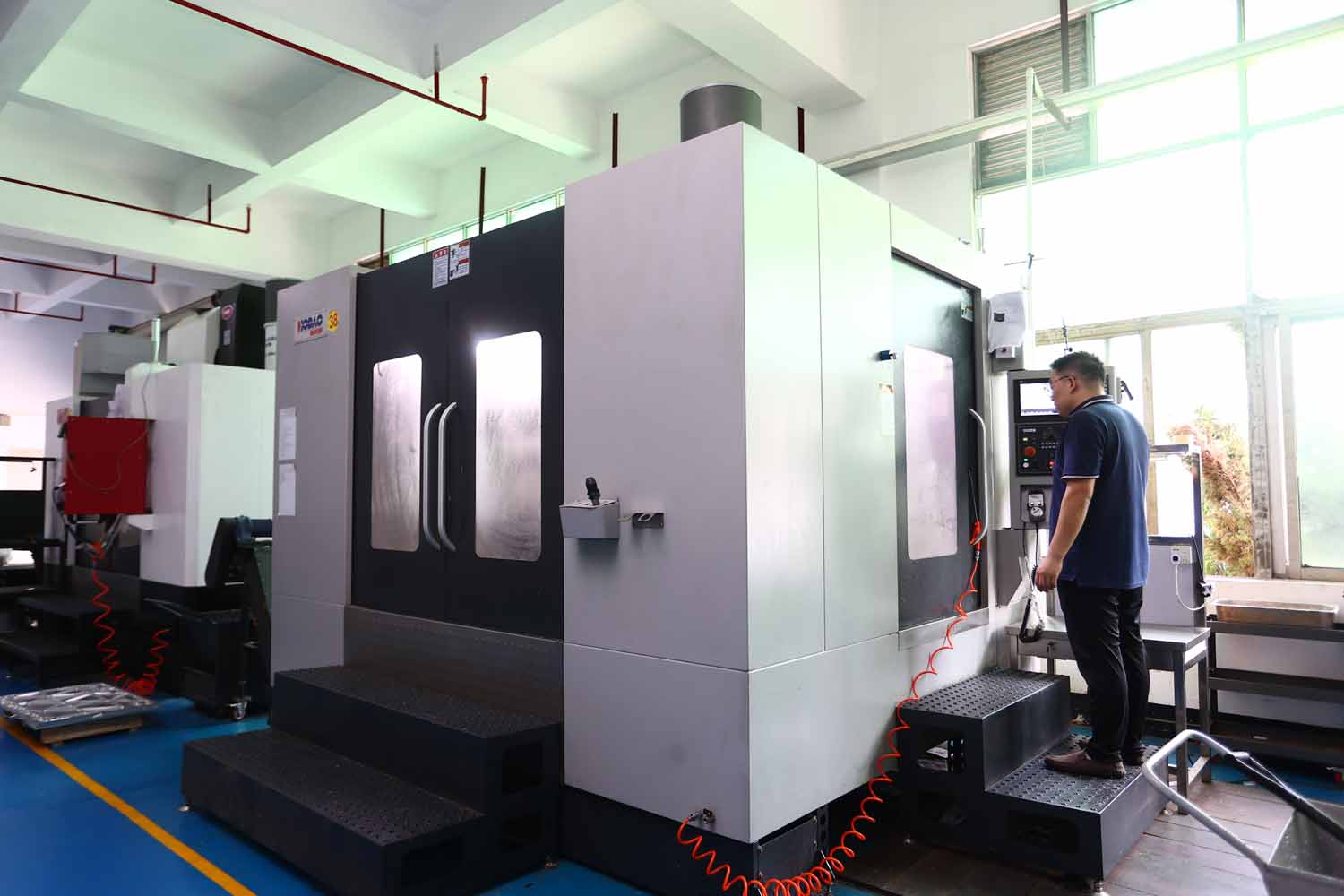
Explore Bole’s precision CNC machining shop
What is a Vertical Machining Center (VMC)?
VMC is a type of CNC machine where the spindle is oriented vertically (perpendicular to the worktable). It’s one of the most common types of machining centers used in manufacturing due to its versatility and cost-effectiveness.
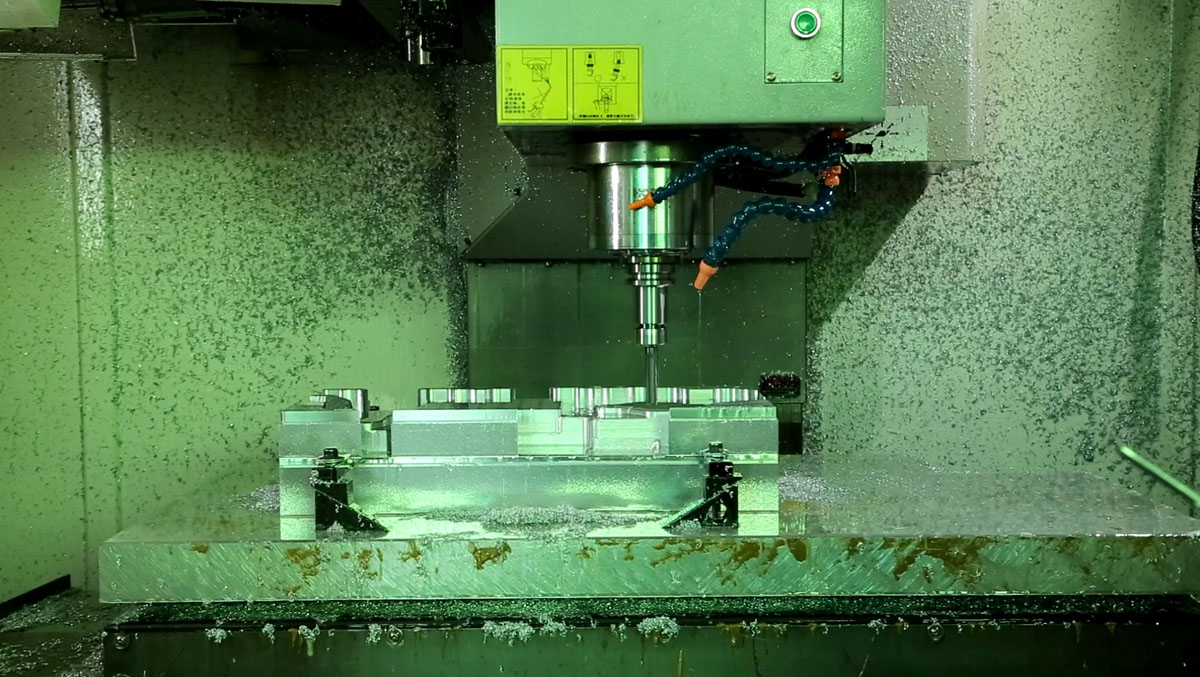
Key Features
Vertical Spindle Orientation
The spindle is aligned vertically, which makes it ideal for machining flat surfaces, pockets, and cavities.
Workpiece Positioning
The workpiece is mounted on a horizontal worktable, and the cutting tool moves along the X, Y, and Z axes to perform operations.
Ease of Use
VMCs are generally easier to set up and operate, making them suitable for smaller production runs or prototypes.
Applications
Commonly used for milling, drilling, tapping, and contouring operations. Industries: Automotive, aerospace, mold-making, and general manufacturing.
Cost-Effectiveness
VMCs are typically more affordable than horizontal machining centers, both in terms of initial cost and maintenance.
Advantages of Vertical Machining Center
Better Visibility. Operators can easily see the machining process due to the vertical orientation of the spindle.
Smaller Footprint. VMCs usually take up less floor space compared to HMCs.
Simpler Workholding. Gravity helps keep the workpiece in place, reducing the complexity of fixtures.
Versatility. Suitable for a wide range of machining tasks, especially for parts with complex geometries.
What is a Horizontal Machining Center (HMC)?
HMC is another type of CNC machine where the spindle is oriented horizontally (parallel to the worktable). This design is better suited for certain types of machining tasks, particularly those involving heavy material removal or complex multi-sided parts.
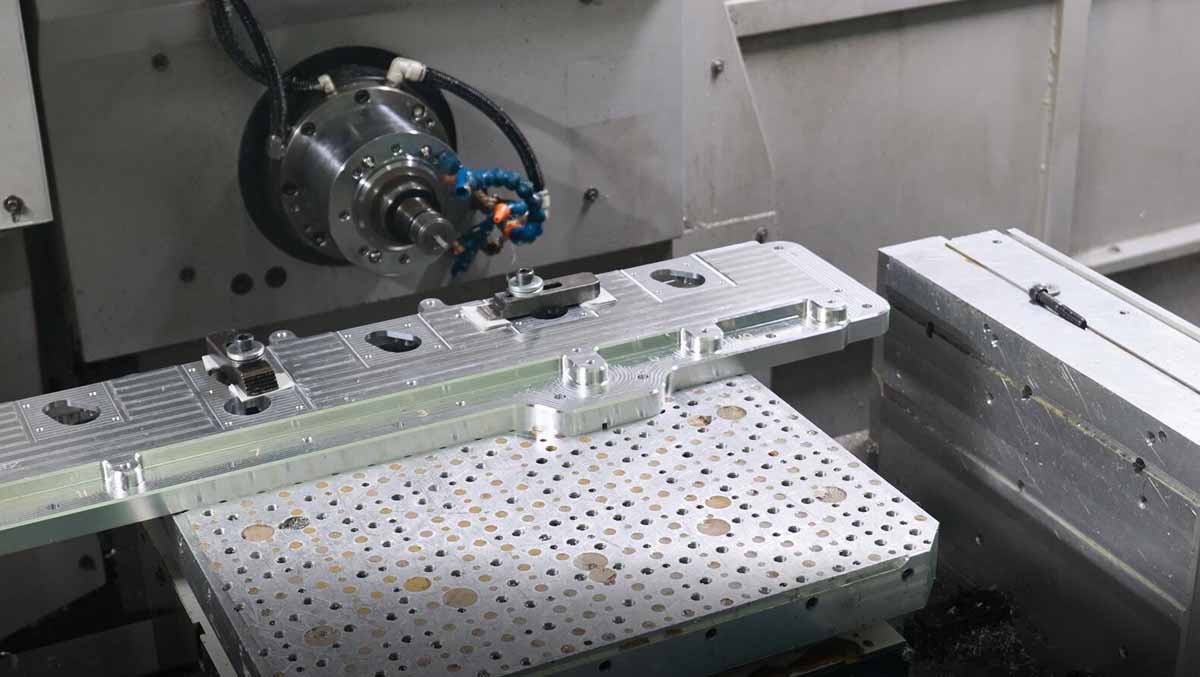
Horizontal Spindle Orientation
The spindle is horizontal, allowing for machining on multiple sides of a workpiece without repositioning.
Rotary Table or Pallet System
HMCs often include a rotary table or a pallet changer, enabling efficient multi-sided machining.
Chip Evacuation
Chips naturally fall away from the cutting area due to gravity, improving machining efficiency and reducing tool wear.
Applications
deal for high-volume production, heavy-duty cutting, and machining large or complex parts. Industries: Automotive, aerospace, heavy equipment, and energy.
Advantages
Faster Cycle Times: Multi-sided machining without manual repositioning reduces setup time.
Better Chip Management: Chips are less likely to accumulate around the cutting area, improving surface finish and tool life.
High Productivity: HMCs are often equipped with pallet changers, allowing one part to be machined while another is being set up.
Alright, let’s make a form to show their comparison
Feature | Vertical Machining Center (VMC) | Horizontal Machining Center (HMC) |
---|---|---|
Spindle Orientation | Vertical (perpendicular to the worktable) | Horizontal (parallel to the worktable) |
Workpiece Setup | Simple, gravity helps hold the workpiece | Requires more complex fixtures |
Chip Evacuation | Chips tend to accumulate on the workpiece | Chips fall away naturally due to gravity |
Visibility | Easy to monitor the machining process | Limited visibility due to horizontal setup |
Applications | Prototyping, smaller production runs | High-volume production, multi-sided machining |
Cost | Lower initial cost and maintenance | Higher initial cost, but more productive |
Footprint | Compact, requires less floor space | Larger, requires more floor space |
Productivity | Slower for multi-sided parts (requires repositioning) | Faster for multi-sided machining (rotary tables) |
How to Choose Between a VMC and HMC?
Bole’s experienced PMC engineers will make proper production arrangement according to the order and design. Generally, we judge to start upon below considerations:
Part Geometry
VMCs are better for flat, simple parts or parts requiring detailed contouring. HMCs excel at machining parts with features on multiple sides or complex geometries.
Production Volume
VMCs are ideal for low to medium production volumes or prototypes. HMCs are better suited for high-volume production due to reduced setup times.
Budget
VMCs are more cost-effective for smaller shops or businesses. HMCs require a larger upfront investment but can be more cost-efficient for large-scale production.
Material Removal
HMCs are better for heavy-duty cutting and high material removal rates. VMCs are sufficient for lighter machining tasks.
Space and Infrastructure
VMCs are more compact and easier to install in smaller workshops. HMCs require more space and often need additional infrastructure like pallet changers.
Both Vertical Machining Center (VMC) and Horizontal Machining Center (HMC) have their strengths and are suited for different applications. VMCs are versatile, cost-effective, and easy to use, making them a popular choice for general-purpose machining. On the other hand, HMCs offer higher productivity, better chip management, and are ideal for complex, multi-sided parts or high-volume production.
Choosing the right machine depends on your specific manufacturing needs, budget, and production goals.