È necessario conoscere le 8 tecniche di lavorazione CNC più comuni per conoscerne le applicazioni, i vantaggi e le caratteristiche principali. In questo articolo esploreremo le tecniche di lavorazione CNC essenziali, tra cui la tornitura, la fresatura, la foratura, la rettifica, l'alesatura, la piallatura, la brocciatura e la lavorazione a scarica elettrica (EDM).
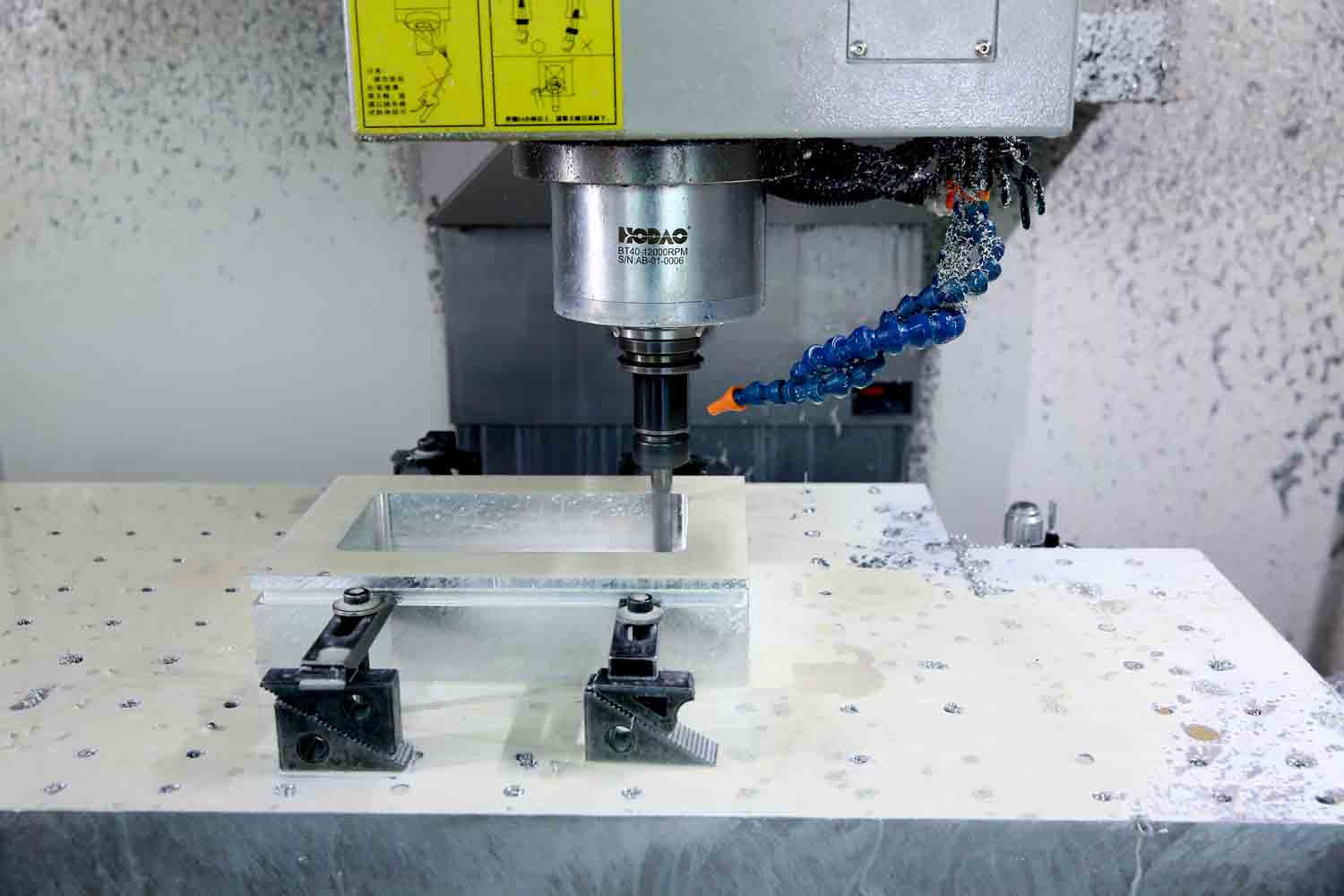
È molto importante indagare sul modo in cui un prodotto viene lavorato se si vuole conoscere la sua struttura dei costi. Imparare le 8 tecniche di lavorazione CNC più comuni vi aiuterà molto.
Quando si parla di industria manifatturiera, i processi di lavorazione meccanica sono una parte essenziale. La lavorazione meccanica è il processo di trasformazione dei materiali grezzi nella forma, nelle dimensioni e nella qualità superficiale desiderate, e comprende una varietà di metodi di lavorazione di precisione per soddisfare le esigenze dei diversi pezzi. Qui di seguito vengono descritte in dettaglio 8 tecniche comuni di lavorazione meccanica.
Si può anche scegliere di esplorare direttamente Servizio di lavorazione CNC di Bole se siete un maestro in questo campo.
Trasformazione
La tornitura prevede il fissaggio del pezzo su un dispositivo rotante di supporto del pezzo e il taglio graduale del materiale sul pezzo con un utensile da taglio per ottenere la forma e le dimensioni desiderate. Questo metodo è adatto alla produzione di pezzi cilindrici come alberi e manicotti. Il metodo di tornitura e la selezione degli utensili influenzano la forma e la rugosità superficiale del prodotto finale.
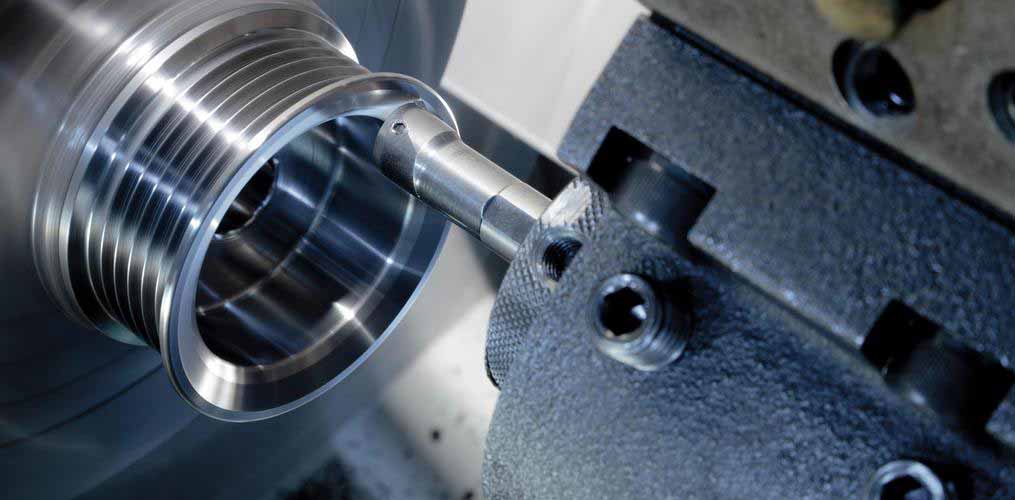
La tornitura può essere suddivisa in diversi tipi: tornitura esterna, tornitura interna, sfacciatura e filettatura.
La tornitura esterna è comunemente utilizzata per la lavorazione di forme come alberi, cilindri e coni; nella tornitura interna, l'utensile entra nel foro interno del pezzo per lavorarne il diametro e la superficie secondo le dimensioni e la precisione richieste; la sfacciatura è tipicamente utilizzata per creare superfici piane, come la base o la faccia finale di un pezzo; la filettatura si ottiene tagliando gradualmente la forma del filetto spostando il tagliente dell'utensile rispetto alla superficie del pezzo, comprese le filettature interne ed esterne.
Fresatura
La fresatura consiste nel far ruotare un utensile da taglio sulla superficie del pezzo per tagliare il materiale, consentendo di produrre pezzi con forme complesse come piani, superfici concave e convesse e ingranaggi controllando il movimento dell'utensile. La fresatura comprende la fresatura piana, la fresatura verticale, la fresatura di estremità, la fresatura di ingranaggi e la fresatura di profili, ciascuna adatta a diverse esigenze di lavorazione.
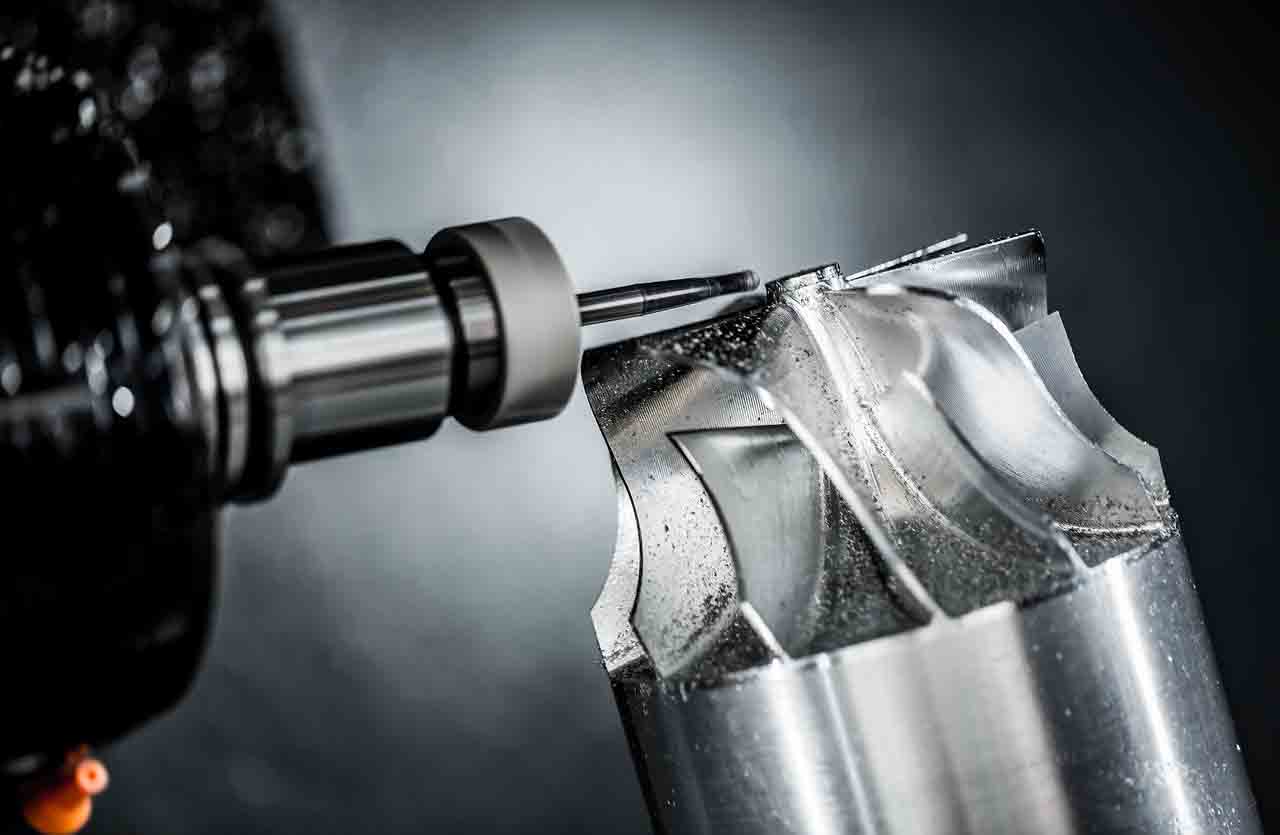
Nella fresatura in piano, il tagliente dell'utensile incide sulla superficie del pezzo per ottenere una superficie piana; la fresatura verticale è utilizzata per la lavorazione di scanalature e fori lungo la direzione dell'altezza del pezzo; la fresatura di testa comporta il taglio sul lato del pezzo ed è utilizzata per la lavorazione di profili, scanalature e bordi; la fresatura di ingranaggi utilizza tipicamente utensili speciali con taglienti per tagliare la forma dei denti dell'ingranaggio; la fresatura di profili è utilizzata per la lavorazione di curve complesse o forme di contorno, con il percorso dell'utensile controllato con precisione in base al contorno.
Perforazione
La foratura consiste nell'incidere il materiale sul pezzo in lavorazione utilizzando una punta rotante per creare fori del diametro e della profondità desiderati, ampiamente utilizzati nei settori della produzione, dell'edilizia e della manutenzione. La foratura è spesso classificata in foratura convenzionale, foratura centrale, foratura profonda, foratura multiasse e altri tipi.
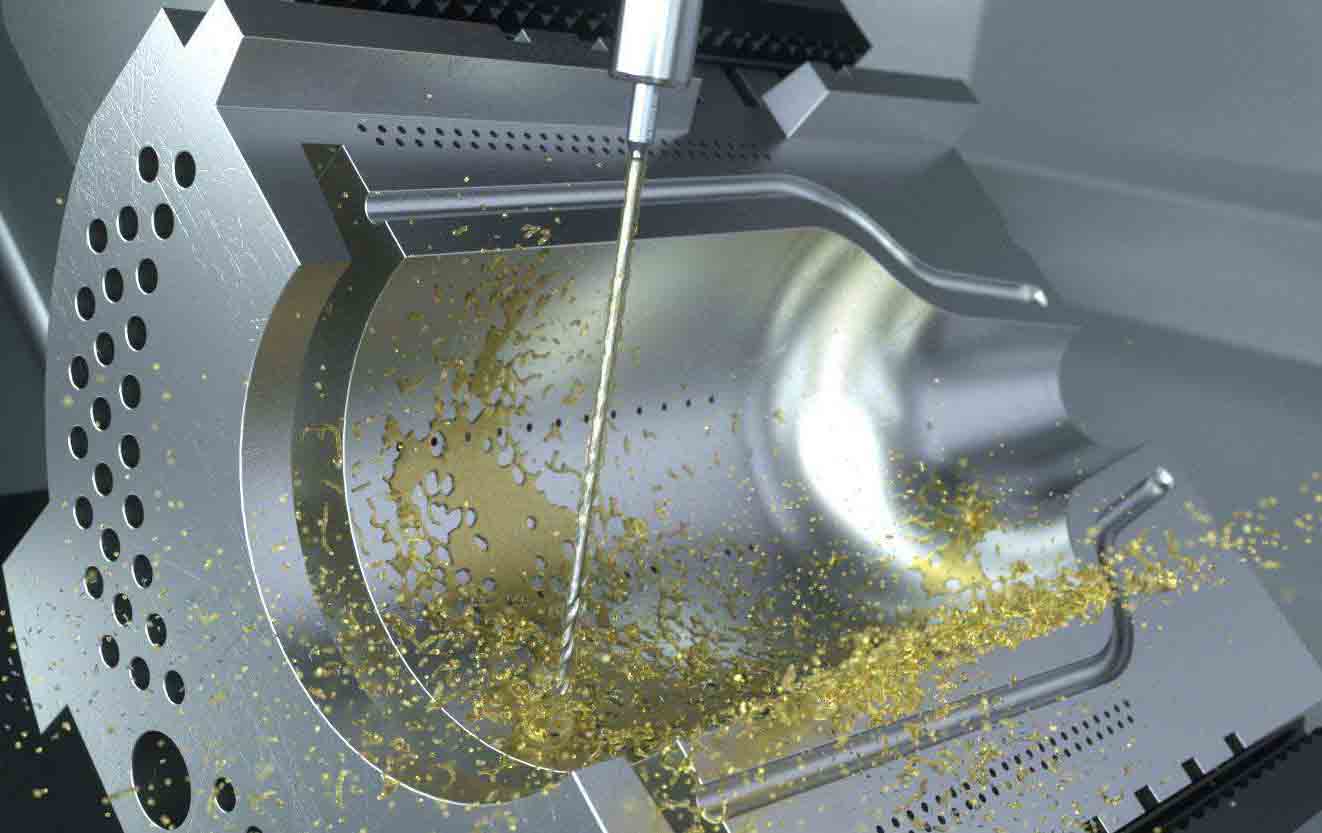
La foratura convenzionale utilizza punte con taglienti a spirale, in genere per fori più piccoli e per esigenze di foratura generiche; la foratura centrale prevede la creazione di un piccolo foro sulla superficie del pezzo prima di utilizzare una punta più grande per garantire il posizionamento accurato di fori più grandi; la foratura profonda è utilizzata per la lavorazione di fori più profondi, che richiedono punte speciali e tecniche di raffreddamento per garantire precisione e qualità; la foratura multiasse utilizza contemporaneamente più punte a diverse angolazioni, adatta ai casi in cui è necessario eseguire più fori contemporaneamente.
La foratura è un metodo di lavorazione molto regolare, una delle tecniche di lavorazione CNC più comuni.
Rettifica
La rettifica consiste nel tagliare o smerigliare gradualmente il materiale sulla superficie del pezzo in lavorazione utilizzando un abrasivo per ottenere la forma, le dimensioni e la qualità superficiale desiderate. La rettifica è comunemente utilizzata per pezzi con requisiti di alta precisione e qualità superficiale, come stampi, parti meccaniche di precisione e utensili.
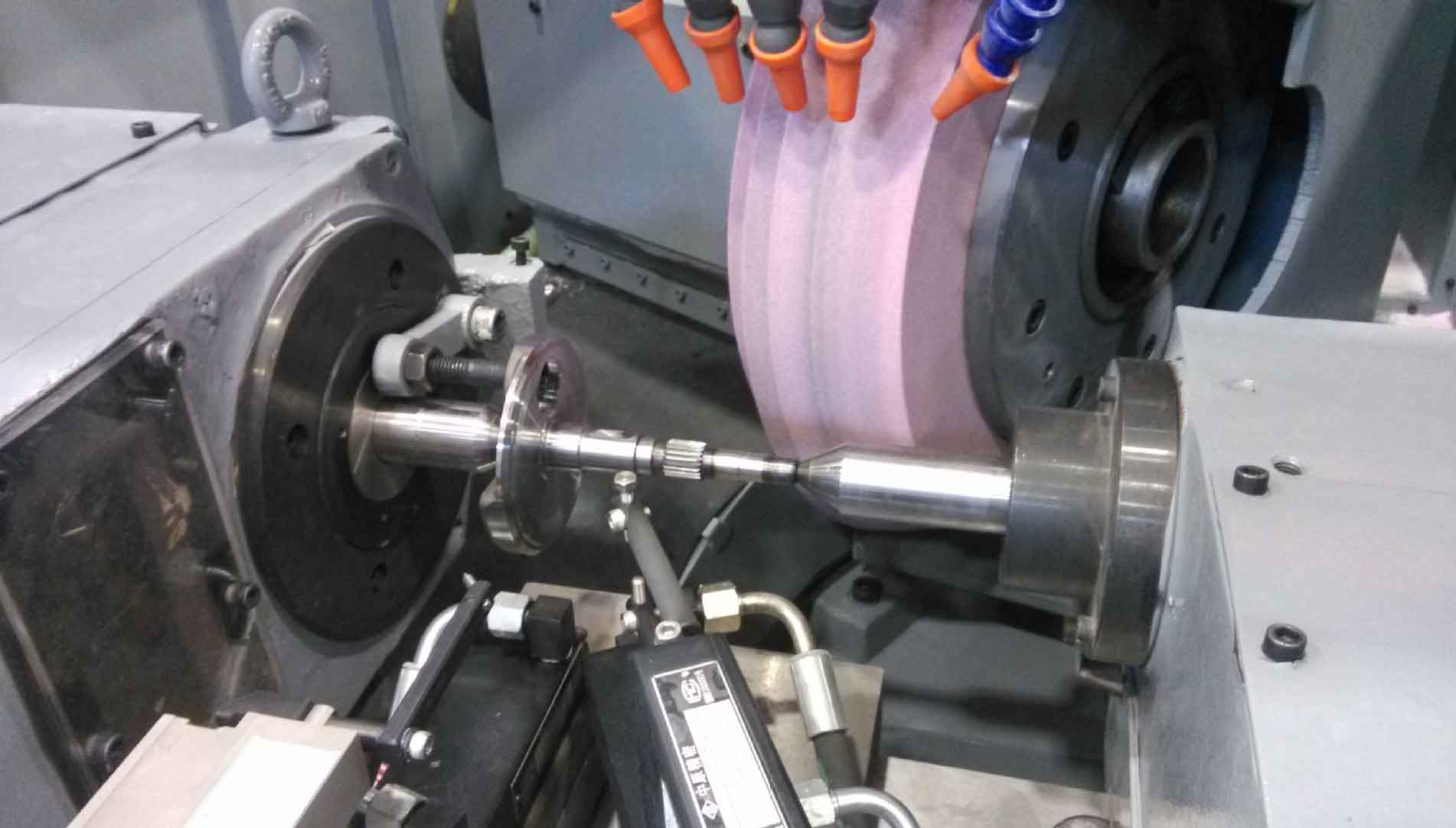
La rettifica si divide in rettifica piana, rettifica esterna, rettifica interna e rettifica di profili. La rettifica piana è utilizzata per la lavorazione delle superfici piane dei pezzi per ottenere superfici lisce e dimensioni precise; la rettifica esterna è utilizzata per la lavorazione della superficie cilindrica esterna dei pezzi, come alberi e perni; la rettifica interna è utilizzata per la lavorazione della superficie interna dei fori, come i fori interni e i fori dell'albero; la rettifica dei profili è utilizzata per la lavorazione di forme complesse, come il bordo di taglio di stampi e utensili.
Noioso
L'alesatura viene utilizzata per la lavorazione di fori circolari interni ai pezzi, incidendo i fori esistenti con un utensile rotante per ottenere dimensioni precise e obiettivi di planarità. A differenza della foratura, in cui i fori si formano tagliando il materiale sulla superficie del pezzo, l'alesatura prevede l'inserimento dell'utensile nel pezzo per praticare i fori.
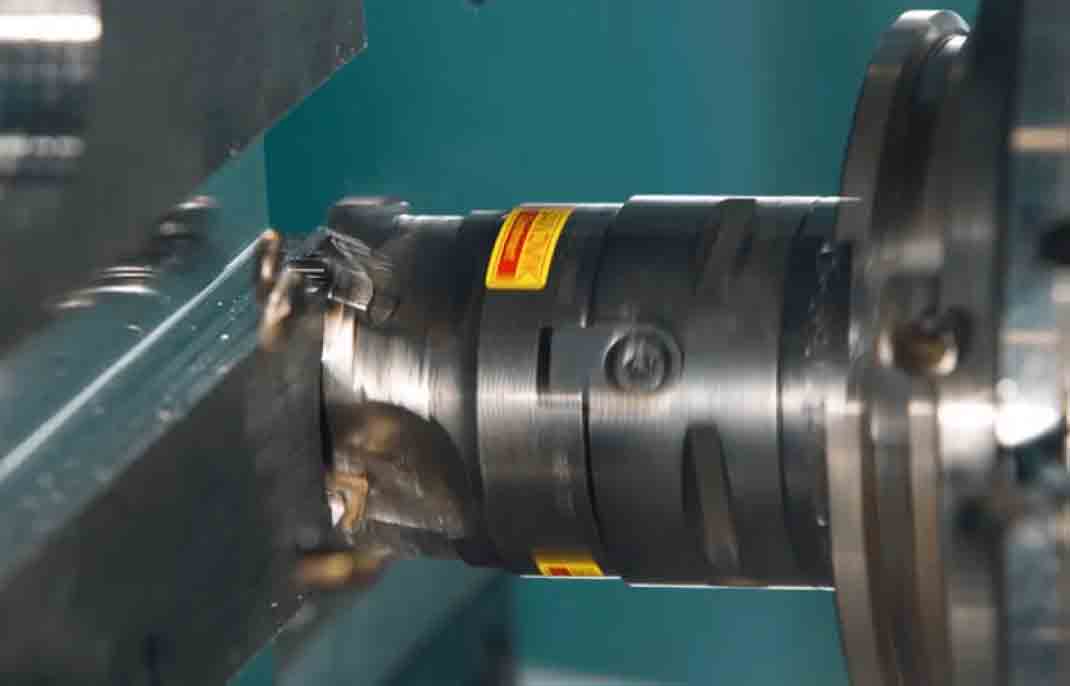
L'alesatura si divide in alesatura manuale e alesatura CNC. L'alesatura manuale è adatta alla produzione di piccoli lotti e a lavorazioni semplici; l'alesatura CNC utilizza la programmazione per determinare i percorsi di taglio, le velocità di avanzamento e le velocità di rotazione per ottenere una lavorazione automatizzata ad alta precisione.
Piallatura
La piallatura consiste nel tagliare il materiale sulla superficie del pezzo con una pialla per ottenere la superficie piana desiderata, dimensioni precise e qualità della superficie. La piallatura è comunemente utilizzata per la lavorazione di superfici piane di pezzi più grandi, come basi e letti. Fornisce una superficie piana ai pezzi da lavorare per adattarli ad altri componenti.
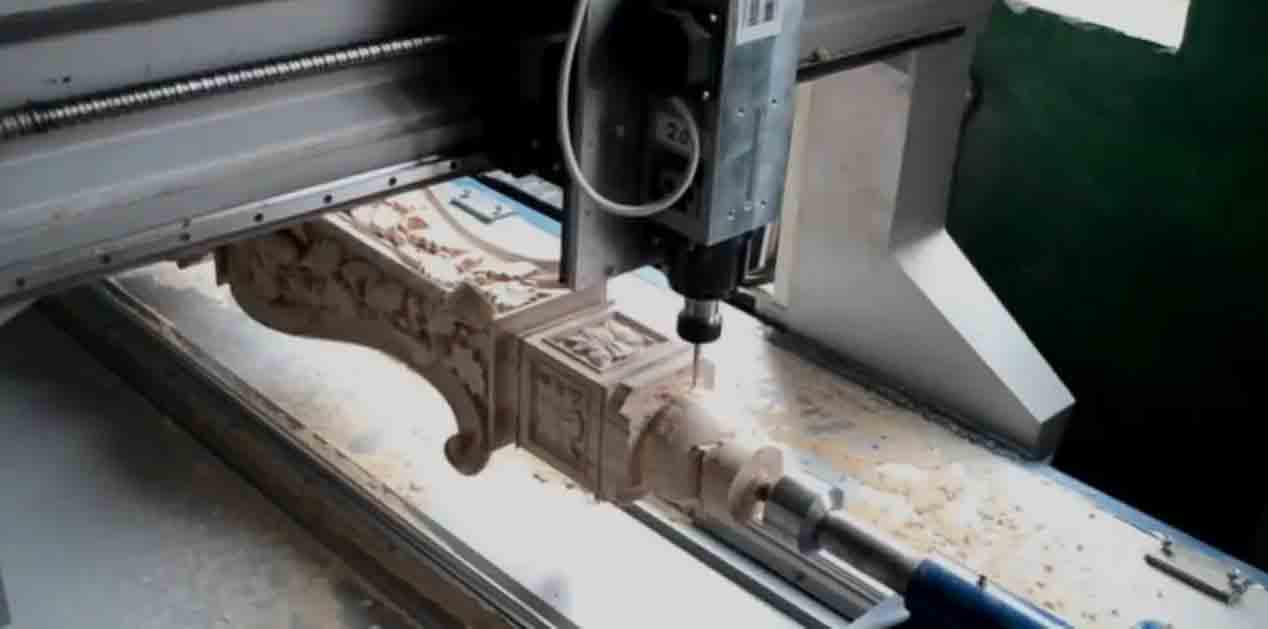
La piallatura si divide tipicamente in una fase di sgrossatura e una di finitura. Nella fase di sgrossatura, la pialla taglia in profondità per rimuovere rapidamente il materiale. Nella fase di finitura, la profondità di taglio viene ridotta per ottenere una maggiore qualità superficiale e precisione dimensionale. La piallatura può essere manuale o automatica. La piallatura manuale è adatta alla produzione di piccoli lotti e a lavorazioni semplici; la piallatura automatica utilizza macchine utensili automatizzate per controllare il movimento della pialla e ottenere un processo di lavorazione più stabile ed efficiente.
Brocciatura
La brocciatura prevede l'approfondimento graduale dei tagli mediante un utensile di brocciatura per creare contorni interni complessi, comunemente utilizzato per la lavorazione di contorni, scanalature e fori di pezzi con forme complesse. La brocciatura consente di ottenere un'elevata precisione di lavorazione e qualità superficiale, adatta a pezzi che richiedono un'alta precisione e una buona qualità superficiale. Viene generalmente classificata in brocciatura piana, brocciatura dei contorni, brocciatura delle scanalature e brocciatura dei fori.
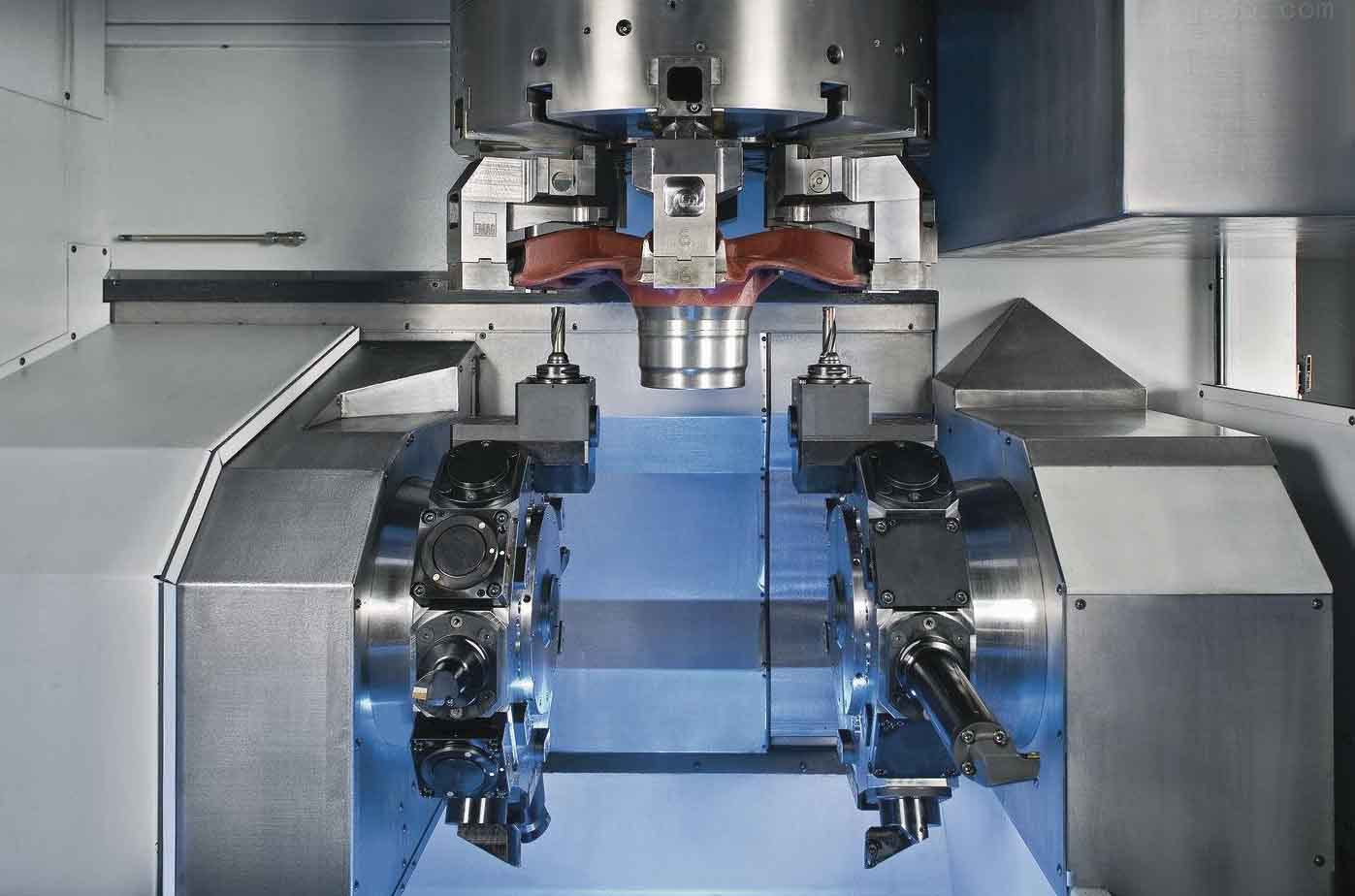
La brocciatura in piano è utilizzata per la lavorazione di superfici piane del pezzo per ottenere superfici lisce e dimensioni precise; la brocciatura per contorni è utilizzata per la lavorazione di forme complesse, come stampi e pezzi; la brocciatura di scanalature è utilizzata per la lavorazione di scanalature e fessure, con il tagliente che entra nel pezzo e taglia lungo la superficie del pezzo; la brocciatura di fori è utilizzata per la lavorazione del contorno interno dei fori, dove il tagliente entra nel foro e taglia la superficie interna del foro.
Lavorazione a scarica elettrica (EDM)
L'elettroerosione utilizza le scariche elettriche per tagliare e lavorare materiali conduttivi, creando parti di alta precisione e di forma complessa, come stampi e utensili. È comunemente utilizzata nella produzione di stampi, stampi a iniezione di plastica, parti di motori aerospaziali, apparecchiature mediche e altri settori. L'elettroerosione è adatta al taglio di materiali duri, fragili o ad alta durezza, difficili da tagliare con i metodi di lavorazione tradizionali, come l'acciaio per utensili, le leghe dure e le leghe di titanio.
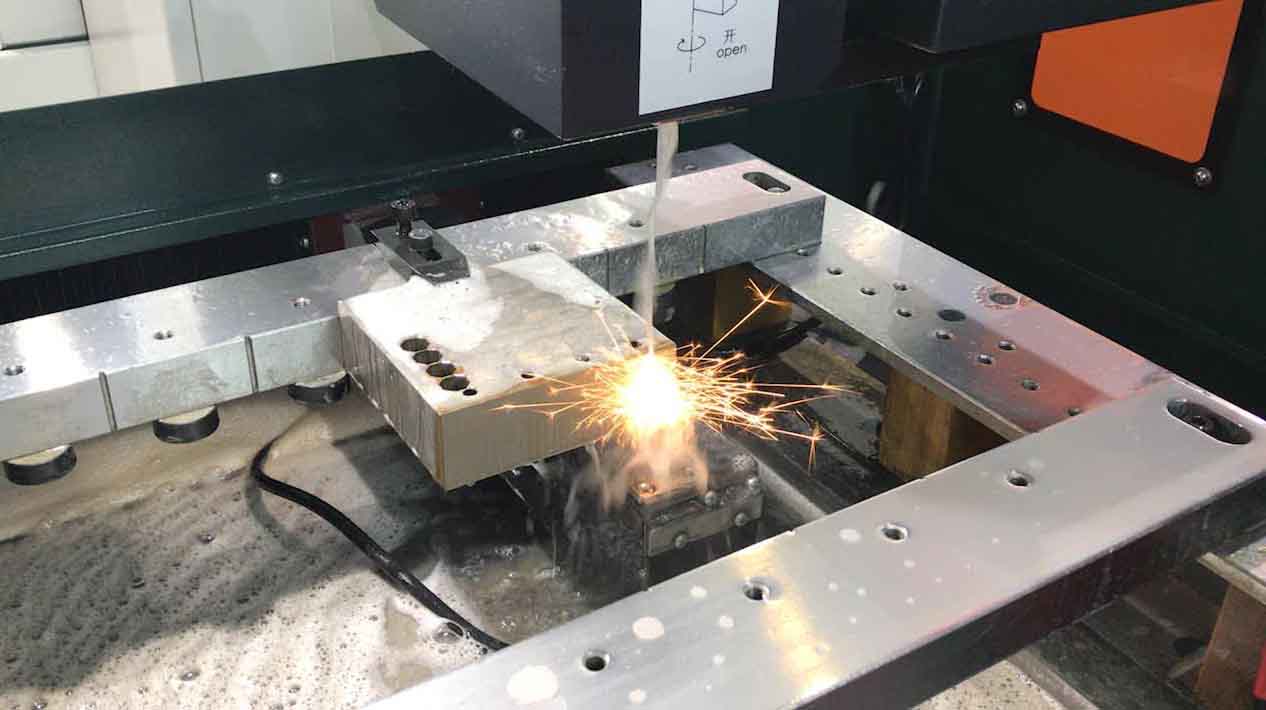
Caratteristiche principali della lavorazione a scarica elettrica:
L'elettroerosione ha un livello tecnico molto elevato nelle 8 tecniche di lavorazione CNC più comuni.
Taglio senza contatto: A differenza del taglio meccanico tradizionale, l'elettroerosione è un metodo di lavorazione senza contatto. Non c'è contatto fisico diretto tra l'utensile e il pezzo; il materiale viene rimosso attraverso la scarica elettrica.
Alta precisione: L'elettroerosione consente di ottenere lavorazioni di alta precisione, spesso raggiungendo un'accuratezza dimensionale di livello sub-micronico. Ciò la rende adatta alla produzione di stampi, modelli e altre parti di precisione.
Forme complesse: Poiché l'elettroerosione è un metodo di lavorazione senza contatto, può essere utilizzata per lavorare forme molto complesse, tra cui contorni interni, piccoli fori, scanalature e altro ancora.
Adatto per materiali ad alta durezza: L'elettroerosione è adatta a materiali di elevata durezza, poiché non si basa sulla durezza degli utensili da taglio nei metodi di taglio tradizionali.
Conclusione:
La padronanza delle 8 tecniche di lavorazione CNC più comuni è essenziale per la produzione di precisione. Ognuna di esse ha applicazioni e vantaggi specifici. Comprendendo le applicazioni e i vantaggi di tornitura, fresatura, foratura, rettifica, alesatura, piallatura, brocciatura ed elettroerosione, i produttori possono ottimizzare i processi di lavorazione per ottenere risultati superiori. Possiamo scegliere la tecnica giusta in base al materiale, alla forma, alle dimensioni e ai requisiti di superficie del pezzo.