Bole made a pre-shutdown 5-axis DMU 65 monoBLOCK maintenance DMU 95 before a 12 days break for Chinese lunar new year 2025. In 2024, we successfully fulfilled most complicated parts in our 5-axis machining center.
In this page, we will focus on introducing how we made the pre-shutdown maintenance for DMU monoBLOCK machines.
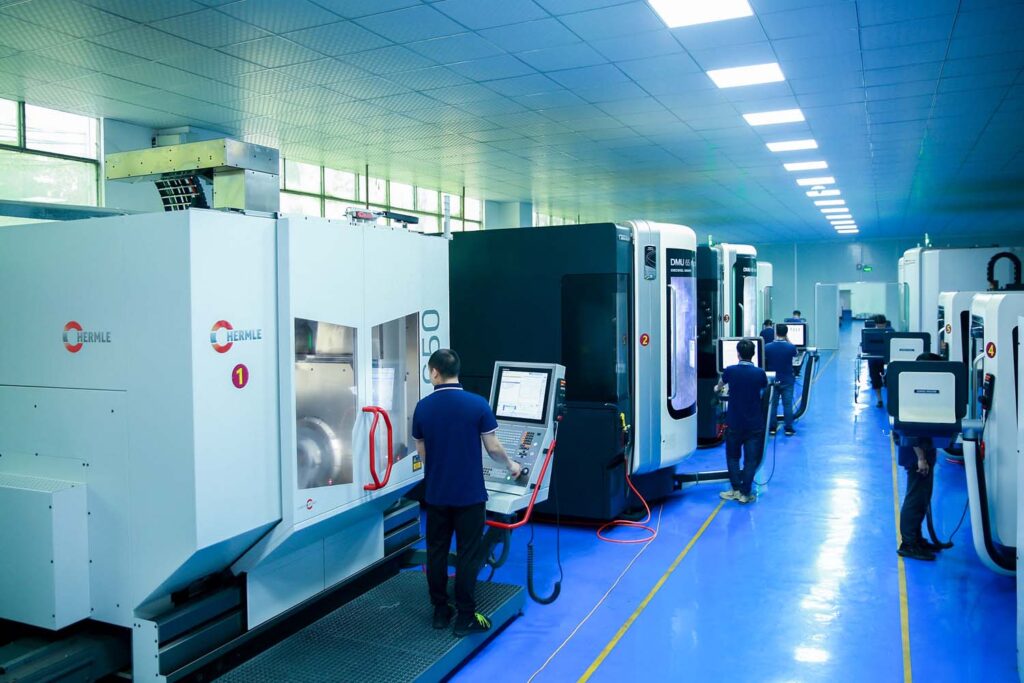
Firstly I am going to introduce DMU 65/95 monoBLOCK machines
They are high-precision, multi-axis machining centers produced by DMG Mori, a leading manufacturer in the machine tool industry.
DMU 65 monoBLOCK
The DMU 65 monoBLOCK is a versatile, five-axis machining center designed for high-precision milling tasks. It’s well-suited for a variety of applications, including automotive, aerospace, medical, and tooling industries.
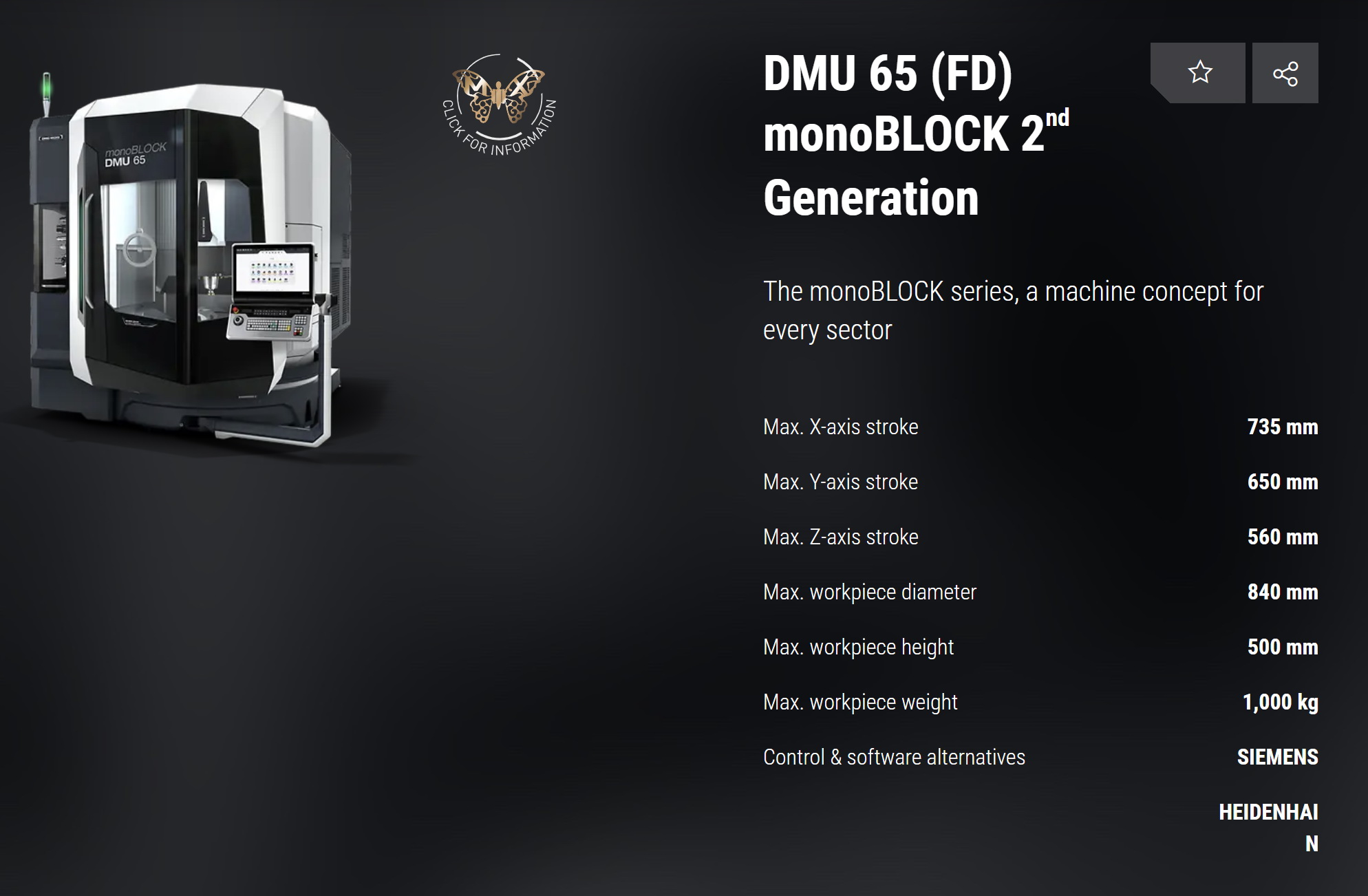
Key Features
Five-Axis Machining. Enables complex geometries and high-precision operations by allowing simultaneous movement along multiple axes.
Compact Design. Optimized for smaller workshops or production areas without compromising performance.
High-Speed Spindle. Equipped with a spindle capable of high rotational speeds, ensuring efficient material removal rates.
Advanced Control System. Utilizes DMG Mori’s intuitive control interface for easy programming and operation.
Tool Magazine. Integrated tool management system that allows for quick tool changes, minimizing downtime.
Rigid Construction. Ensures stability and accuracy during machining, reducing vibrations and improving surface finish.
Applications
Prototyping: Ideal for creating detailed prototypes with tight tolerances.
Small to Medium Batch Production: Efficient for producing parts in limited quantities without sacrificing quality.
Complex Components: Capable of handling intricate designs that require multi-axis machining.
DMU 95 monoBLOCK
The DMU 95 monoBLOCK is a robust, five-axis machining center designed for large-scale, high-precision manufacturing. It offers enhanced capabilities suitable for demanding industries such as automotive, aerospace, and heavy machinery.
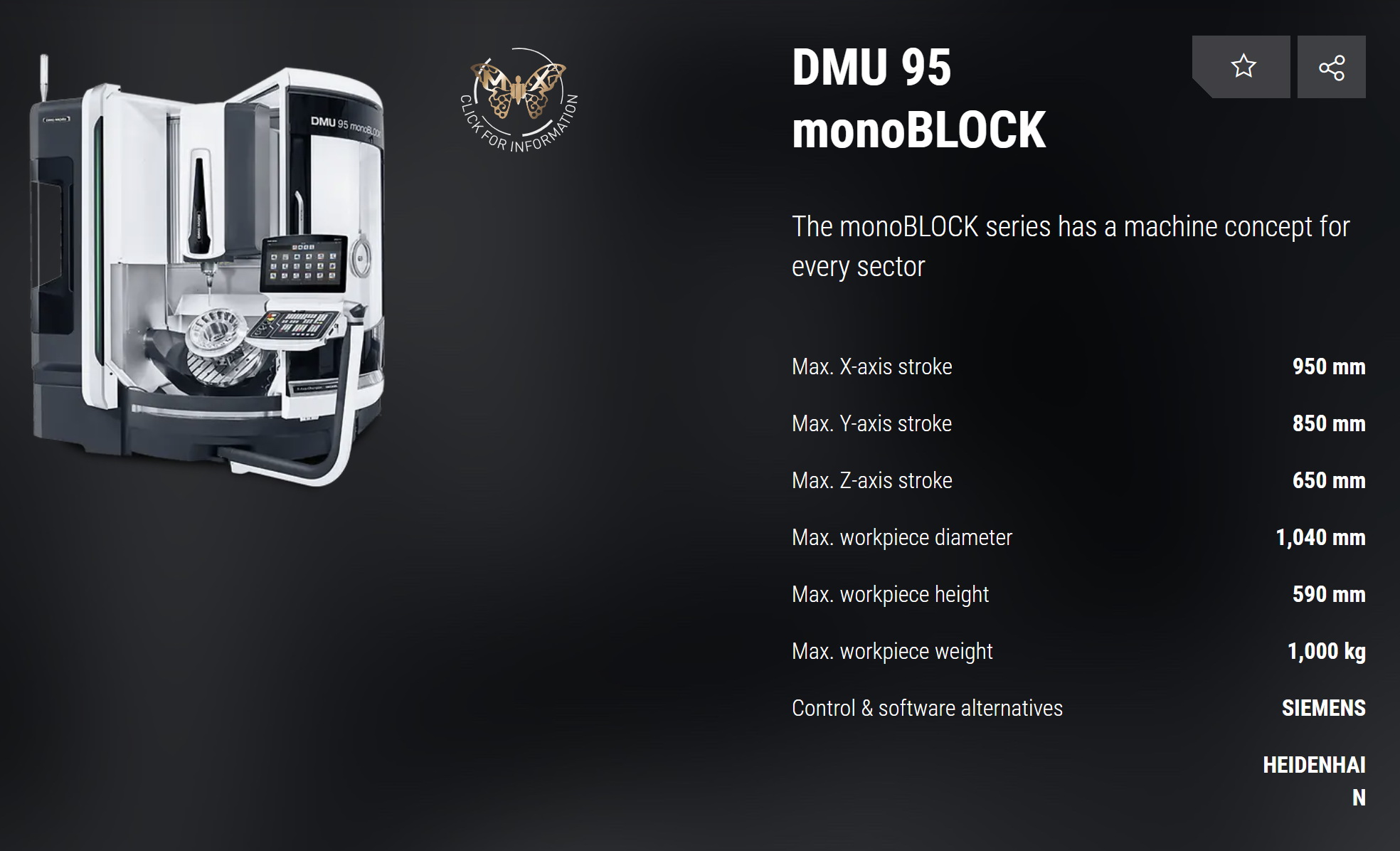
Key Features
Extended Work Envelope: Larger machining area compared to the DMU 65, allowing for the production of bigger and more complex parts.
High-Speed and High-Torque Spindle: Balances speed and power to handle a wide range of materials, from soft alloys to hardened steels.
Enhanced Stability: Features a stable base and advanced damping systems to maintain precision even under heavy cutting loads.
Advanced Control and Automation: Equipped with DMG Mori’s cutting-edge control systems, supporting automated workflows and reducing manual intervention.
Integrated Tool Management: Comprehensive tool storage and indexing system ensures seamless tool changes and inventory management.
Customization Options: Offers various configurations and add-ons to tailor the machine to specific manufacturing needs.
Applications
Large Component Manufacturing: Suitable for producing sizeable parts with high precision, such as engine blocks or aerospace components.
High-Volume Production: Efficient for mass production runs where consistency and reliability are paramount.
Complex Assemblies: Capable of machining complex assemblies that require precise alignment and multi-axis operations.
In Bole, to fulfill clients’order, when we choose DMU 95 or DMU 65 monoBLOCK for precision machining instead of 3-axis CNC machines and other common CNC machines?
Virtually speaking, to explaine how we make proper production arrangement with suitable precision machines, I need to write another long article. In this page, our emphasis is introducing to all of our ongoing clients and potential clients how we made the pre-shutdown 5-axis DMU 65 monoBLOCK maintenance. However, it’s very necessary to briefly illustrate why and how as the below:
Unparalleled advantages for precision machining
3-axis CNC machines and common CNC machines are sufficient for simpler machining tasks and lower production volumes, but the DMU 65 monoBLOCK and DMU 95 monoBLOCK machining centers offer unparalleled advantages for precision machining, particularly in industries that demand high accuracy, complex geometries, and efficient production processes. The investment in these advanced five-axis machining centers translates into: Superior precision and quality, increased productivity and efficiency, enhanced flexibility and versatility and future-proof operations.
For manufacturers aiming to excel in precision machining and cater to high-end markets, investing in DMU 65 or DMU 95 monoBLOCK machining centers provides a strategic edge that surpasses the capabilities of traditional CNC machines.
How to choose between DMU 65 and DMU 95?
Generally, we consider the following factors:
Firstly we need to view the production volume for corresponding order. The DMU 95 is better suited for high-volume production, while the DMU 65 excels in smaller batches and prototyping. Secondly we check the workpiece size. For larger components, the DMU 95 offers a more extensive work envelope. Also need to view the complexity of parts. Both machines handle complex geometries, but the DMU 95 provides additional stability for more demanding tasks. At last, before put the order into machining, we must check the space and budget. The DMU 65 has a more compact footprint and may be more cost-effective for businesses with space or budget constraints.
How We Made a Pre-shutdown 5-axis DMU 65 monoBLOCK Maintenance?
As Bole is going to make a 12 days break for lunar new year 2025, we made a fully pre-shutdown 5-axis DMU 65 monoBLOCK Maintenance DMU95 in this week.
Preparing your DMU 65 monoBLOCK and DMU 95 monoBLOCK machines for a 12-day hiatus requires thoughtful planning to ensure their longevity, maintain performance, and prevent potential issues that can arise from extended periods of inactivity. Below are special maintenance suggestions tailored for such a scenario:
Machine Cleaning
Remove Debris and Chips
It’s crucial to remove chips from the machines. Before cleaning, we need to ensure all metal chips, swarf, and debris are meticulously cleared from the machine bed, spindle area, tool changers, and workholding components. Then we use brushes, compressed air (sparingly and carefully to avoid moisture), or vacuum systems designed for CNC machines. At last, we made surface cleaning: Wipe down all accessible surfaces, including linear guides, ball screws, and control panels, using lint-free cloths to remove dust and residual contaminants.
Clean Coolant System
Engineers in Bole with well pre-shutdown training drained or stabilize the coolant. Depending on manufacturer recommendations, either drain the coolant system to prevent stagnation and microbial growth or ensure the coolant is properly mixed and treated to maintain its integrity during the break. Then made flush if necessary. If you opt to drain, consider flushing the coolant lines with fresh coolant before restarting to purge any contaminants that may have settled.
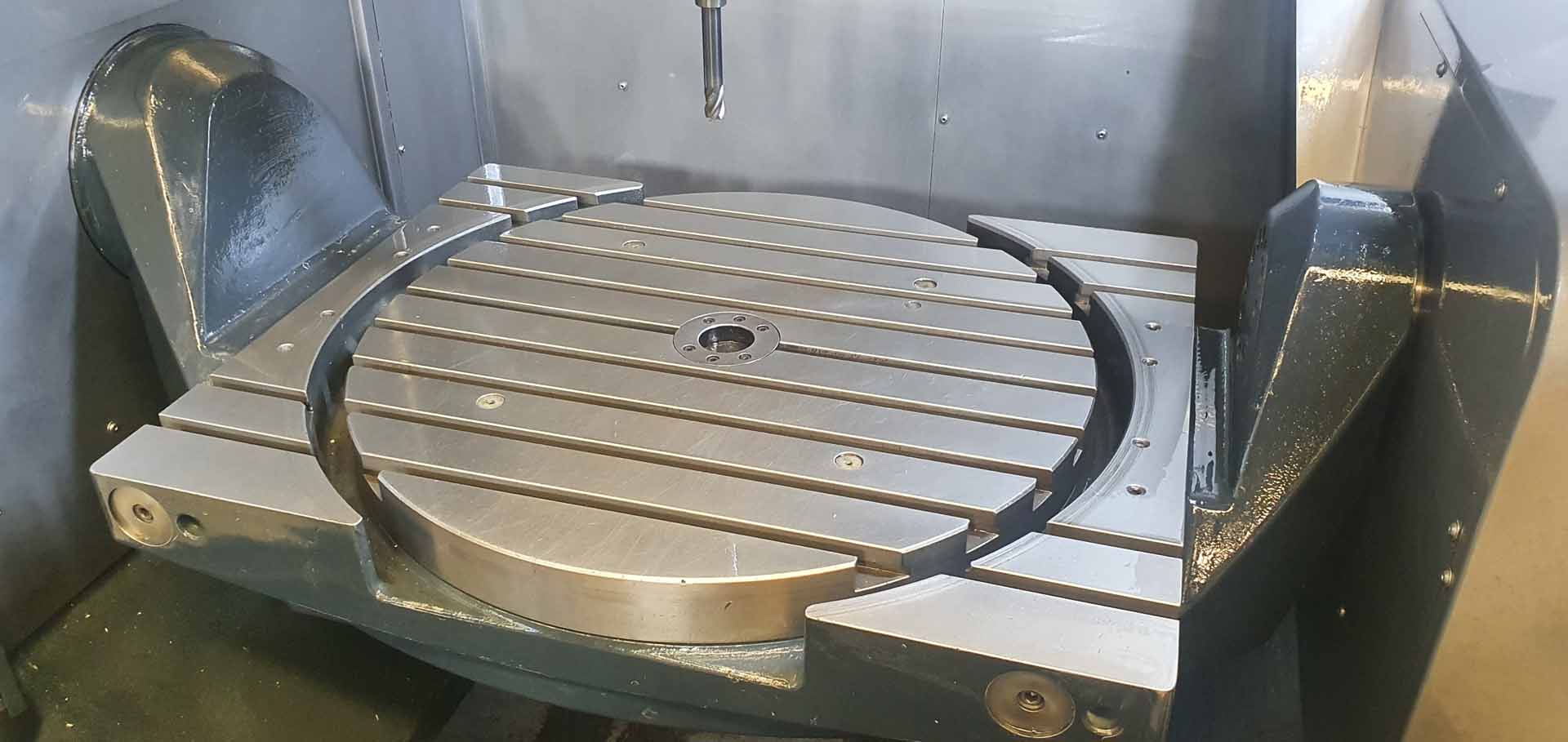
Lubrication and Protection
Lubricate Moving Parts
This technique article is supported by ChatGPT. However, we also consulted our engineer team for a complete DMU 65 monoBLOCK maintenance. We can guarantee that all our countermeasures are highly fit DMG Mori standard operations.
Re-lubricate all critical moving components such as linear guides, ball screws, spindle bearings, and any other accessible lubrication points. Use the lubricants specified by DMG Mori to prevent corrosion and ensure components are protected during inactivity. Ensure that no excess lubricant is left on surfaces where it can attract dust or debris.
Anti-Corrosion Measures
Bole applied appropriate anti-corrosion sprays or coatings to exposed metal surfaces to prevent rust and corrosion. We also used protective covers or seals on areas susceptible to moisture ingress, such as control panels and electrical connectors.
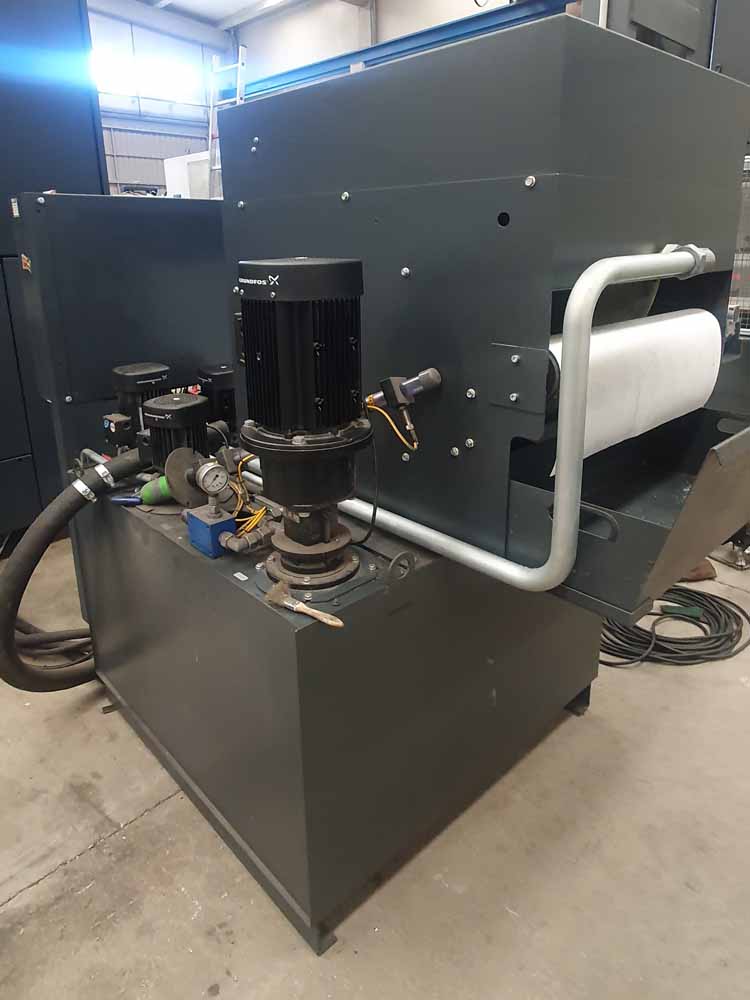
Proper Shutdown Procedures
Follow Manufacturer’s Guidelines
Naturally, our engineers initially followed user manuals for specific shutdown procedures recommended by DMG Mori. Each machine is an independent system. Therefore, we need systematic shutdown. We ensured all axes return to their home positions, spindle stops, coolant pump turns off, and all auxiliary systems are properly shut down.
Power Down Safely
After the machine has been properly shut down, we disconnected it from the main power source to prevent electrical issues, especially in areas prone to power surges or outages. Implement Lock-Out Tag-Out (LOTO) procedures to ensure that the machine cannot be inadvertently powered on during the break.
Environmental Control
Control Temperature and Humidity
In Bole factory, all workshops have stable environment with comfortable air conditioners. We ensure the machines are stored in an environment with controlled temperature and humidity to prevent thermal expansion issues and moisture-related damage. We periodically power on humidifiers and moisture absorbers in the machine’s vicinity to maintain optimal humidity levels.
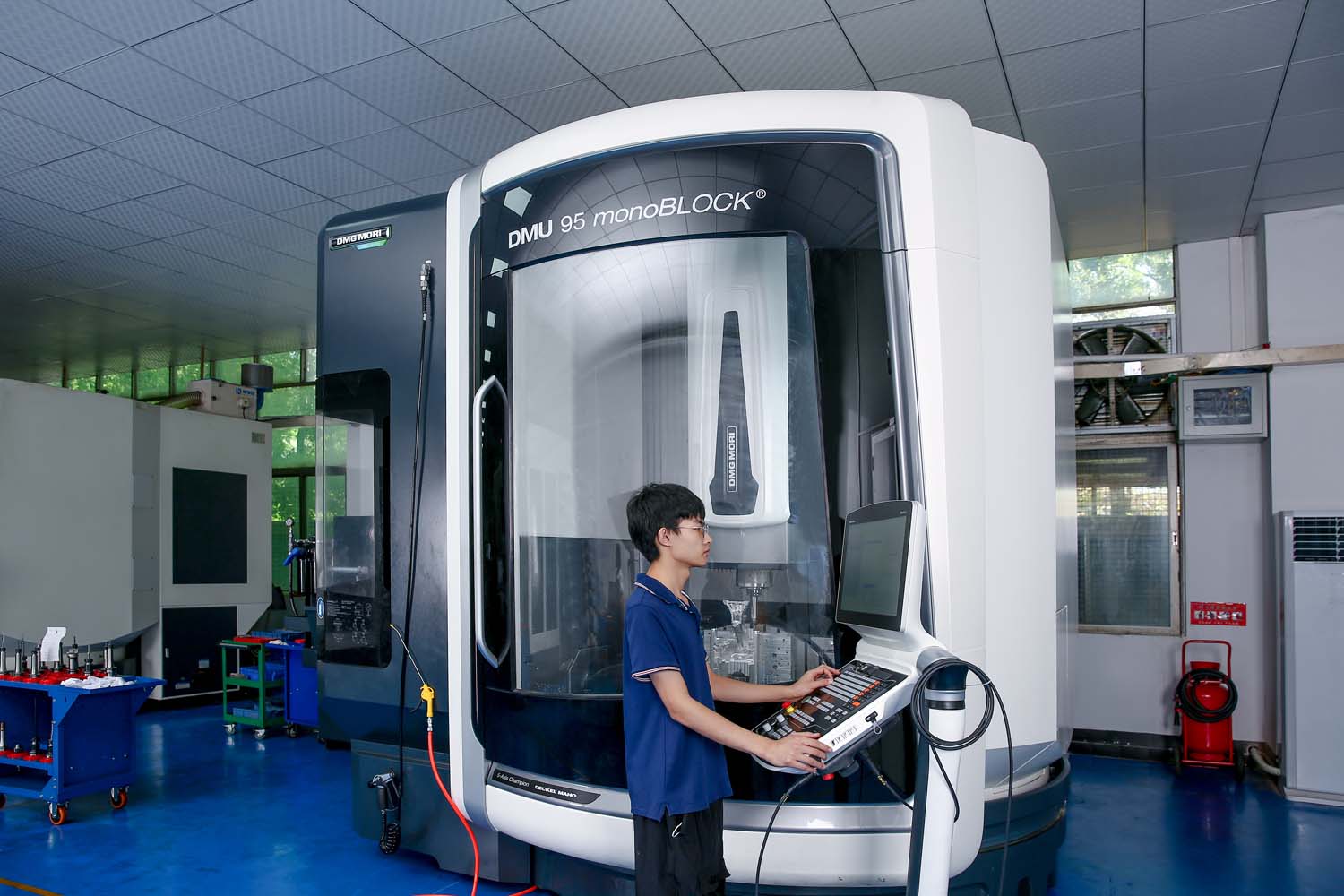
Protect from Dust and Contaminants
We used breathable machine covers or protective tarps to shield the machine from dust, airborne particles, and potential contaminants. Avoid plastic covers that can trap moisture.
Documentation and Record-Keeping
Maintenance Logs
We also documented all maintenance activities performed before the break, including cleaning, lubrication, and any parts replaced or inspected. Carefully do more small but important workd: Note the machine’s operational status, settings, and any observations that may be relevant upon resumption.
Backup Machine Settings
Back up control system settings, tool libraries, and any custom configurations to prevent data loss and facilitate quick restoration after the break.
Security Measures
Physical Security
It’s important to set restrict access before the break. We ensure that only authorized engineer have access to each monoBLOCK machine during the break to prevent unauthorized use or tampering. And, we set alarm systems. Professionals do excellent job. Engineer activate existing security and alarm systems to monitor the machine’s environment.
Operator Notifications
Naturally, we need to inform all staff in Bole. Communicate the machine’s downtime to all relevant staff to prevent accidental operation and to ensure that maintenance preparations are respected.
Final Checks
Inspect Guards and Safety Devices
It’s never be an easy thing to maintain a CNC machining enterprise. All safety measures we need to do before the break. Do a lot of safety compliance things. We need to verify that all machine guards, emergency stops, and safety devices are in place and functioning correctly before shutting down. After a careful check, we replaced all worn components for a better status during the break and an absolutely well conditions for restarting. We addressed any wear or issues with safety components to maintain a safe environment upon machine reactivation.
Test Shutdown
How to guarantee all things are handled correctly? Must do functionality check after all operations done. As a final operation, Bole’s engineers perform a final test shutdown to ensure that all systems power down correctly and that there are no lingering issues that need attention. Monitor Upon Return: Plan to conduct a thorough inspection and test run once the break concludes to ensure the machine is operational and no issues arose during the downtime.
Additional Recommendations
Generally, if an engineers has problem that won’t get efficient response from Bole engineers team, he can also consult DMG Mori support. He can reach out to DMG Mori’s technical support or the local representative for any machine-specific recommendations or updates related to extended periods of inactivity. However, in Bole, our engineers got very very complete operation training before handling each machine. During the past 20 years development, we set up mature training systems to guarantee our production capacity and quality.
We also need to make a plan for restarting procedures so that we don’t need to cost too much time for restarting our production line in 12 days later. All things will run much smoothly. In detail, we prepared a checklist for restarting the machines after the break, including re-lubrication, coolant system checks, and calibration as necessary.
By following these specialized maintenance steps before a 12-day break, we can protect our DMU 65 monoBLOCK and DMU 95 monoBLOCK machines from potential issues related to prolonged inactivity. Proper preparation ensures that Bole machines remain in optimal condition, ready to resume high-precision operations with minimal downtime and disruption upon our return. That’s all the DMU 65 monoBLOCK maintenance we made before our CNY holiday break.