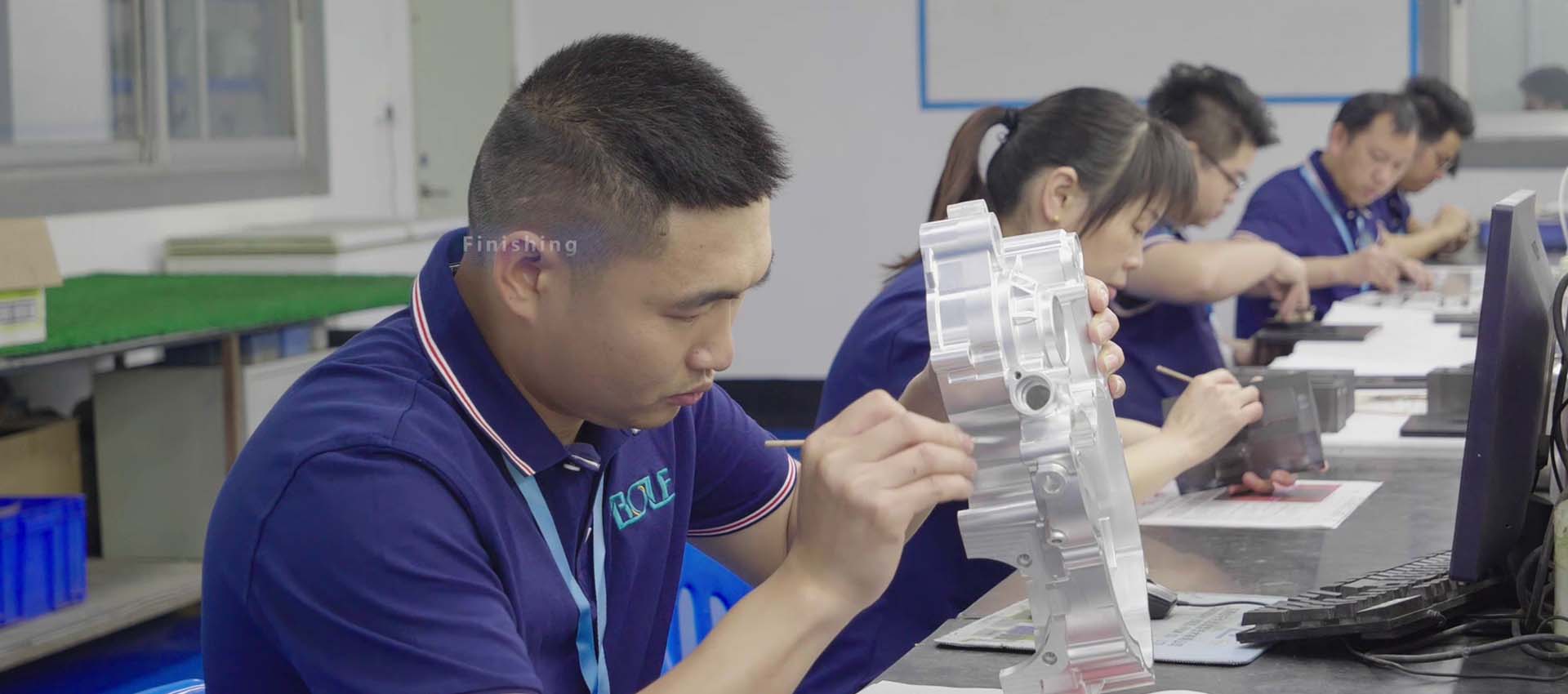
CNC MACHINING SURFACE FINISHING SERVICE
Bole’s CNC machining surface finishing service: Anodizing, Deoxidizing, Grinding, Oxide coating, Lapping, Polishing, Pretreatment, satin finishing… No functionality damage to the parts & Improve the aesthetics of the parts
Don’t know how to choose? Just inquire us for free
The surface finishing service in Bole is actually not limited to CNC machining surface finishing. We are also good at the surface finishing for plastics parts, various technique including handle operation by experienced workers.
What is surface finishing?
Surface finishing is the final step in the manufacturing process of CNC machined parts, where the surface of a part is treated, coated, or modified to achieve specific properties. It involves applying various techniques and processes to enhance the appearance, functionality, and durability of the part, ensuring it meets the requirements of its intended application. Surface finishing is not just about aesthetics; it plays a critical role in determining how a part performs under real-world conditions.
Why need surface finishing in precision processing?
When CNC machining produces a part, the raw finish often includes tool marks, rough edges, or surface imperfections. While these parts may meet dimensional and structural requirements, they may not perform optimally or look professional without additional finishing. Surface finishing addresses these issues by refining the part’s surface to achieve the desired smoothness, texture, or protective properties.
Keep compliance with stricter sndustry standards
Some industries have strict standards for surface finishes to ensure safety, functionality and longevity. For example:
Medical devices require biocompatible finishes. as
Aerospace components must meet corrosion and wear resistance requirements.
Food-grade equipment needs non-toxic, easy-to-clean finishes.
Proper surface finishing ensures compliance with these regulations and certifications.
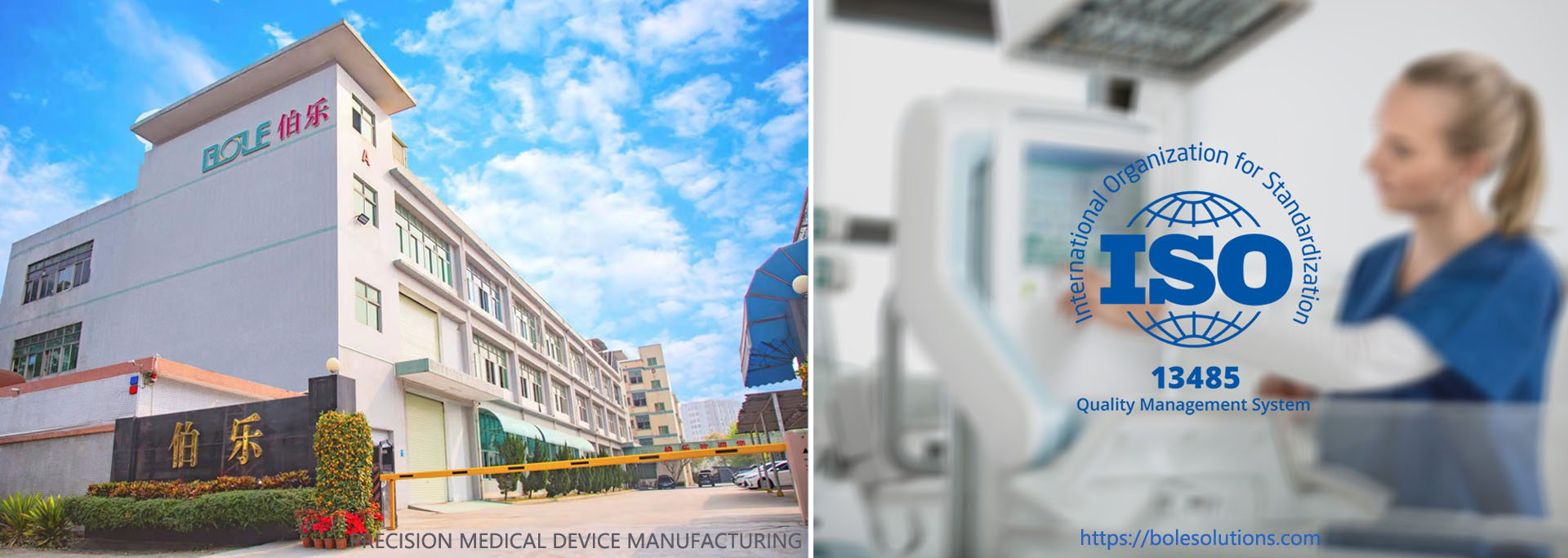
Related reading: 10 important standards for medical devices
Why is Surface Finishing so Important?
Benefits of surface finishing: Corrosion resistance, improved aesthetics, wear resistance and better performance in specific applications. Surface finishing is a critical step in CNC machining that goes beyond just improving the appearance of a part. It directly impacts the performance, durability and functionality of the final product, making it an essential consideration for nearly every industry that uses precision-machined components.
Enhance Parts Corrosion Resistance
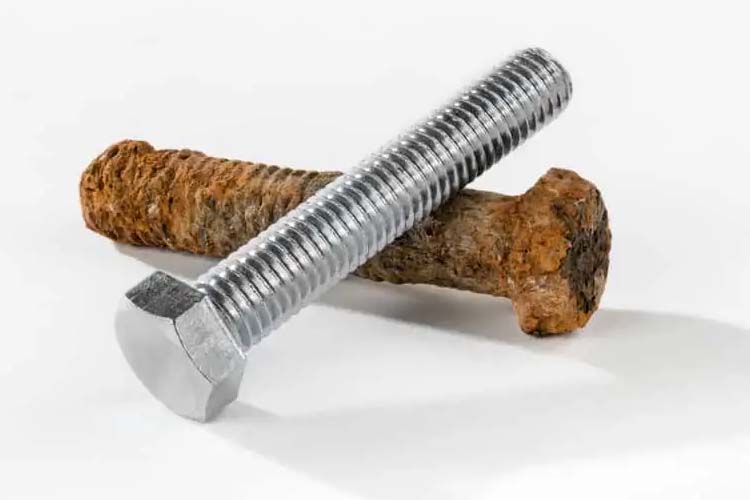
Many materials, especially metals like aluminum, steel, and brass, are prone to corrosion when exposed to moisture, air, or harsh environments.
Surface finishes such as anodizing, passivation, or powder coating create a protective barrier that prevents oxidation and rust, significantly extending the lifespan of the part.
For industries like aerospace, marine, and automotive, where parts are exposed to extreme weather or corrosive chemicals, corrosion resistance is essential.
Processing an Attractive Appearance
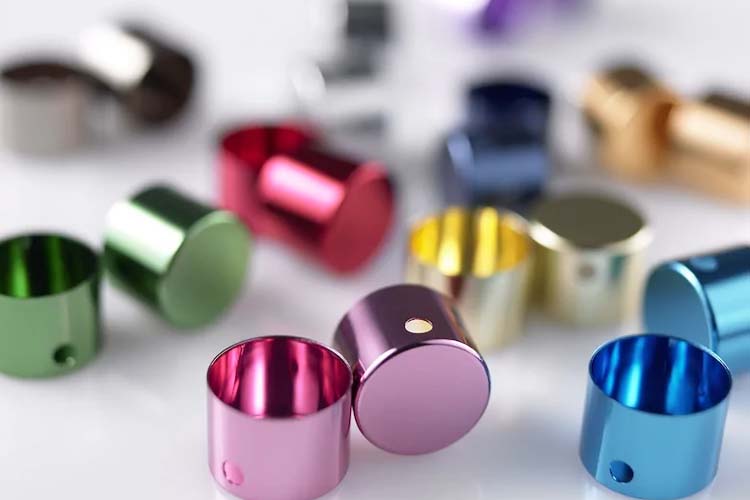
Surface finishing enhances the visual appeal of CNC machined parts, making them more attractive and professional-looking.
Techniques like polishing, brushing, or painting can create a sleek, clean, and high-quality appearance.
Customizable finishes, such as colored anodizing or powder coating, allow for branding opportunities or specific design preferences, making the product stand out in competitive markets like consumer electronics or luxury goods.
Much Better Wear Resistance
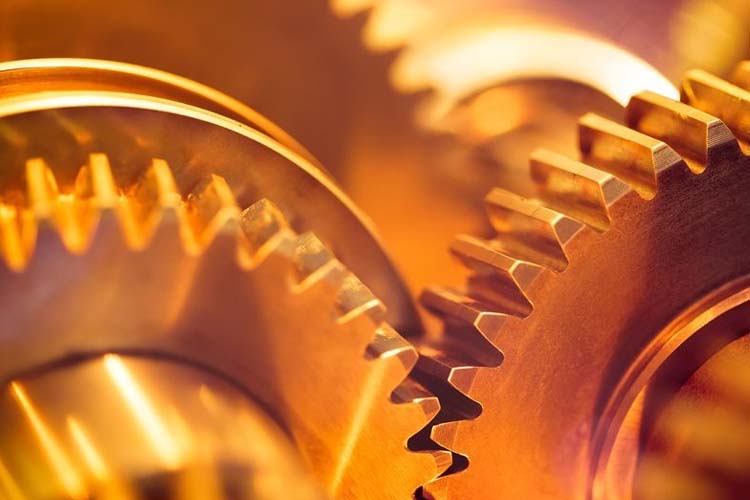
Parts that are subject to frequent friction, movement, or mechanical stress can wear out quickly without proper surface finishing.
Finishes like hard anodizing, electroplating, or ceramic coatings add a layer of hardness to the surface, reducing wear and tear.
This is particularly important for industrial machinery, automotive components, and medical devices, where durability and reliability are non-negotiable.
Enhanced Surface Properties and Functionality
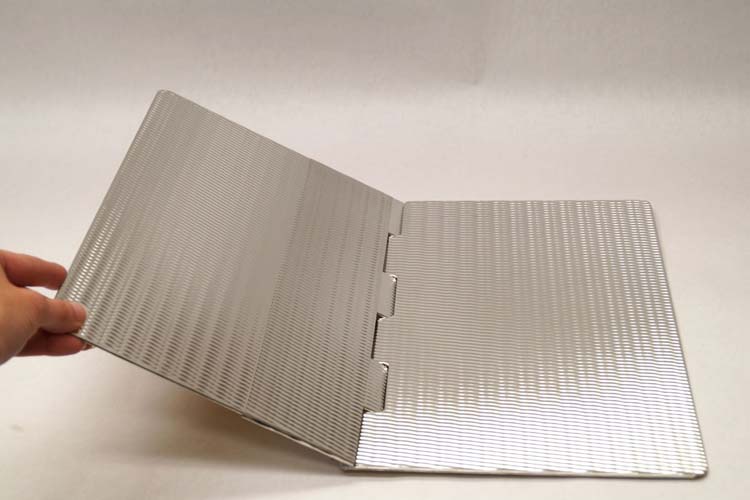
Surface finishing can improve the functionality of a part by altering its surface properties: Reduced friction: Polished or coated surfaces can improve the efficiency of moving parts.
Electrical insulation or conductivity: Finishes like anodizing can provide electrical insulation, while electroplating with conductive materials (e.g., gold, silver) can enhance conductivity.
Thermal resistance: Certain finishes can improve a part’s ability to withstand high temperatures or dissipate heat more effectively.
These enhancements are crucial in high-performance applications like electronics, aerospace, and medical technology.
Meet Stricter Hygiene Standards
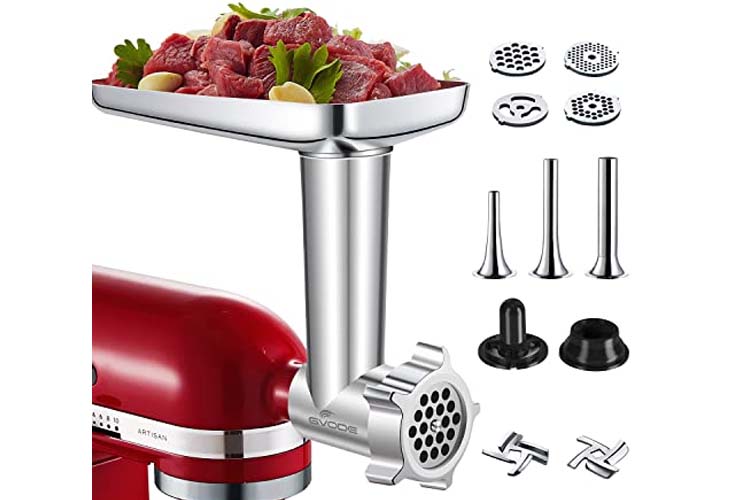
Smooth and polished finishes make parts easier to clean and maintain, which is vital for industries like food processing, pharmaceuticals, and medical devices.
Surface treatments like passivation not only improve corrosion resistance for stainless steel but also remove contaminants, ensuring compliance with strict hygiene standards.
Enhance Parts Fatigue Resistance
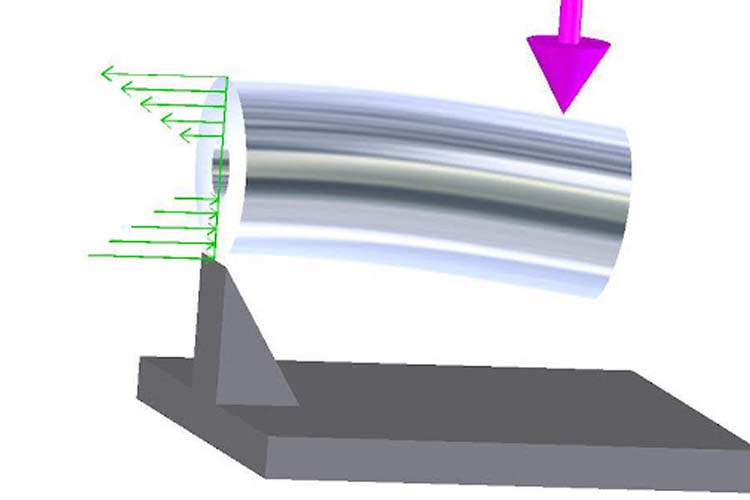
Surface finishing can improve a part’s resistance to fatigue by reducing surface imperfections such as micro-cracks or rough areas that can lead to stress concentration.
Processes like shot peening or hard anodizing strengthen the surface, making it more resistant to cracking or failure under repeated stress.
Coatings Prevent From Harsh Chemicals
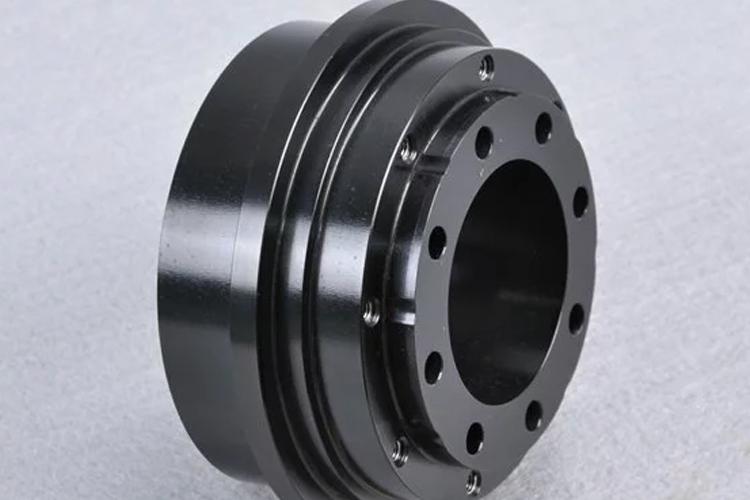
In industries like chemical processing or oil and gas, parts are often exposed to harsh chemicals that can degrade untreated surfaces.
Finishes like electroplating (e.g., nickel or chrome) or ceramic coatings provide a protective barrier, ensuring the part remains functional in aggressive environments.
Smooth Surface Adds Parts Precision
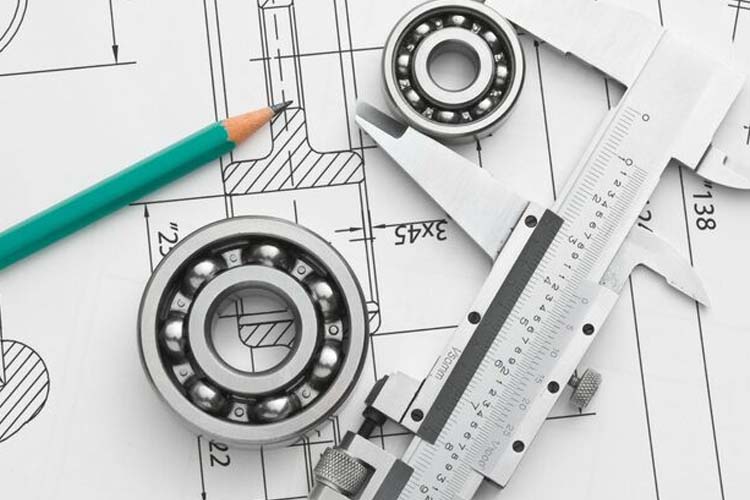
Surface finishing can fine-tune the dimensions of a part by adding or removing material, ensuring a precise fit in assemblies.
Processes like grinding, lapping, or polishing help achieve tight tolerances and smooth surfaces, which are critical in precision engineering applications.
Change Parts Reflectivity: Polishing or Matte
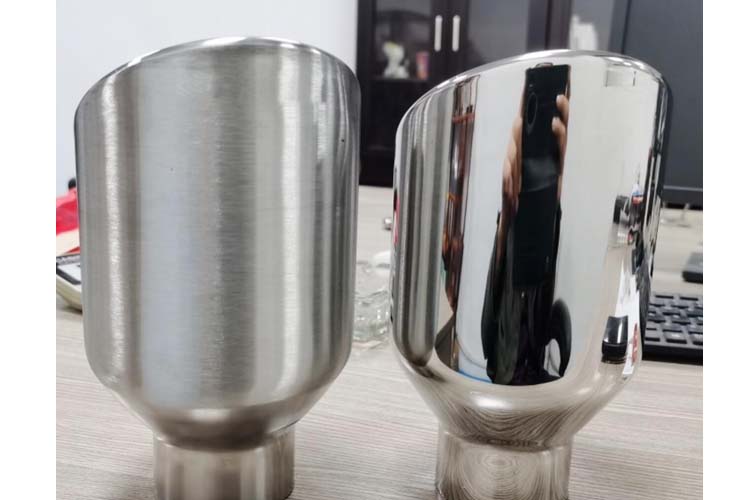
Some applications require specific light-reflecting or light-absorbing properties. For instance:
Polished surfaces are often used in optical or decorative applications for high reflectivity.
Matte finishes like bead blasting reduce glare and reflections, making them ideal for camera components, displays, or aerospace parts.