Es ist notwendig, die 8 gängigen CNC-Bearbeitungsverfahren zu kennen, wenn man etwas über ihre Anwendungen, Vorteile und wichtigsten Merkmale erfahren möchte. In diesem Artikel werden wir die wichtigsten CNC-Bearbeitungstechniken wie Drehen, Fräsen, Bohren, Schleifen, Ausbohren, Hobeln, Räumen und Funkenerosion (EDM) vorstellen.
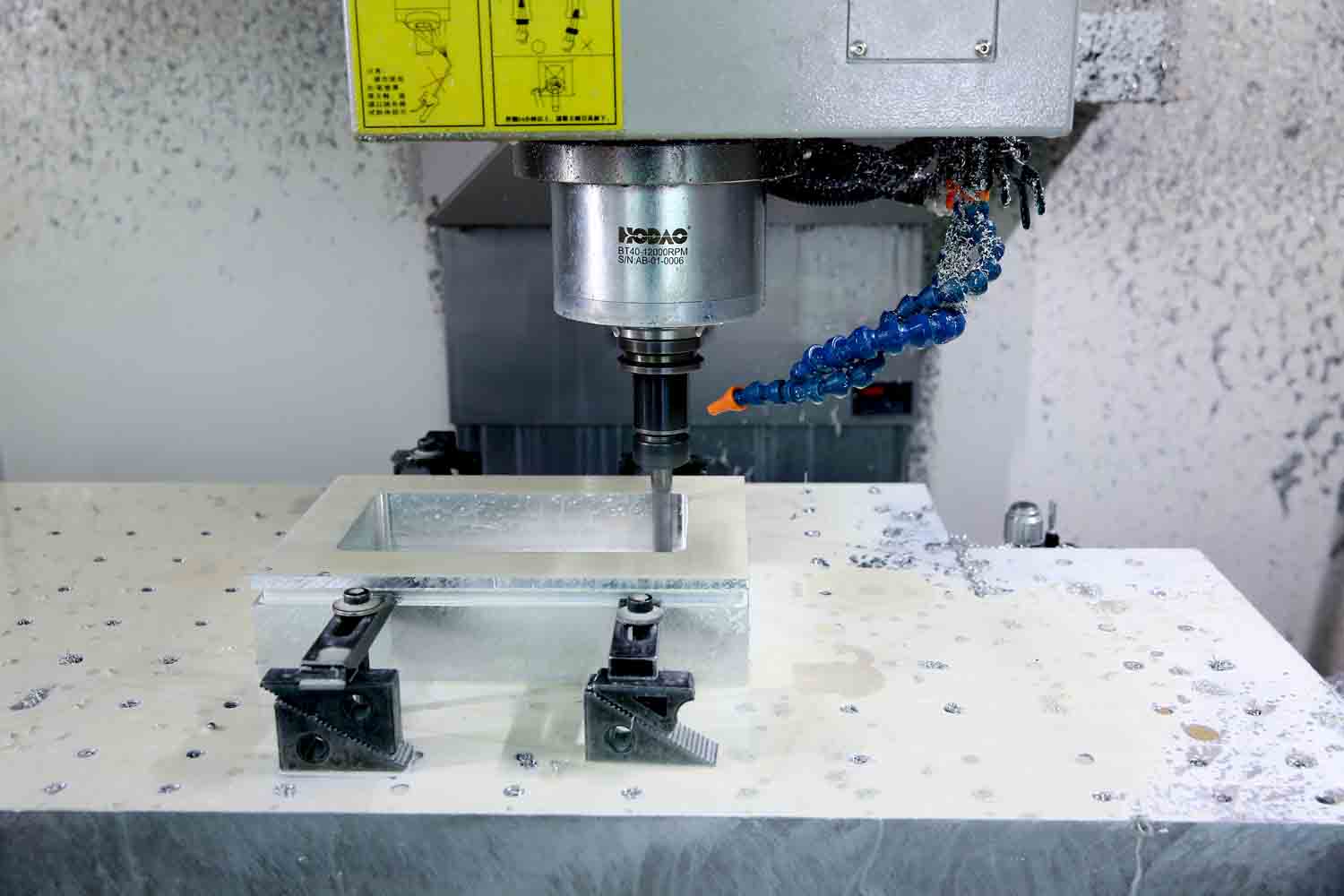
Es ist sehr wichtig, zu untersuchen, wie ein Produkt bearbeitet wird, wenn wir hoffen, seine Kostenstruktur zu überblicken. Das Erlernen der 8 gängigen CNC-Bearbeitungstechniken wird Ihnen sehr helfen.
In der verarbeitenden Industrie sind mechanische Bearbeitungsverfahren ein wesentlicher Bestandteil. Mechanische Bearbeitung ist der Prozess der Umwandlung von Rohmaterialien in die gewünschte Form, Größe und Oberflächenqualität, der eine Vielzahl von Präzisionsbearbeitungsmethoden umfasst, um den Anforderungen der verschiedenen Teile gerecht zu werden. Im Folgenden werden 8 gängige mechanische Bearbeitungsverfahren näher erläutert.
Sie können auch direkt erkunden Bole's CNC-Bearbeitungsdienst wenn Sie ein Meister auf diesem Gebiet sind.
Wenden
Beim Drehen wird das Werkstück auf einer rotierenden Werkstückhalterung fixiert und dann mit einem Schneidewerkzeug schrittweise bearbeitet, um die gewünschte Form und Größe zu erhalten. Dieses Verfahren eignet sich für die Herstellung zylindrischer Teile wie Wellen und Hülsen. Das Drehverfahren und die Wahl des Werkzeugs beeinflussen die Form und die Oberflächenrauheit des Endprodukts.

Das Drehen kann in verschiedene Arten unterteilt werden, darunter Außendrehen, Innendrehen, Plandrehen und Gewindedrehen.
Beim Außendrehen werden in der Regel Formen wie Wellen, Zylinder und Kegel bearbeitet; beim Innendrehen dringt das Werkzeug in die Innenbohrung des Werkstücks ein, um den Durchmesser und die Oberfläche auf die gewünschte Größe und Genauigkeit zu bearbeiten; beim Plandrehen werden in der Regel ebene Flächen, wie die Grund- oder Stirnfläche eines Teils, hergestellt; beim Gewindedrehen wird die Gewindeform durch schrittweises Bewegen der Schneide des Werkzeugs relativ zur Werkstückoberfläche, einschließlich Innen- und Außengewinde, geschnitten.
Fräsen
Beim Fräsen wird ein Schneidwerkzeug auf der Oberfläche des Werkstücks gedreht, um das Material zu schneiden. Dies ermöglicht die Herstellung von Teilen mit komplexen Formen wie Ebenen, konkaven und konvexen Flächen und Zahnrädern durch die Steuerung der Werkzeugbewegung. Zum Fräsen gehören das Flachfräsen, das Vertikalfräsen, das Schaftfräsen, das Zahnradfräsen und das Profilfräsen, die jeweils für unterschiedliche Bearbeitungsanforderungen geeignet sind.
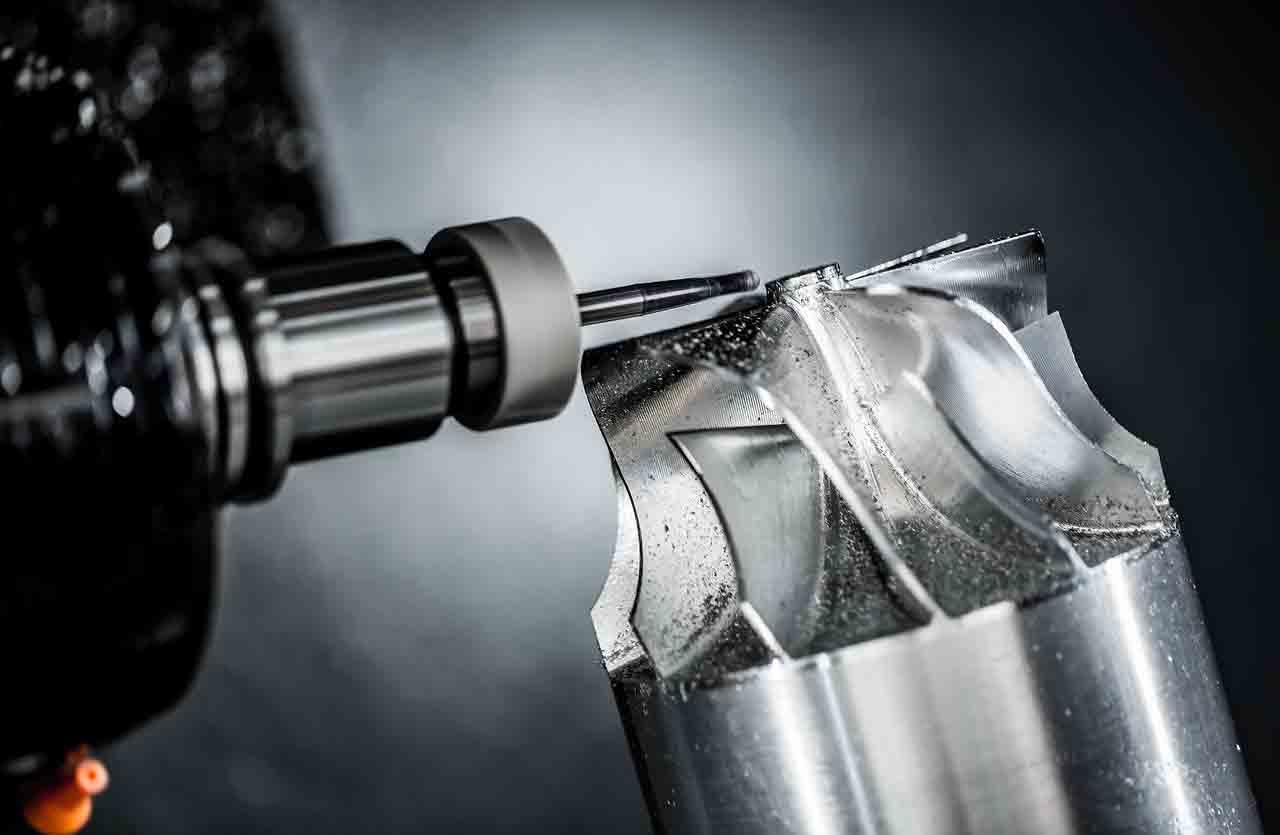
Beim Flachfräsen schneidet die Schneide des Werkzeugs auf der Werkstückoberfläche, um eine ebene Fläche zu erhalten; das Vertikalfräsen wird für die Bearbeitung von Nuten und Löchern entlang der Höhenrichtung des Werkstücks verwendet; beim Stirnfräsen wird an der Seite des Werkstücks geschnitten und für die Bearbeitung von Profilen, Nuten und Kanten verwendet; beim Zahnradfräsen werden in der Regel spezielle Werkzeuge mit Schneiden verwendet, um die Form der Zahnräder zu schneiden; das Profilfräsen wird für die Bearbeitung komplexer Kurven oder Konturen verwendet, wobei der Werkzeugweg anhand der Kontur genau gesteuert wird.
Bohren
Beim Bohren wird das Material mit einem rotierenden Bohrer in das Werkstück geschnitten, um Löcher mit dem gewünschten Durchmesser und der gewünschten Tiefe zu erzeugen, was in der Fertigung, im Bauwesen und in der Instandhaltung weit verbreitet ist. Beim Bohren wird häufig zwischen konventionellem Bohren, Zentrierbohren, Tieflochbohren, mehrachsigem Bohren und anderen Arten unterschieden.

Beim konventionellen Bohren werden Bohrer mit spiralförmigen Schneiden verwendet, typischerweise für kleinere Löcher und allgemeine Bohranforderungen; beim Zentrierbohren wird ein kleines Loch auf der Werkstückoberfläche erzeugt, bevor ein größerer Bohrer verwendet wird, um die genaue Positionierung größerer Löcher zu gewährleisten; beim Tieflochbohren werden tiefere Löcher bearbeitet, wofür spezielle Bohrer und Kühltechniken erforderlich sind, um Genauigkeit und Qualität zu gewährleisten; beim mehrachsigen Bohren werden mehrere Bohrer mit unterschiedlichen Winkeln gleichzeitig verwendet, was sich für Fälle eignet, in denen mehrere Löcher gleichzeitig gebohrt werden müssen.
Bohren ist ein sehr gängiges Bearbeitungsverfahren und gehört zu den gängigen CNC-Bearbeitungstechniken.
Schleifen
Beim Schleifen wird die Oberfläche des Werkstücks mit Hilfe eines Schleifmittels schrittweise bearbeitet, um die gewünschte Form, Größe und Oberflächenqualität zu erzielen. Schleifen wird üblicherweise für Teile mit hohen Anforderungen an Präzision und Oberflächenqualität verwendet, z. B. für Formen, feinmechanische Teile und Werkzeuge.
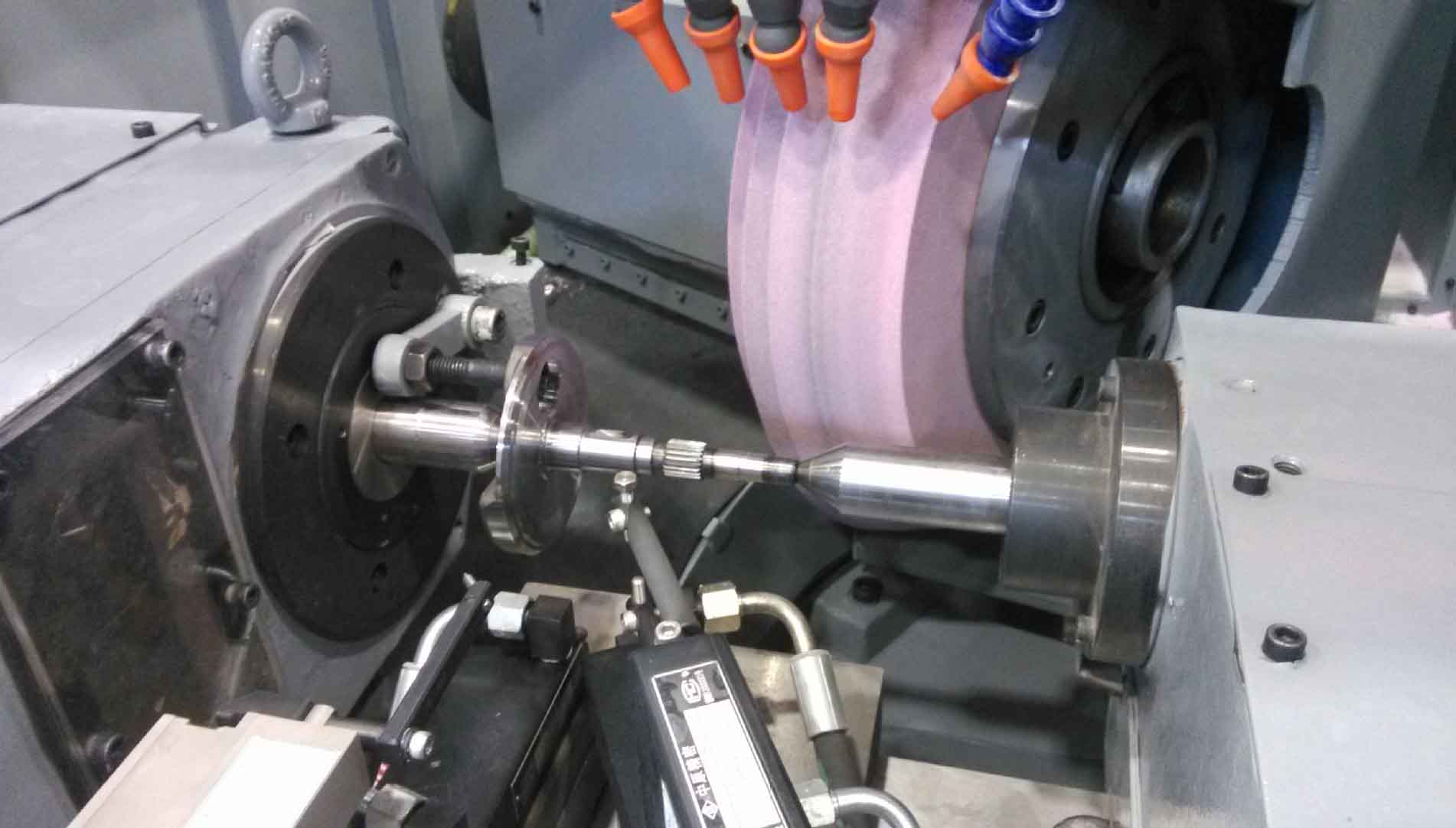
Das Schleifen wird unterteilt in Flachschleifen, Außenschleifen, Innenschleifen und Profilschleifen. Das Flachschleifen wird für die Bearbeitung flacher Werkstückoberflächen verwendet, um glatte Oberflächen und präzise Abmessungen zu erzielen; das Außenschleifen wird für die Bearbeitung der äußeren zylindrischen Oberfläche von Werkstücken wie Wellen und Stiften verwendet; das Innenschleifen wird für die Bearbeitung der inneren Oberfläche von Löchern, wie Innenlöchern und Wellenlöchern, verwendet; das Profilschleifen wird für die Bearbeitung komplexer Konturformen, wie der Schneidkante von Formen und Werkzeugen, verwendet.
Bohren
Beim Bohren werden kreisförmige Innenlöcher in Werkstücke gebohrt, indem mit einem rotierenden Werkzeug in vorhandene Löcher geschnitten wird, um genaue Abmessungen und Ebenheitsziele zu erreichen. Im Gegensatz zum Bohren, bei dem die Löcher durch Schneiden von Material auf der Werkstückoberfläche entstehen, wird beim Aufbohren das Werkzeug in das Werkstück eingeführt, um Löcher zu schneiden.
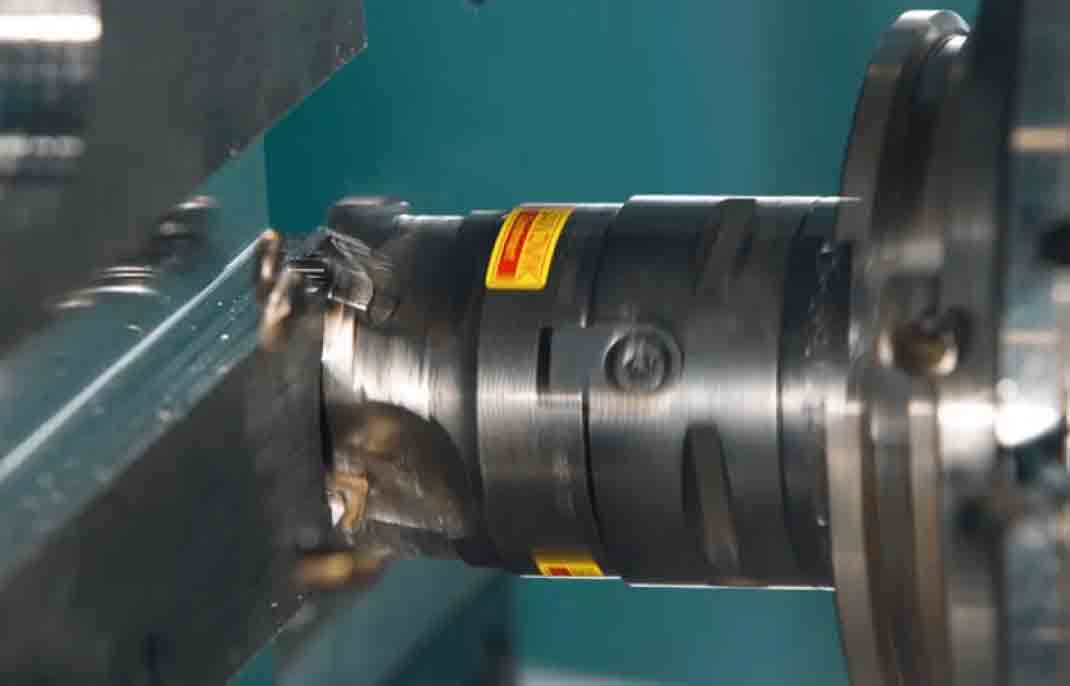
Beim Bohren unterscheidet man zwischen manuellem Bohren und CNC-Bohren. Manuelles Ausbohren eignet sich für die Kleinserienfertigung und einfache Bearbeitungsaufgaben. Beim CNC-Bohren werden Schnittwege, Vorschubgeschwindigkeiten und Drehzahlen programmiert, um eine automatisierte Hochpräzisionsbearbeitung zu erreichen.
Hobeln
Beim Hobeln wird das Material auf der Werkstückoberfläche mit einem Hobel bearbeitet, um die gewünschte ebene Oberfläche, die genauen Abmessungen und die Oberflächenqualität zu erzielen. Hobeln wird in der Regel für die Bearbeitung von ebenen Oberflächen größerer Werkstücke, wie z. B. Sockel und Betten, verwendet. Es bietet eine ebene Oberfläche für Werkstücke, die mit anderen Komponenten zusammenpassen.
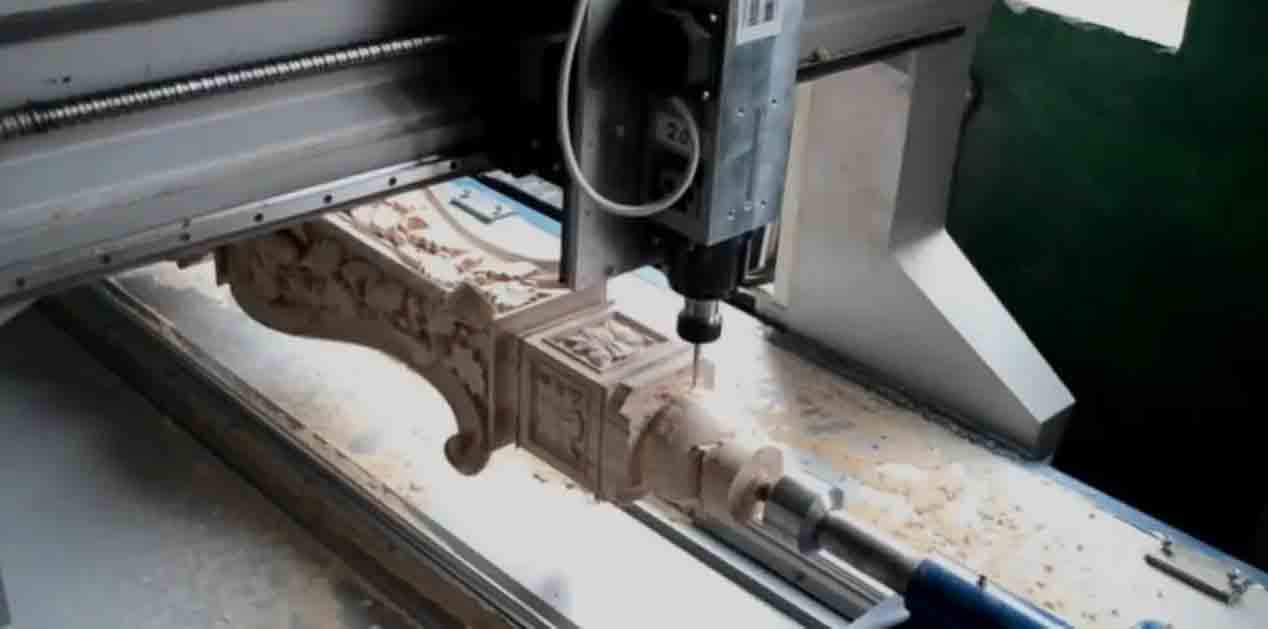
Das Hobeln wird in der Regel in eine Schrupp- und eine Schlichtphase unterteilt. In der Schruppphase schneidet die Hobelmaschine tief, um das Material schnell zu entfernen. In der Schlichtphase wird die Schnitttiefe verringert, um eine höhere Oberflächenqualität und Maßgenauigkeit zu erreichen. Das Hobeln kann manuell oder automatisch erfolgen. Manuelles Hobeln eignet sich für Kleinserien und einfache Bearbeitungsaufgaben; beim automatischen Hobeln werden automatisierte Werkzeugmaschinen eingesetzt, um die Bewegung der Hobelmaschine zu steuern und so einen stabileren und effizienteren Bearbeitungsprozess zu ermöglichen.
Räumen
Beim Räumen werden die Schnitte mit einem Räumwerkzeug schrittweise vertieft, um komplexe Innenkonturen zu erzeugen, die üblicherweise für die Bearbeitung von Konturen, Nuten und Löchern von Werkstücken mit komplexen Formen verwendet werden. Durch das Räumen kann eine hohe Bearbeitungsgenauigkeit und Oberflächenqualität erreicht werden, die sich für Teile eignet, die eine hohe Präzision und gute Oberflächenqualität erfordern. Es wird allgemein in Flachräumen, Konturräumen, Nutenräumen und Lochräumen unterschieden.
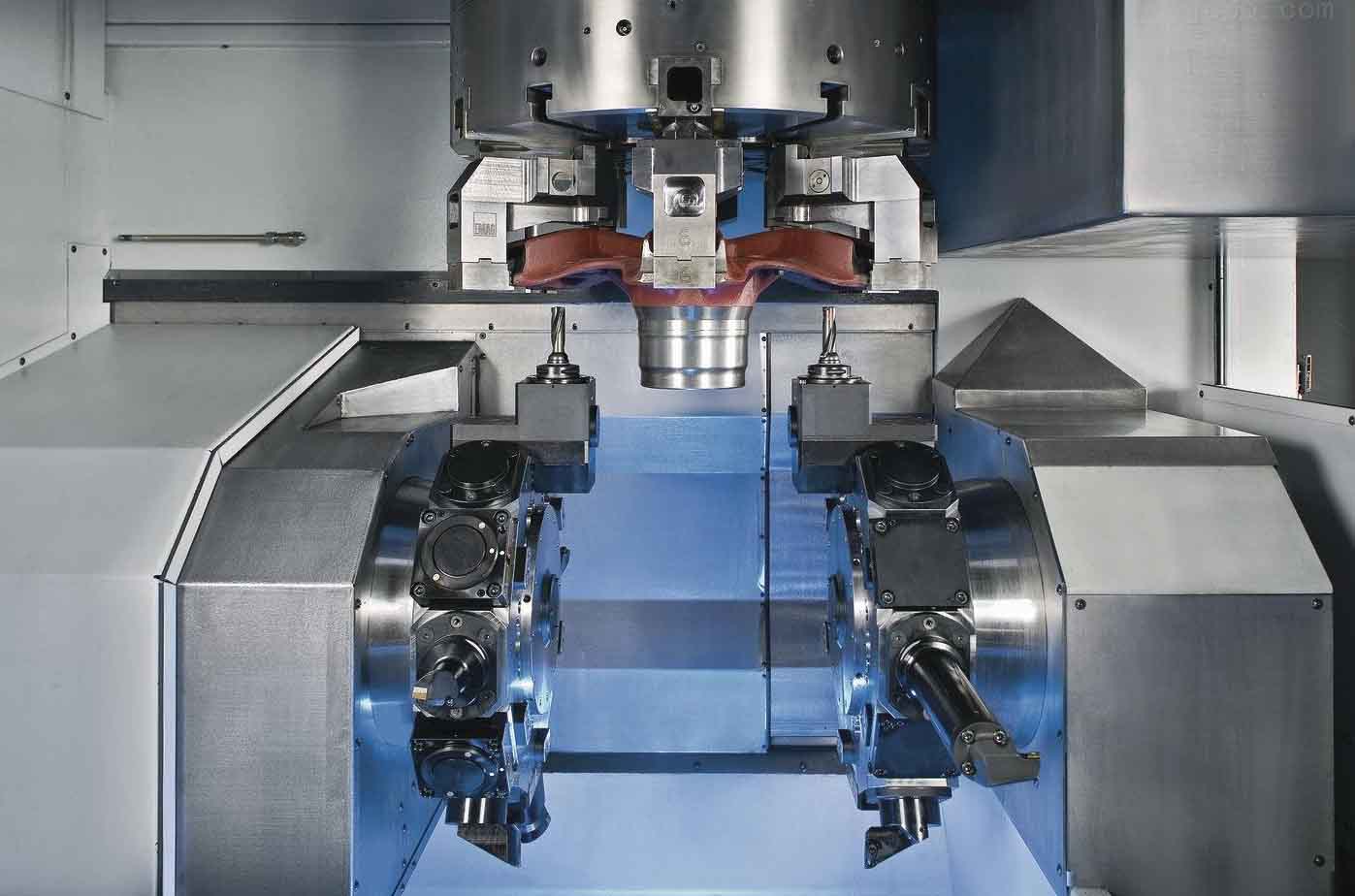
Flachräumen wird für die Bearbeitung flacher Werkstückoberflächen verwendet, um glatte Oberflächen und präzise Abmessungen zu erzielen; Konturräumen wird für die Bearbeitung komplexer Konturformen, wie Formen und Teile, verwendet; Nutenräumen wird für die Bearbeitung von Nuten und Schlitzen verwendet, wobei die Schneide in das Werkstück eindringt und entlang der Werkstückoberfläche schneidet; Lochräumen wird für die Bearbeitung der Innenkontur von Löchern verwendet, wobei die Schneide in das Loch eindringt und die Innenfläche des Lochs schneidet.
Elektroerosionsbearbeitung (EDM)
Bei der Funkenerosion werden leitende Materialien durch elektrische Entladung geschnitten und bearbeitet, um hochpräzise, komplex geformte Teile wie Formen und Werkzeuge herzustellen. Es wird häufig bei der Herstellung von Gussformen, Kunststoffspritzgussformen, Triebwerksteilen für die Luft- und Raumfahrt, medizinischen Geräten und anderen Bereichen eingesetzt. Die Funkenerosion eignet sich zum Schneiden von harten, spröden oder hochharten Werkstoffen, die sich mit herkömmlichen Bearbeitungsmethoden nur schwer schneiden lassen, z. B. Werkzeugstahl, Hartlegierungen und Titanlegierungen.
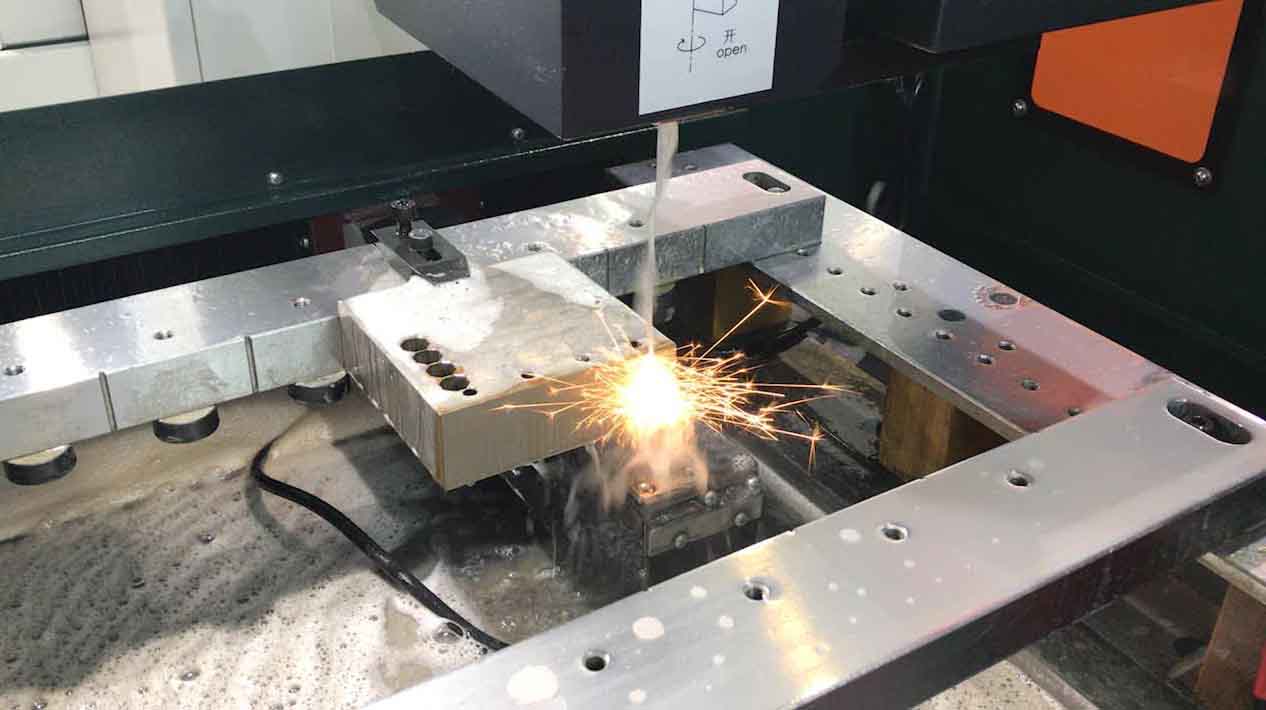
Hauptmerkmale der Funkenerosion:
EDM hat ein sehr hohes technisches Niveau in den 8 gängigen CNC-Bearbeitungstechniken.
Berührungsloses Schneiden: Im Gegensatz zur traditionellen mechanischen Zerspanung ist die Funkenerosion eine berührungslose Bearbeitungsmethode. Es gibt keinen direkten physischen Kontakt zwischen dem Werkzeug und dem Werkstück; das Material wird durch elektrische Entladung abgetragen.
Hohe Präzision: Mit der Funkenerosion lassen sich hochpräzise Bearbeitungen durchführen, die oft eine Maßgenauigkeit im Submikrometerbereich erreichen. Dadurch eignet sich das Verfahren für die Herstellung von Formen, Modellen und anderen Präzisionsteilen.
Komplexe Formen: Da es sich bei der Funkenerosion um ein berührungsloses Bearbeitungsverfahren handelt, können damit sehr komplexe Formen bearbeitet werden, darunter Innenkonturen, kleine Löcher, Schlitze und vieles mehr.
Geeignet für Materialien mit hoher Härte: Die Funkenerosion eignet sich für Werkstoffe mit hoher Härte, da sie nicht von der Härte der Schneidwerkzeuge bei herkömmlichen Schneidverfahren abhängt.
Schlussfolgerung:
Die Beherrschung der 8 gängigen CNC-Bearbeitungstechniken ist für die Präzisionsfertigung unerlässlich. Jedes dieser Verfahren hat seine spezifischen Anwendungen und Vorteile. Wenn Sie die Anwendungen und Vorteile von Drehen, Fräsen, Bohren, Schleifen, Aufbohren, Hobeln, Räumen und Erodieren kennen, können die Hersteller ihre Bearbeitungsprozesse optimieren und bessere Ergebnisse erzielen. Je nach Material, Form, Größe und Oberflächenanforderungen des Teils können wir die richtige Technik auswählen.