一般的な8つのCNC加工技術について、その用途、利点、主な特徴を知る必要がある。この記事では、旋盤加工、フライス加工、ドリル加工、研削加工、ボーリング加工、プレーニング加工、ブローチ加工、放電加工(EDM)など、必要不可欠なCNC加工技術についてご紹介します。
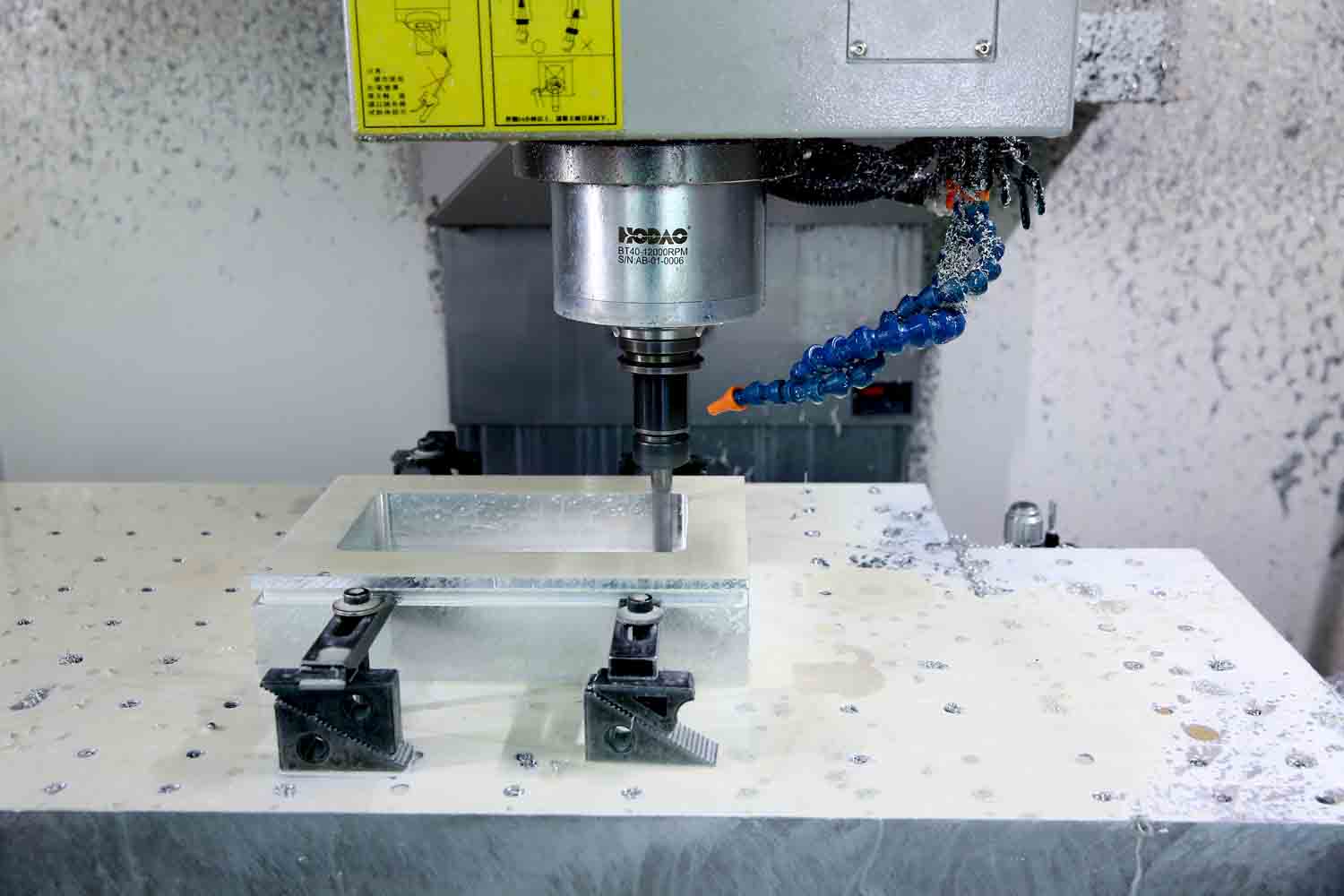
製品のコスト構造を調査するには、その製品がどのように加工されているかを調べることが非常に重要です。一般的な8つのCNC加工技術を学ぶことは、大いに役立つだろう。
製造業において、機械加工は不可欠な要素です。機械加工とは、原材料を所望の形状、サイズ、表面品質に加工するプロセスであり、さまざまな部品のニーズに対応するため、さまざまな精密加工方法があります。以下では、一般的な8つの機械加工技術について詳しく説明します。
を直接探索することもできる。 BoleのCNC機械加工サービス この分野の達人ならね。
ターニング
旋盤加工は、回転するワーク保持装置にワークを固定し、切削工具でワーク上の材料を徐々に切削して目的の形状や寸法を得る。この方法は、シャフトやスリーブなどの円筒形部品の製造に適している。旋削方法と工具の選択は、最終製品の形状と表面粗さに影響する。

旋盤加工には、外旋盤加工、内旋盤加工、フェーシング加工、ねじ切り加工などの種類がある。
外旋加工は、シャフト、シリンダー、円錐形などの形状を加工するのに一般的に使用される。内旋加工では、工具がワークの内孔に入り、直径と表面を必要なサイズと精度に加工する。フェーシングは、一般的に部品の底面や端面などの平らな面を作成するのに使用される。ねじ切り加工は、内ねじと外ねじを含め、工具の刃先をワークの表面に対して相対的に移動させ、ねじの形状を徐々に切削することで達成される。
ミーリング
フライス加工は、切削工具をワークの表面上で回転させて材料を切削するもので、工具の動きを制御することで、平面、凹面、凸面、歯車などの複雑な形状の部品を製造することができる。フライス加工には、平面フライス加工、垂直フライス加工、エンドミル加工、歯車フライス加工、プロファイルフライス加工があり、それぞれ異なる加工ニーズに適している。
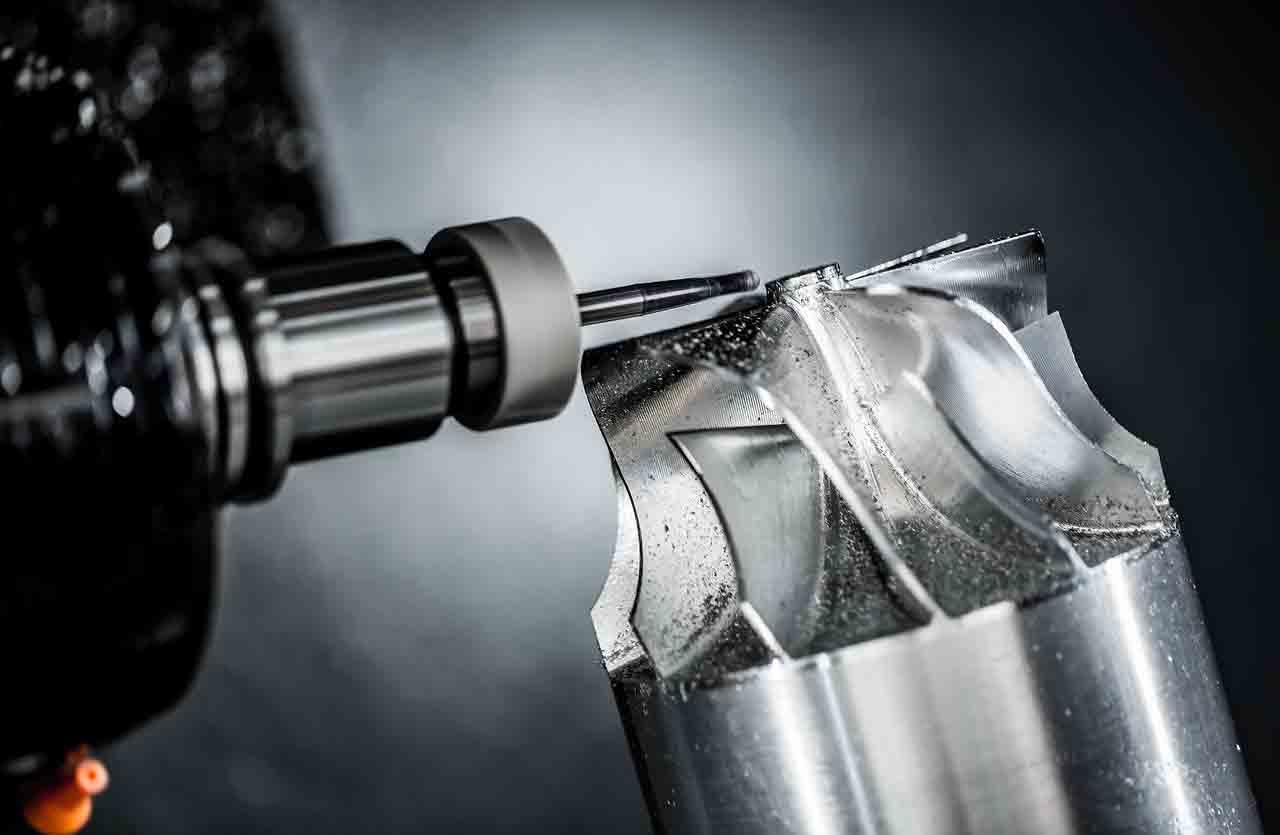
平面フライス加工では、工具の刃先がワークの表面を切削して平面を実現する。垂直フライス加工は、ワークの高さ方向に沿って溝や穴を加工するために使用される。エンドミル加工では、ワークの側面を切削し、プロファイル、溝、エッジを加工するために使用される。ギアフライス加工では、一般的に刃先を持つ特殊な工具を使用して、ギアの歯の形状を切削する。プロファイルフライス加工は、複雑な曲線や輪郭形状を加工するために使用され、輪郭に基づいて工具経路が正確に制御される。
掘削
ドリル加工は、回転するドリルビットを使って被削材を切削し、目的の直径と深さの穴を形成するもので、製造、建設、メンテナンスの分野で広く使用されている。ドリル加工は、通常ドリル加工、センタードリル加工、深穴加工、多軸ドリル加工などに分類される。

従来の穴あけ加工では、一般的に小さな穴や一般的な穴あけ加工のニーズに対応するため、らせん状の切れ刃を持つドリルビットを使用する。センタードリル加工では、大きな穴の正確な位置決めを確実にするため、大きなドリルビットを使用する前に、被加工物の表面に小さな穴を開ける。
ドリル加工は、一般的なCNC加工技術の一つとして、非常に一般的な加工方法である。
研磨
研削とは、砥粒を使用して工作物の表面を徐々に切削または研削し、所望の形状、寸法、表面品質を得ることである。研削は、金型、精密機械部品、工具など、高い精度と表面品質が要求される部品によく使われる。
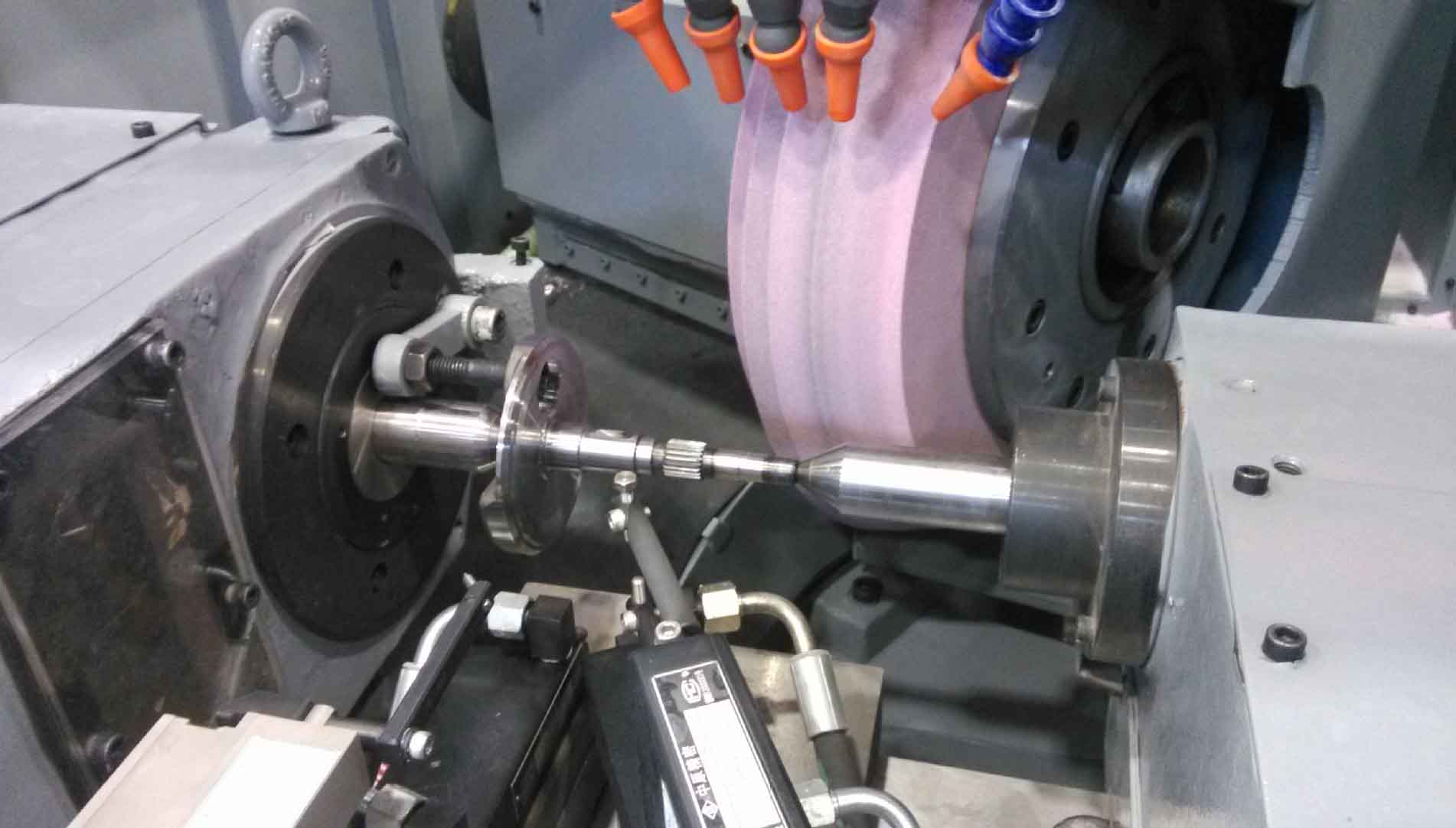
研削は平面研削、外面研削、内面研削、プロファイル研削に分けられる。平面研削は、平らな工作物の表面を加工し、滑らかな表面と正確な寸法を得るために使用される。外径研削は、シャフトやピンなどの工作物の外側の円筒面を加工するために使用される。内径研削は、内径穴や軸穴などの穴の内面を加工するために使用される。プロファイル研削は、金型や工具の刃先などの複雑な輪郭形状を加工するために使用される。
つまらない
ボーリングは、回転する工具で既存の穴を切削し、精密な寸法と平坦度の目標を達成することで、ワークピースの内部円形穴を加工するために使用される。穴あけ加工がワーク表面の材料を切削して穴を形成するのとは異なり、中ぐり加工では工具をワークピースに挿入して穴を切削する。
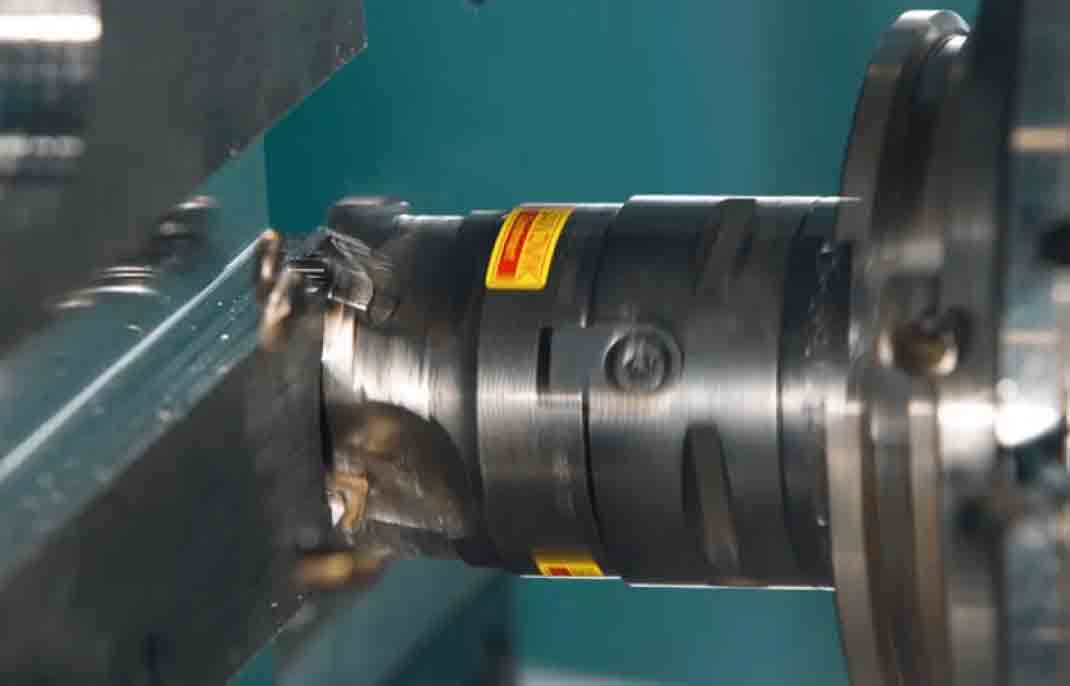
ボーリングは、手動ボーリングとCNCボーリングに分けられる。手動ボーリングは少量生産や単純な加工に適しており、CNCボーリングはプログラミングによって切削経路、送り速度、回転速度を決定し、高精度の自動加工を実現する。
プレーニング
プレーニングは、プレーナーを使用してワークピース表面の材料を切削し、所望の平坦面、正確な寸法、表面品質を実現する。プレーニングは、ベースやベッドなど、大きなワークピースの平らな表面を加工するために一般的に使用されます。これは、ワークピースが他のコンポーネントと適合するための平らな表面を提供します。
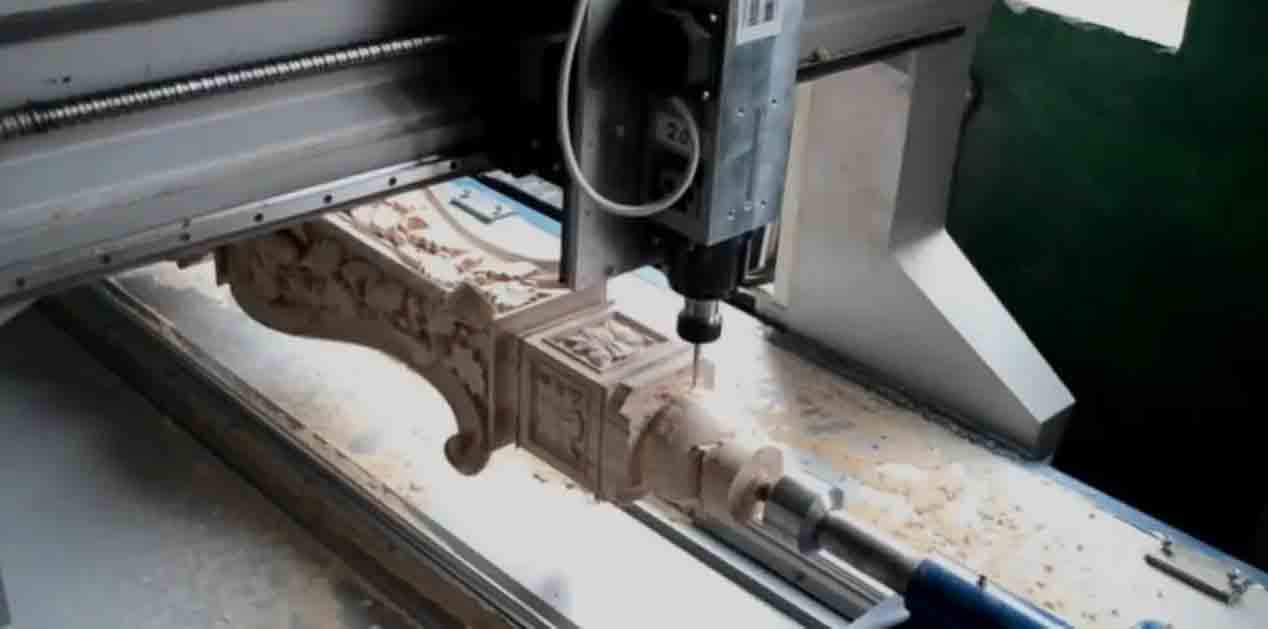
プレーニングは通常、荒削り段階と仕上げ段階に分けられる。荒削り段階では、プレーナーは材料を素早く除去するために深く切削する。仕上げ段階では、より高い表面品質と寸法精度を得るために、切削深さを浅くします。プレーニングには、手動と自動がある。手動プレーニングは、少量生産や単純な加工作業に適しています。自動プレーニングは、自動工作機械を使用してプレーナーの動きを制御し、より安定した効率的な加工プロセスを実現します。
ブローチ加工
ブローチ加工は、ブローチ工具を使用して徐々に切り込みを深くし、内部の複雑な輪郭を形成するもので、一般的に複雑な形状のワークの輪郭、溝、穴の加工に使用される。ブローチ加工は、高い加工精度と表面品質を達成することができ、高精度と良好な表面品質を必要とする部品に適している。一般的に、平面ブローチ加工、輪郭ブローチ加工、溝ブローチ加工、穴ブローチ加工に分類される。
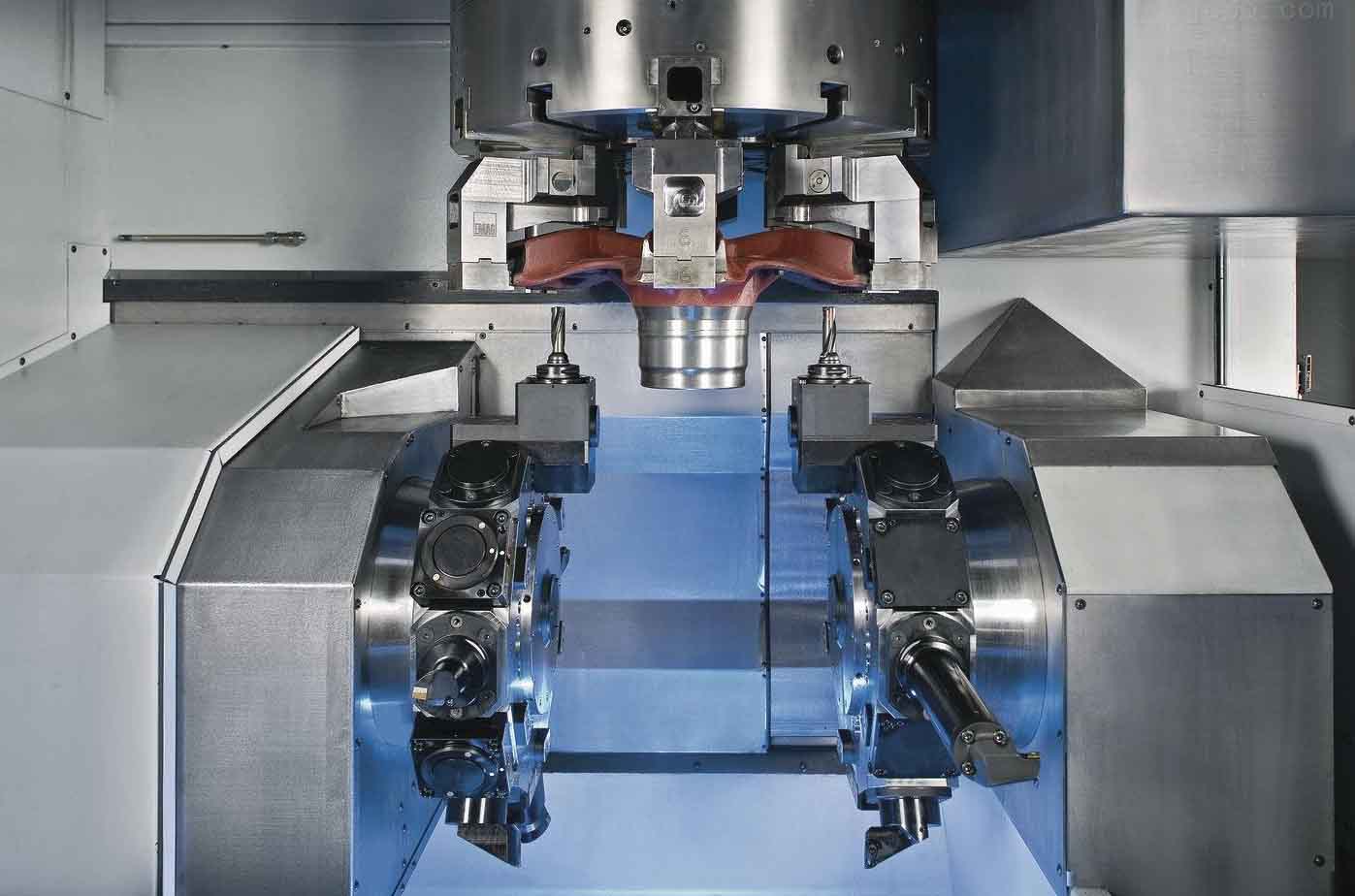
フラットブローチ加工は、平らな被加工物の表面を加工し、滑らかな表面と正確な寸法を得るために使用される。輪郭ブローチ加工は、金型や部品のような複雑な輪郭形状の加工に使用される。溝ブローチ加工は、溝やスロットの加工に使用され、刃先が被加工物に入り、被加工物の表面に沿って切削する。穴ブローチ加工は、穴の内側の輪郭の加工に使用され、刃先が穴に入り、穴の内面を切削する。
放電加工イーディーエム)
放電加工は、放電を利用して導電性材料を切断・加工し、金型や工具などの高精度で複雑な形状の部品を作る。金型、プラスチック射出成形金型、航空宇宙エンジン部品、医療機器などの製造によく使われている。放電加工は、工具鋼、硬質合金、チタン合金など、従来の加工方法では加工が困難な硬い材料、脆い材料、高硬度材料の切断に適している。
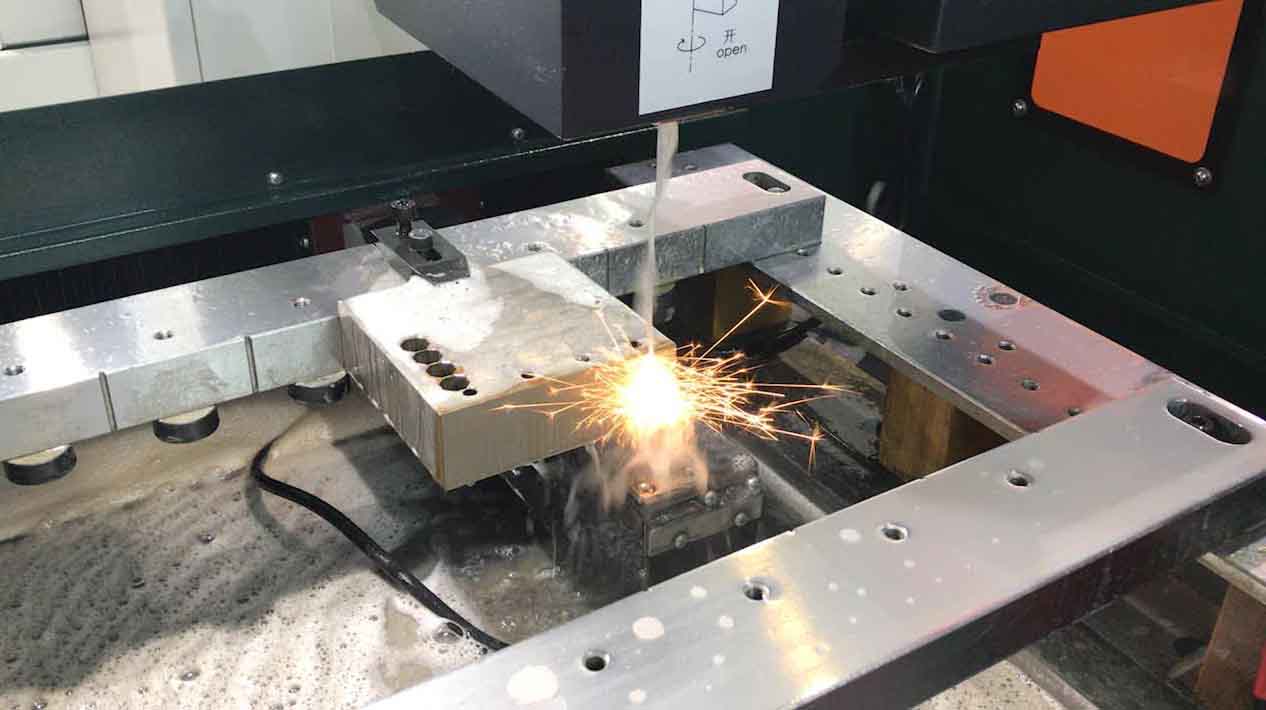
放電加工の主な特徴
EDMは、8つの一般的なCNC加工技術において、非常に高い技術レベルを持っている。
非接触切断: 従来の機械切削とは異なり、EDMは非接触加工法である。工具と被加工物が直接物理的に接触することはなく、材料は放電によって除去されます。
高精度: EDMは高精度の加工が可能で、サブミクロンレベルの寸法精度に達することも多い。そのため、金型や模型などの精密部品の製造に適している。
複雑な形状: EDMは非接触加工法であるため、内部輪郭、小さな穴、スロットなど、非常に複雑な形状の加工に使用できる。
高硬度材料に適している: EDMは、従来の切削方法における切削工具の硬度に依存しないため、高硬度材料に適している。
結論
一般的な8つのCNC加工技術をマスターすることは、精密製造に不可欠である。それぞれに特有の用途と利点があります。旋盤加工、フライス加工、ドリル加工、研削加工、ボーリング加工、プレーニング加工、ブローチ加工、放電加工の用途と利点を理解することで、メーカーは加工プロセスを最適化し、優れた結果を得ることができます。部品の材質、形状、サイズ、表面の要求に応じて、適切な技術を選択することができます。